Zarządzanie pomieszczeniami czystymi – [Perspektywa praktyka]

Wstęp dotyczący pomieszczeń czystych
Jako ekspert z blisko 20-letnim doświadczeniem w zarządzaniu pomieszczeniami czystymi, miałem okazję obserwować ewolucję standardów i praktyk w tej dziedzinie. W naszym zakładzie produkcyjnym funkcjonują pomieszczenia czyste klasy ISO 8, ISO 7 i ISO 5, co pozwoliło mi zdobyć kompleksową wiedzę na temat ich specyfiki i wymagań. Pomieszczenia czyste typu clean room to niezwykle złożone środowiska, gdzie nawet najmniejsze detale mają ogromne znaczenie. Prawa fizyki, które działają „w tle” tych przestrzeni, są fundamentem ich prawidłowego funkcjonowania. W tym artykule podzielę się moimi spostrzeżeniami i doświadczeniami, które mogą być cenne dla osób zarządzających pomieszczeniami czystymi klasyfikowanymi wg normy ISO 14644-1, szczególnie tych mniej doświadczonych.
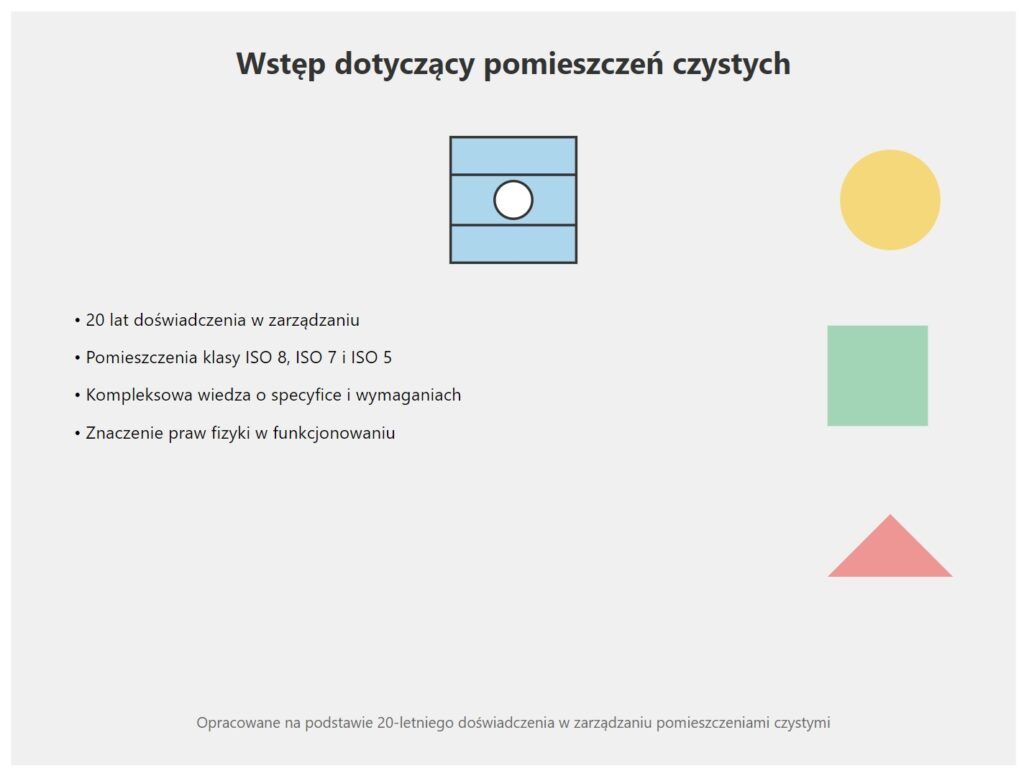
Zakres stosowania wytycznych dla pomieszczeń czystych
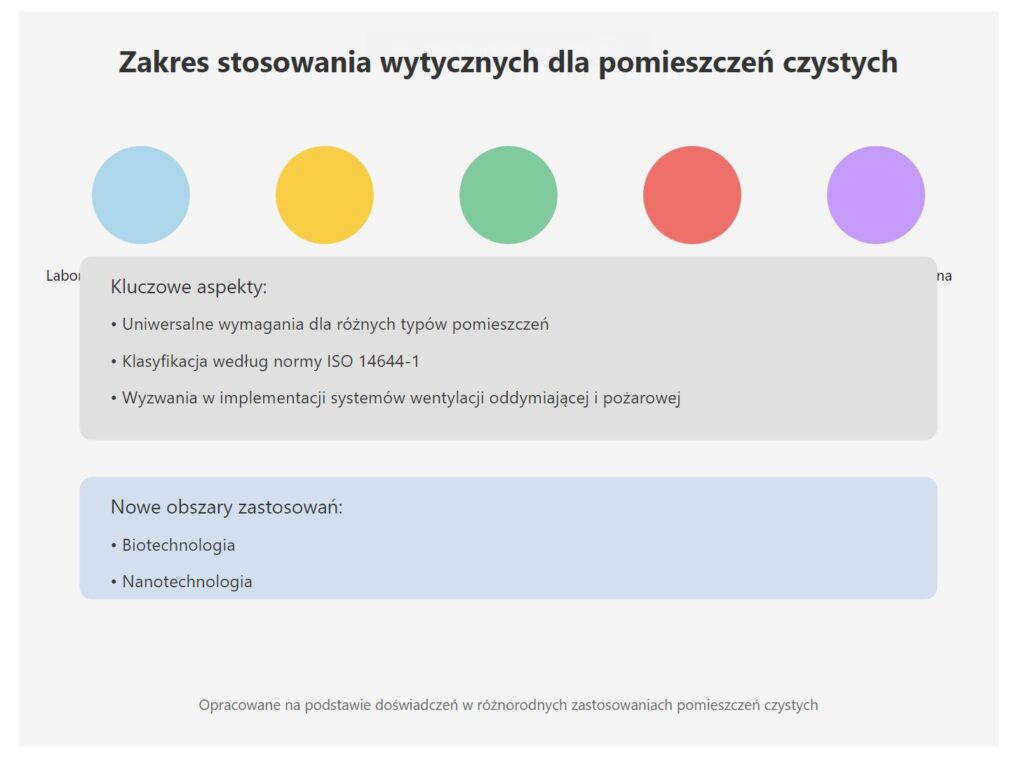
W mojej karierze miałem do czynienia z różnorodnymi zastosowaniami pomieszczeń czystych. Nasze wytyczne obejmują projektowanie, odbiór i eksploatację systemów wentylacji i klimatyzacji w pomieszczeniach czystych stosowanych w laboratoriach mikrobiologicznych, optycznych, a także w pomieszczeniach produkcyjnych o podwyższonej higienie w branżach spożywczej, farmaceutycznej i kosmetycznej. Nie można też zapomnieć o firmach produkcyjnych w przemyśle elektronicznym i optycznym.
Z mojego doświadczenia wynika, że kluczowe jest zrozumienie, iż wymagania dla pomieszczeń czystych są uniwersalne i można je zastosować nie tylko do głównych pomieszczeń produkcyjnych, ale także do śluz, korytarzy oraz innych pomieszczeń funkcjonujących jako pomieszczenia czyste. Wszystkie te przestrzenie muszą być klasyfikowane według normy ISO 14644-1, co zapewnia spójność i przewidywalność w całym zakładzie.
W praktyce, najtrudniejsze do wdrożenia okazały się często wymagania dotyczące systemów wentylacji oddymiającej i pożarowej. Zapewnienie odpowiedniej ochrony przeciwpożarowej przy jednoczesnym utrzymaniu czystości powietrza było zawsze wyzwaniem, które wymagało ścisłej współpracy z ekspertami od bezpieczeństwa pożarowego.
Co ciekawe, z biegiem lat zauważyłem, że pomieszczenia czyste są coraz częściej wykorzystywane w nowych, innowacyjnych branżach. Na przykład, w ostatnim czasie obserwuję rosnące zainteresowanie pomieszczeniami czystymi w sektorze biotechnologii i nanotechnologii. To pokazuje, jak ważne jest ciągłe dostosowywanie naszych praktyk do zmieniających się potrzeb przemysłu.
Podstawowe zalecenia dla pomieszczeń czystych
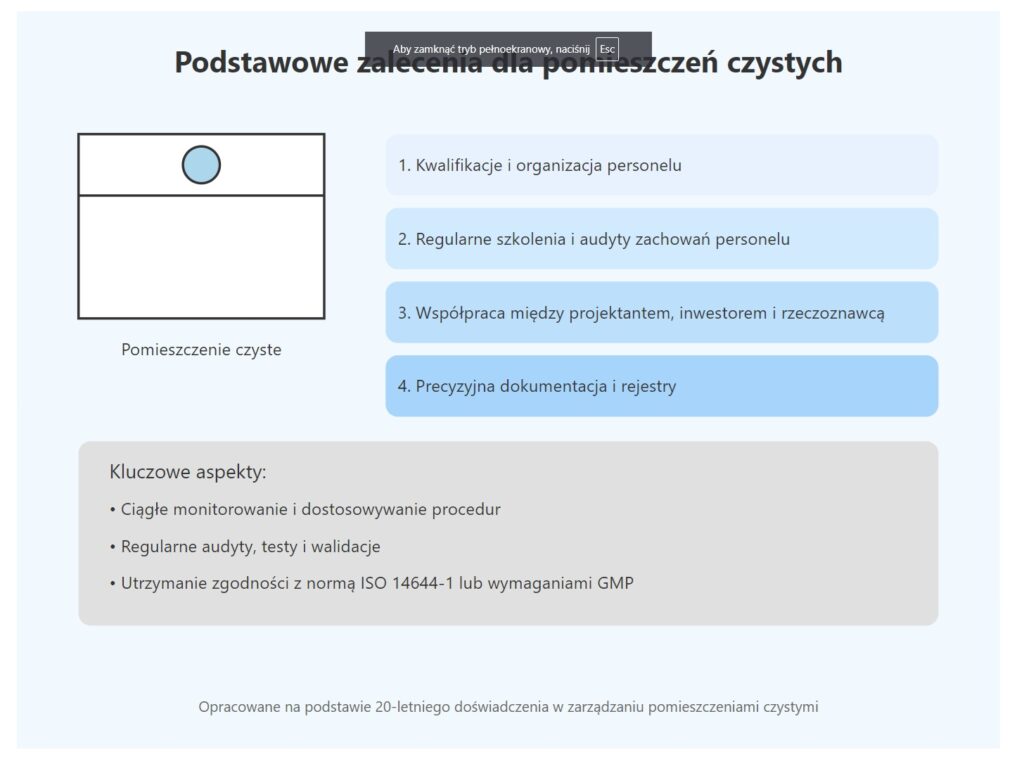
W trakcie mojej 20-letniej kariery w zarządzaniu pomieszczeniami czystymi, zrozumiałem, że utrzymanie wysokiej czystości powietrza to znacznie więcej niż tylko technologia. To złożony proces, który wymaga zaangażowania i dyscypliny wszystkich zaangażowanych osób.
Kluczowym elementem, który często jest niedoceniany, są kwalifikacje i organizacja personelu. W naszym zakładzie wprowadziliśmy rygorystyczny program szkoleń dla wszystkich pracowników, którzy mają dostęp do pomieszczeń czystych. Obejmuje on nie tylko procedury wejścia i wyjścia, ale także zasady zachowania się wewnątrz pomieszczenia czystego. Z mojego doświadczenia wynika, że nawet najlepiej zaprojektowany system wentylacji i klimatyzacji może być nieefektywny, jeśli personel nie przestrzega ściśle ustalonych procedur.
Jednym z największych wyzwań, z jakimi się spotkałem, było przekonanie kierownictwa do inwestycji w regularne szkolenia i audyty zachowań personelu. Początkowo postrzegano to jako dodatkowy koszt, ale z czasem udało się udowodnić, że jest to inwestycja, która znacząco poprawia efektywność i zmniejsza ryzyko zanieczyszczeń.
Współpraca między projektantem, inwestorem i rzeczoznawcą ds. ISO 14644-1 jest absolutnie kluczowa. W naszym zakładzie wprowadziliśmy praktykę regularnych spotkań tych stron, nie tylko na etapie projektowania, ale także podczas eksploatacji pomieszczeń czystych. To pozwoliło nam na bieżąco dostosowywać nasze procedury do zmieniających się wymagań produkcyjnych i technologicznych.
Warto również zwrócić uwagę na znaczenie dokumentacji. Precyzyjne procedury, instrukcje i rejestry są niezbędne do utrzymania spójności działań w długim okresie. W naszym zakładzie wprowadziliśmy system elektronicznej dokumentacji, co znacznie ułatwiło zarządzanie i analizę danych dotyczących funkcjonowania pomieszczeń czystych.
Pamiętajmy, że pomieszczenia czyste to dynamiczne środowiska, które wymagają ciągłego monitorowania i dostosowywania. Regularne audyty, testy i walidacje są niezbędne do utrzymania wymaganego poziomu czystości zgodnie z normą ISO 14644-1 lub wymaganiami GMP.
Założenia do projektowania systemów wentylacji i klimatyzacji Cleanroom
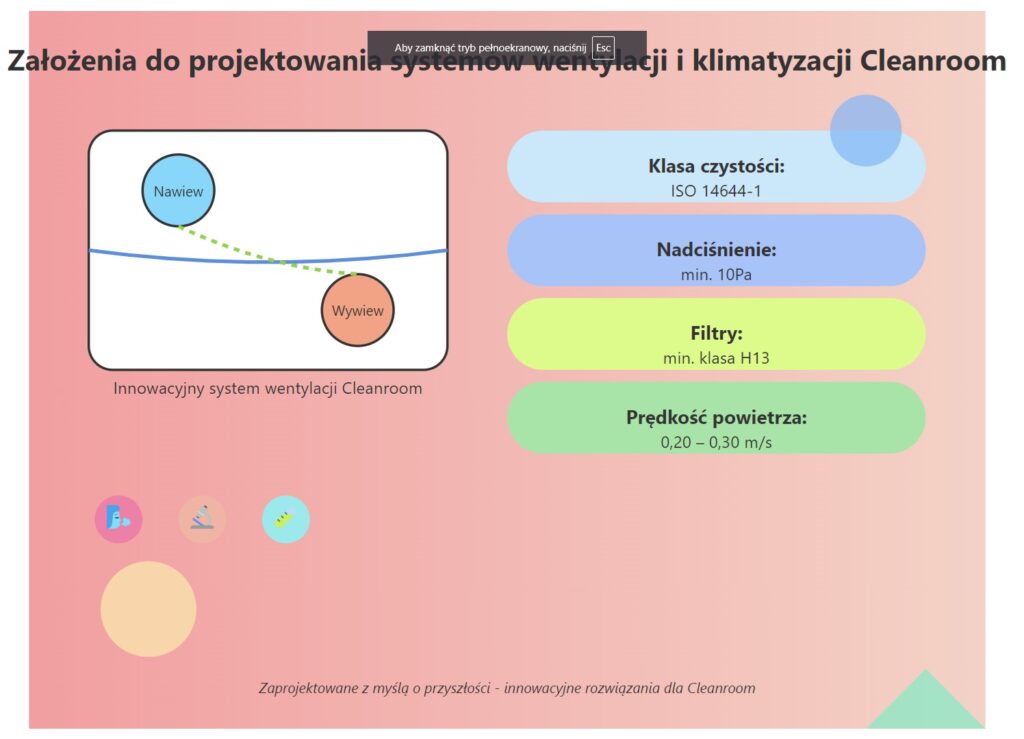
Jako ekspert z blisko 20-letnim doświadczeniem w zarządzaniu pomieszczeniami czystymi, mogę z pewnością stwierdzić, że odpowiednie zaprojektowanie systemów wentylacji i klimatyzacji jest fundamentem funkcjonowania każdego Cleanroom. W naszym zakładzie, gdzie mamy pomieszczenia klasy ISO 5, ISO 7 i ISO 8, kwestia ta jest szczególnie istotna i wymaga niezwykłej precyzji oraz uwagi do najdrobniejszych szczegółów.
Klasyfikacja pomieszczeń zgodnie z międzynarodowym standardem ISO 14644-1 jest pierwszym i kluczowym krokiem w projektowaniu systemu wentylacji i klimatyzacji. W praktyce oznacza to, że każde pomieszczenie czyste musi być dokładnie sklasyfikowane pod względem czystości powietrza, uwzględniając nie tylko cząstki stałe, ale także, w przypadku niektórych zastosowań, czystość mikrobiologiczną. To nie jest łatwe zadanie, szczególnie w przypadku pomieszczeń klasy ISO 5, gdzie wymagania są niezwykle restrykcyjne – dopuszczalna liczba cząstek o wielkości 0,5 μm na metr sześcienny powietrza jest ograniczona do zaledwie 3520.
W naszym zakładzie stosujemy rygorystyczne zalecenia dotyczące układu ciśnienia powietrza. Utrzymujemy nadciśnienie minimum 10Pa w pomieszczeniach czystych względem pomieszczeń sąsiednich. To pozwala nam skutecznie zapobiegać przedostawaniu się zanieczyszczeń z zewnątrz. Jednak utrzymanie tego nadciśnienia wymaga precyzyjnego zbalansowania systemów nawiewu i wywiewu powietrza. W praktyce oznacza to ciągłe monitorowanie i regulację przepływów powietrza, co jest jednym z najbardziej wymagających aspektów zarządzania pomieszczeniem czystym.
Kwestia filtrów wysokoskutecznych to kolejny kluczowy element, który wymaga szczególnej uwagi. W naszych pomieszczeniach czystych stosujemy filtry klasy minimum H13, które są w stanie zatrzymać 99,95% cząstek o wielkości 0,3 mikrometra. Wybór odpowiednich filtrów i ich regularna wymiana to jeden z najważniejszych elementów utrzymania czystości powietrza. Z mojego doświadczenia wynika, że warto inwestować w filtry najwyższej jakości, nawet jeśli początkowo wydaje się to droższe – w dłuższej perspektywie przekłada się to na lepszą efektywność i mniejsze ryzyko zanieczyszczeń.
Prędkość strugi powietrza to parametr, który wymaga stałej uwagi i precyzyjnej kontroli. W naszym zakładzie utrzymujemy prędkość 0,20 – 0,30 m/s w odległości 0,30 m poniżej powierzchni wylotu powietrza z nawiewu. To pozwala na skuteczne usuwanie cząstek, jednocześnie nie powodując dyskomfortu dla pracowników. Osiągnięcie i utrzymanie tej prędkości wymaga zaawansowanych systemów kontroli i regulacji, a także regularnych pomiarów i kalibracji.
Warto również zwrócić szczególną uwagę na kwestię krotności wymian powietrza. W naszych pomieszczeniach czystych utrzymujemy minimalną krotność na poziomie 25 wymian na godzinę. To zapewnia stały dopływ świeżego, przefiltrowanego powietrza i skuteczne usuwanie zanieczyszczeń. Jednak w praktyce, w zależności od specyfiki procesów prowadzonych w danym pomieszczeniu, często stosujemy wyższe krotności wymian, sięgające nawet 60-80 na godzinę w przypadku najbardziej krytycznych obszarów.
Projektując system wentylacji i klimatyzacji dla pomieszczeń czystych, nie można zapomnieć o minimalnym wymaganym strumieniu powietrza zewnętrznego. W naszym zakładzie stosujemy się do zalecenia, aby strumień ten wynosił powyżej 2000 m3/h. To pozwala na skuteczne rozcieńczanie i usuwanie zanieczyszczeń generowanych wewnątrz pomieszczenia.
Ważnym aspektem, który często jest niedoceniany, jest kwestia strumienia powietrza wywiewanego. Zgodnie z naszymi doświadczeniami i zaleceniami, strumień ten nie powinien być mniejszy niż 50% nawiewanego strumienia powietrza zewnętrznego. To pozwala na utrzymanie odpowiedniego bilansu powietrza w pomieszczeniu i zapobiega nadmiernemu gromadzeniu się zanieczyszczeń.
W praktyce, projektowanie i utrzymanie systemów wentylacji i klimatyzacji dla pomieszczeń czystych to nieustanne balansowanie między różnymi parametrami. Wymaga to nie tylko technicznej wiedzy, ale także doświadczenia i intuicji. Każde pomieszczenie czyste jest unikalne i wymaga indywidualnego podejścia, uwzględniającego specyfikę prowadzonych w nim procesów i wymagań produkcyjnych.
Zalecenia dotyczące rozwiązań systemów wentylacji i klimatyzacji
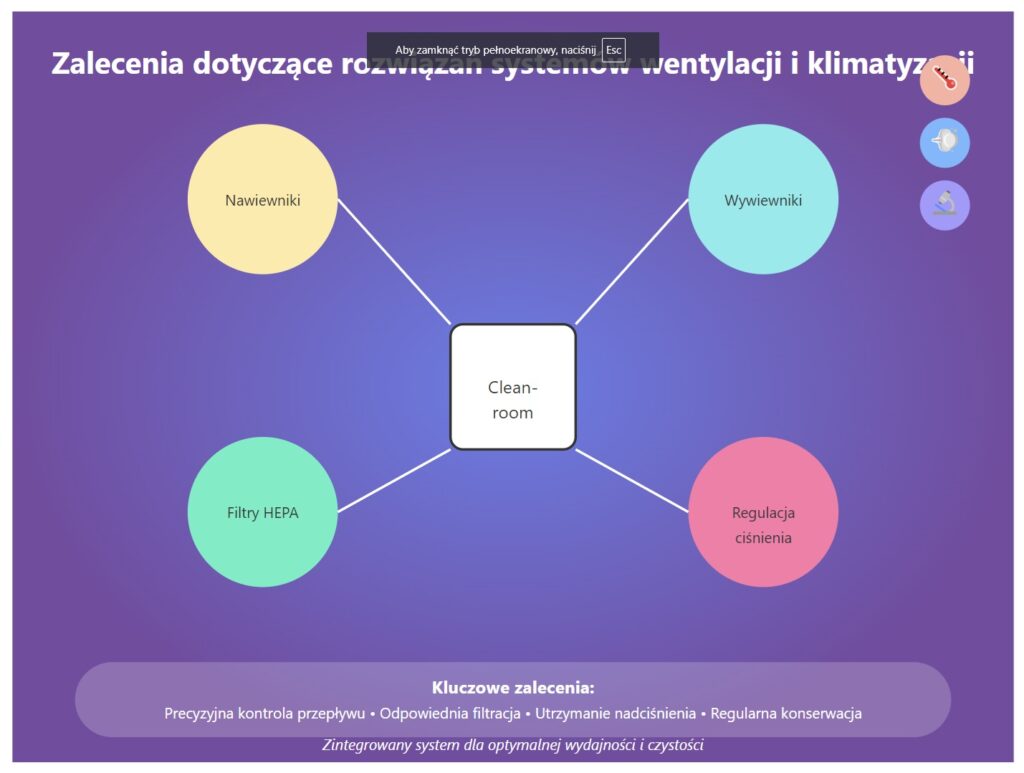
W mojej wieloletniej praktyce zarządzania pomieszczeniami czystymi, zagadnienia związane z systemami wentylacji i klimatyzacji zawsze stanowiły jeden z kluczowych obszarów uwagi. Doświadczenie nauczyło mnie, że odpowiednie zaprojektowanie i utrzymanie tych systemów jest fundamentem prawidłowego funkcjonowania każdego pomieszczenia czystego, niezależnie od jego klasy czystości według iso 14644-1.
Dla pomieszczeń sklasyfikowanych w klasach ISO 5-9, które są najczęściej spotykane w naszym zakładzie, bezwzględnie wymagane jest wyposażenie w systemy klimatyzacji i wentylacji mechanicznej nawiewno-wywiewnej. Te systemy muszą zapewniać co najmniej minimalną krotność wymiany powietrza, wymaganą czystość powietrza oraz komfort cieplny. W praktyce oznacza to, że musimy stale monitorować i kontrolować nie tylko ilość cząstek w powietrzu, ale także temperaturę i wilgotność.
Głównym zadaniem systemu wentylacji i klimatyzacji w pomieszczeniu czystym jest utrzymanie czystości powietrza. Aby to osiągnąć, stosujemy trzy kluczowe strategie. Po pierwsze, utrzymujemy nadciśnienie powietrza w stosunku do pomieszczeń przylegających. To proste, ale niezwykle skuteczne rozwiązanie zapobiega przedostawaniu się zanieczyszczeń z zewnątrz. Po drugie, zapewniamy nawiew czystego powietrza o określonej, stałej prędkości. W naszej praktyce staramy się utrzymać różnicę temperatury nawiewu i rzeczywistej temperatury w pomieszczeniu w granicach 1-3 K. To pozwala na skuteczne usuwanie zanieczyszczeń bez tworzenia niepożądanych turbulencji. Po trzecie, zapewniamy odpowiednią ilość powietrza zewnętrznego, co pozwala na rozcieńczenie ewentualnych zanieczyszczeń.
W przypadku wielu pomieszczeń czystych, szczególnie tych o wyższych klasach czystości, stosujemy system nawiewu z użyciem nawiewników sufitowych lub pełnego sufitu laminarnego. To rozwiązanie, choć kosztowne, zapewnia najwyższą skuteczność w utrzymaniu czystości powietrza. Kluczowe jest tutaj zachowanie niskiej turbulencji i odpowiedniej prędkości opadania strugi powietrza.
Jednym z największych wyzwań, z jakimi się spotykamy, jest zapewnienie odpowiedniego nadciśnienia i jednokierunkowego przepływu powietrza. W praktyce oznacza to, że musimy bardzo precyzyjnie kontrolować strumienie powietrza nawiewanego i wywiewanego, uwzględniając przy tym różnice ciśnień między poszczególnymi pomieszczeniami. To wymaga zaawansowanych systemów kontroli i regulacji, a także regularnych pomiarów i kalibracji.
W naszym zakładzie wprowadziliśmy możliwość zmniejszenia strumienia nawiewanego powietrza (minimalnie do 50% nominalnego strumienia) w czasie, gdy pomieszczenie czyste nie jest używane. To rozwiązanie pozwala na znaczne oszczędności energii, ale wymaga bardzo precyzyjnego systemu kontroli, aby nie dopuścić do utraty nadciśnienia względem pomieszczeń sąsiadujących.
Szczególną uwagę zwracamy na pomieszczenia klasy ISO 7 i niższych. W tych przypadkach nigdy nie wyłączamy całkowicie systemu wentylacji i klimatyzacji, nawet w przerwach w użytkowaniu. Doświadczenie nauczyło nas, że ponowne osiągnięcie wymaganej klasy czystości po całkowitym wyłączeniu systemu może być czasochłonne i kosztowne.
Aby uniknąć przestojów w funkcjonowaniu systemów obsługujących pomieszczenia czyste, stosujemy urządzenia redundantne. W praktyce oznacza to, że mamy zainstalowane dodatkowe wentylatory, które mogą automatycznie przejąć pracę w przypadku awarii urządzeń podstawowych. To rozwiązanie, choć zwiększa koszty inwestycyjne, okazało się niezwykle skuteczne w zapewnieniu ciągłości produkcji.
W kwestii ogrzewania pomieszczeń czystych, preferujemy stosowanie ogrzewania płaszczyznowego. W naszej praktyce okazało się ono najbardziej efektywne i najmniej zakłócające przepływ powietrza. W niektórych przypadkach stosujemy również grzejniki w wykonaniu higienicznym, ale zawsze z dużą ostrożnością, aby nie zakłócić laminarnego przepływu powietrza.
Jednym z kluczowych etapów w procesie tworzenia pomieszczenia czystego jest dokładny, komisyjny przegląd całej struktury budowlanej i instalacyjnej przed przystąpieniem do prac wykończeniowych. W naszej praktyce zawsze uczestniczą w nim inwestor, wykonawca i inspektor nadzoru budowlanego. To pozwala na wczesne wykrycie i usunięcie potencjalnych problemów, które mogłyby wpłynąć na czystość pomieszczenia.
Szczególną uwagę zwracamy na szczelność pomieszczenia. Wszystkie otwory i elementy powodujące utratę szczelności muszą być starannie uszczelnione przy użyciu środków dopuszczonych do zastosowania w pomieszczeniach czystych. To kluczowy element w utrzymaniu wymaganego nadciśnienia i zapobieganiu przedostawaniu się zanieczyszczeń z zewnątrz.
Czystość powietrza w pomieszczeniach czystych
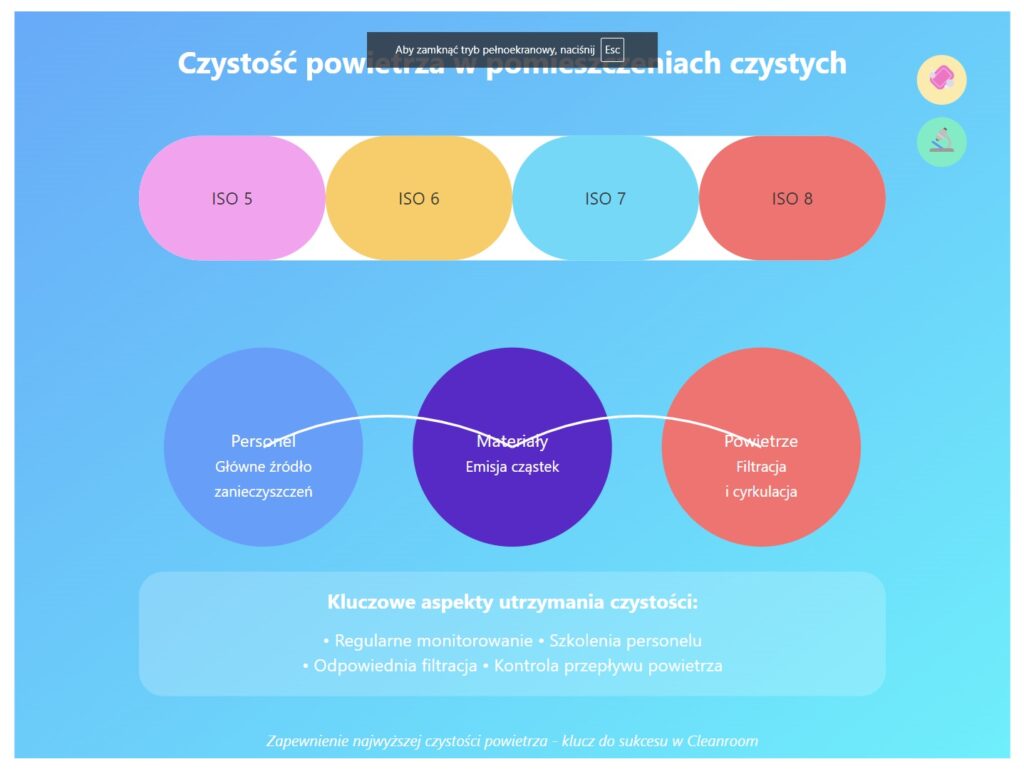
W moim 20-letnim doświadczeniu w zarządzaniu pomieszczeniami czystymi, kwestia czystości powietrza zawsze była i jest nadal kluczowym aspektem. Pomieszczenia typu clean room ISO 5-ISO 8, z którymi mam do czynienia na co dzień, to miejsca, gdzie czystość powietrza ma fundamentalne znaczenie dla prowadzonych w nich czynności produkcyjnych.
Z perspektywy praktyka mogę powiedzieć, że utrzymanie odpowiedniej czystości powietrza to nieustanne wyzwanie. Powietrze w Cleanroom ISO 5-8 może być zanieczyszczone przez różnorodne czynniki, takie jak drobnoustroje, opary surowców, cząstki stałe oraz biozanieczyszczenia. W mojej praktyce zawodowej wielokrotnie przekonałem się, że najistotniejszym źródłem mikroorganizmów i cząstek stałych są ludzie przebywający w Cleanroom. To właśnie personel stanowi główne źródło zanieczyszczeń, co czyni kwestię szkoleń i przestrzegania procedur absolutnie kluczową.
Ilość drobnoustrojów w powietrzu, a także mikrowłókien oraz cząstek stałych uwalnianych m.in. z powierzchni odzieży, zależy od liczby osób oraz intensywności ruchu. To oznacza, że musimy bardzo starannie kontrolować liczbę osób przebywających jednocześnie w pomieszczeniu czystym oraz ich aktywność. W naszym zakładzie wprowadziliśmy system monitorowania ruchu personelu, co pozwoliło nam lepiej zrozumieć i kontrolować to źródło zanieczyszczeń.
Nie można też zapominać o innych potencjalnych źródłach zanieczyszczeń. Materiały budowlane, wykończeniowe oraz wyposażenie sali mogą emitować cząstki stałe. Dlatego w naszej praktyce zawsze starannie dobieramy materiały używane w pomieszczeniach czystych, preferując te o niskiej emisyjności cząstek. Ponadto, cząstki stałe mogą również przedostać się do sali wraz z powietrzem wentylacyjnym, co podkreśla znaczenie odpowiedniej filtracji powietrza nawiewanego.
W praktyce, czystość powietrza określamy definiując dopuszczalne stężenie cząstek stałych o danych wymiarach oraz dopuszczalne stężenie drobnoustrojów w powietrzu. To dwutorowe podejście, uwzględniające zarówno czystość pyłową, jak i mikrobiologiczną, okazało się w mojej praktyce najbardziej skuteczne.
Określenie czystości pyłowej powietrza według normy ISO 14644-1 jest standardową procedurą, którą wykonujemy w trakcie odbioru instalacji lub po jej modernizacji. Jednak z doświadczenia wiem, że samo określenie dopuszczalnej ilości cząstek pyłowych nie jest wystarczające. Ilość zanieczyszczeń w powietrzu zależy bowiem od sposobu i intensywności wykorzystania pomieszczeń, dlatego konieczne jest uzupełnienie tych pomiarów o badania mikrobiologiczne.
W naszej praktyce, czystość mikrobiologiczną powietrza określamy w trakcie rutynowego użytkowania oraz bezpośrednio po skończeniu produkcji. To drugie podejście pozwala nam wykluczyć instalację wentylacji jako dodatkowe źródło zanieczyszczeń mikrobiologicznych. Te badania okazały się kluczowe w identyfikacji potencjalnych problemów i optymalizacji naszych procedur czyszczenia i dezynfekcji.
Warto podkreślić, że utrzymanie odpowiedniej czystości powietrza wymaga ciągłego monitoringu i szybkiej reakcji na wszelkie odchylenia od norm. W naszym zakładzie wprowadziliśmy system ciągłego monitoringu cząstek w powietrzu, co pozwala nam na natychmiastową reakcję w przypadku przekroczenia dopuszczalnych poziomów. To rozwiązanie, choć kosztowne, okazało się niezwykle skuteczne w zapewnieniu stabilności procesu produkcyjnego.
Jednym z największych wyzwań, z jakimi się spotkałem, była kwestia równowagi między utrzymaniem czystości powietrza a komfortem pracowników. Zbyt rygorystyczne procedury mogą prowadzić do spadku efektywności pracy, dlatego kluczowe jest znalezienie odpowiedniego balansu. W naszej praktyce staramy się projektować procedury i systemy w taki sposób, aby były one jak najmniej uciążliwe dla personelu, jednocześnie zapewniając wymaganą czystość powietrza.
Podsumowując, utrzymanie odpowiedniej czystości powietrza w pomieszczeniach czystych to złożone zadanie, wymagające kompleksowego podejścia. Kluczowe jest zrozumienie wszystkich potencjalnych źródeł zanieczyszczeń, wdrożenie odpowiednich systemów monitoringu i kontroli, a także ciągłe szkolenie personelu. Tylko takie holistyczne podejście pozwala na skuteczne zarządzanie czystością powietrza w pomieszczeniach czystych zgodnie z wymaganiami normy ISO 14644-1.
Czystość pyłowa powietrza w pomieszczeniach czystych
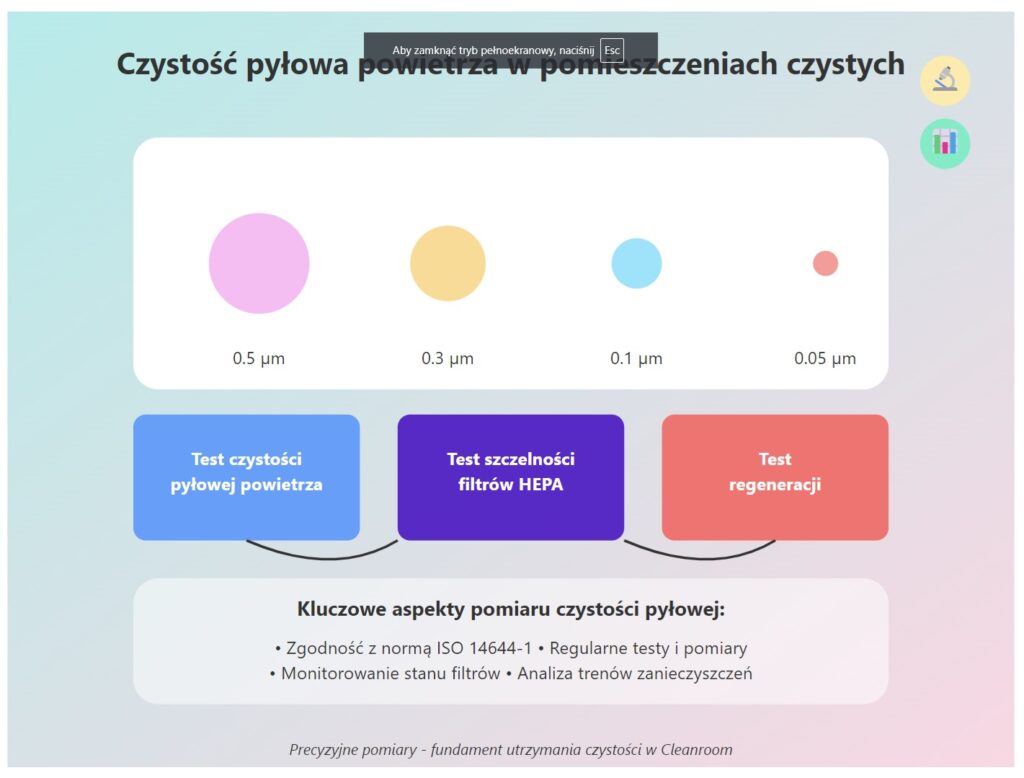
W mojej wieloletniej praktyce zarządzania pomieszczeniami czystymi, kwestia czystości pyłowej powietrza zawsze stanowiła jeden z kluczowych obszarów zainteresowania. Zgodnie z normą PN-EN ISO 14644-1, czystość powietrza w pomieszczeniach czystych i strefach czystych określana jest ze względu na liczbę cząstek pyłu w powietrzu jako klasa N ISO, gdzie N to odpowiedni numer klasy.
Z mojego doświadczenia wynika, że zrozumienie i prawidłowe stosowanie tej klasyfikacji jest fundamentem skutecznego zarządzania pomieszczeniem czystym. W naszym zakładzie, gdzie mamy do czynienia z pomieszczeniami klasy ISO 5, ISO 7 i ISO 8, precyzyjne określenie i utrzymanie odpowiedniej klasy czystości jest kluczowe dla zapewnienia jakości naszych produktów.
Warto zaznaczyć, że wielu specjalistów w branży nadal posługuje się klasami czystości zgodnymi z amerykańską normą Fed-Std-209. Choć nie jest to już standard obowiązujący, znajomość tej klasyfikacji okazuje się przydatna w komunikacji z partnerami z USA lub przy pracy ze starszymi systemami.
Metodyka pomiarów w pomieszczeniach czystych
W celu potwierdzenia uzyskania wymaganej czystości pyłowej powietrza dla pomieszczeń ISO 5 do ISO 8 wg iso 14644 (lub A /D gmp), w naszej praktyce przeprowadzamy trzy kluczowe testy:
- Test czystości pyłowej powietrza
- Test szczelności zamocowania i integralności filtrów HEPA
- Test regeneracji
Wszystkie te testy przeprowadzamy podczas odbiorów instalacji, a w szczególnych przypadkach również podczas rozruchu oraz po dłuższych przerwach w pracy instalacji. Z mojego doświadczenia wynika, że regularne przeprowadzanie tych testów jest kluczowe dla utrzymania wymaganej klasy czystości.
Warto podkreślić, że wymagania dotyczące czystości pyłowej odnoszą się do pomieszczeń czystych w stanie spoczynku, czyli gdy instalacje są całkowicie wykonane, aparatura zainstalowana i gotowa do pracy, ale bez obecności personelu. To ważne rozróżnienie, ponieważ obecność personelu znacząco wpływa na poziom zanieczyszczeń.
W praktyce, przy określaniu klasy czystości, musimy pamiętać o niedokładnościach procesu pomiarowego. Dlatego wyniki stężenia wykorzystywane do określenia klasy czystości powinny być liczbami o nie więcej niż trzech cyfrach znaczących. To pozwala na uwzględnienie pewnego marginesu błędu i zapewnia bardziej realistyczne podejście do klasyfikacji pomieszczeń.
Test szczelności zamocowania i integralności filtrów wysokoskutecznych
Ten test jest kluczowy dla zapewnienia efektywności systemu filtracji. W naszej praktyce przeprowadzamy go zgodnie z zaleceniami normy PN-EN ISO 14644-3. Test ten pozwala nam ocenić nie tylko szczelność zamocowania filtrów, ale także jednorodność materiału filtracyjnego. Z mojego doświadczenia wynika, że nawet niewielkie nieszczelności w systemie filtracji mogą znacząco wpłynąć na czystość powietrza w pomieszczeniu.
Test regeneracji
Test regeneracji, który przeprowadzamy zgodnie z normą PN-EN ISO 14644-3, jest szczególnie istotny dla pomieszczeń klasy ISO 5 i ISO 8. Polega on na pomiarze czasu powrotu stężenia cząstek pyłu do stężenia właściwego dla danej klasy, po wprowadzeniu zanieczyszczenia 100 razy powyżej tego poziomu.
W praktyce, test ten daje nam cenne informacje o zdolności systemu wentylacji do usuwania zanieczyszczeń. Z mojego doświadczenia wynika, że wyniki tego testu mogą być bardzo pomocne w optymalizacji procedur czyszczenia i dezynfekcji pomieszczenia po incydentach związanych z nadmiernym zanieczyszczeniem.
Podsumowując, utrzymanie odpowiedniej czystości pyłowej powietrza w pomieszczeniach czystych wymaga systematycznego podejścia, regularnych testów i ciągłego monitoringu. Tylko takie kompleksowe podejście pozwala na skuteczne zarządzanie czystością powietrza zgodnie z wymaganiami normy ISO 14644-1 i zapewnienie optymalnych warunków dla procesów produkcyjnych.
Czystość mikrobiologiczna powietrza w pomieszczeniach czystych
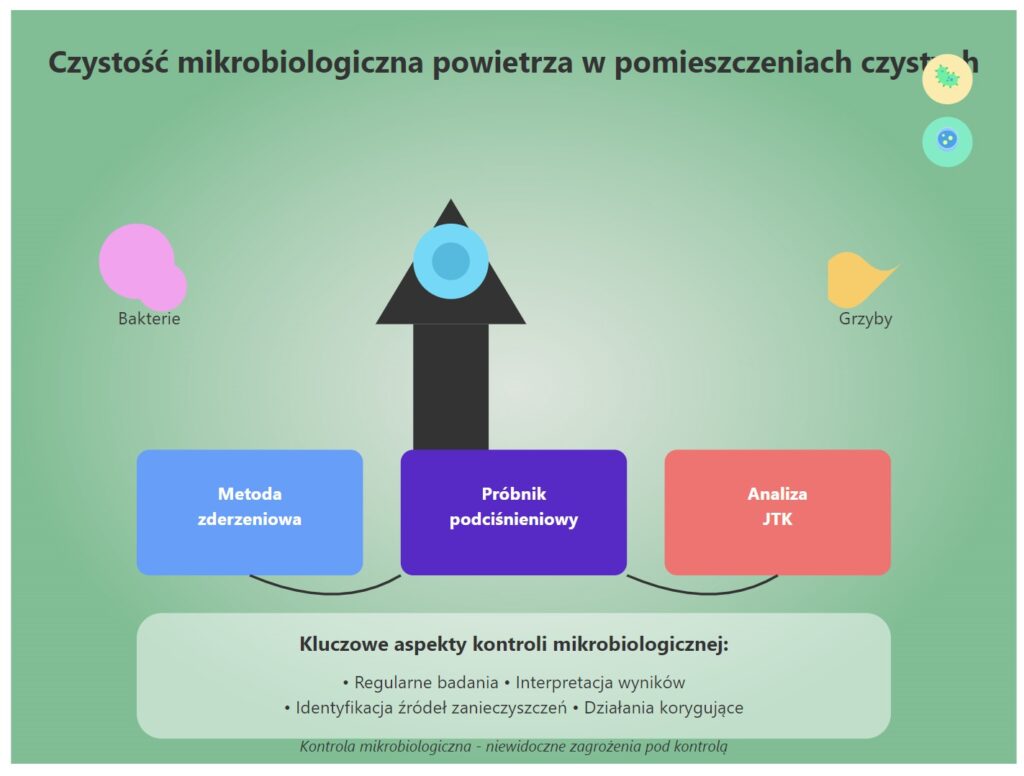
W mojej wieloletniej praktyce zarządzania pomieszczeniami czystymi, kontrola czystości mikrobiologicznej powietrza zawsze stanowiła jedno z największych wyzwań. Testy mikrobiologiczne powietrza w Cleanroom wykonujemy w celu oceny stopnia obciążenia pomieszczenia czystego mikroorganizmami zdolnymi do rozmnażania. To kluczowy element zapewnienia bezpieczeństwa i jakości procesów produkcyjnych, szczególnie w branżach takich jak farmaceutyka czy produkcja żywności.
W naszej praktyce stosujemy skalę oceny poziomu zanieczyszczeń mikrobiologicznych w jednostkach JTK (jednostki tworzące kolonie). To podejście pozwala nam na precyzyjne określenie liczby żywych mikroorganizmów obecnych w powietrzu, co jest znacznie bardziej miarodajne niż sama ocena ilości cząstek.
Nasze doświadczenie pokazuje, że testy mikrobiologiczne w Cleanroom powinny być wykonywane regularnie w kilku kluczowych sytuacjach:
- W trakcie eksploatacji, aby monitorować czystość powietrza podczas trwania produkcji.
- Po każdej wymianie filtrów wysokoskutecznych, co pozwala nam upewnić się, że nowe filtry działają prawidłowo i nie wprowadzają dodatkowych zanieczyszczeń.
- Po upływie 2 lat od wymiany filtrów wysokoskutecznych, w celu ewentualnego wydłużenia czasu ich eksploatacji.
- Po zdarzeniach losowych powodujących dłuższy przestój pracy instalacji.
W naszym zakładzie do oceny czystości mikrobiologicznej powietrza stosujemy metodę zderzeniową z zastosowaniem próbnika podciśnieniowego (metoda szczelinowa). Z mojego doświadczenia wynika, że ta metoda zapewnia najbardziej wiarygodne i powtarzalne wyniki.
Warto zaznaczyć, że interpretacja wyników testów mikrobiologicznych wymaga dużego doświadczenia. Uzyskana w badaniach szczególnie wysoka liczebność kolonii w obszarze pomieszczenia czystego nie zawsze musi wskazywać na nieprawidłowości działania systemu wentylacji i klimatyzacji. Może ona wynikać ze wzrostu emisji drobnoustrojów pochodzących od personelu przebywającego w Cleanroom oraz obecności dodatkowych osób. To kolejny argument za tym, jak ważne jest ograniczenie liczby osób w pomieszczeniu czystym i przestrzeganie rygorystycznych procedur higienicznych.
Jednak jeśli przy powtarzalnym korzystaniu z pomieszczenia czystego następuje wzrost obciążenia mikrobiologicznego, może to wskazywać na nieprawidłowości w działaniu systemu wentylacji i klimatyzacji. W takich przypadkach zawsze przeprowadzamy dodatkowe testy, w tym pomiar w Cleanroom w stanie spoczynku, aby zidentyfikować źródło problemu.
Metodyka pomiarów w pomieszczeniach klasy ISO 5 i ISO 8
W naszym zakładzie metodyka pomiarów mikrobiologicznych jest określana przez kierownika laboratorium mikrobiologicznego. To zapewnia nam spójność i rzetelność wyników. Badania czystości powietrza pod względem zanieczyszczeń mikrobiologicznych przeprowadzamy w trakcie produkcji, przy pracującej instalacji klimatyzacji.
Kluczowe jest zapewnienie ustalonych warunków mikroklimatu podczas pomiaru. W naszej praktyce utrzymujemy temperaturę w zakresie 19-23°C i wilgotność względną w zakresie 30-65%. To pozwala nam na uzyskanie powtarzalnych i miarodajnych wyników.
Do pobierania próbek używamy podciśnieniowego próbnika powietrza zawierającego płytkę lub pasek osadczy z odpowiednim podłożem. Standardowo pobieramy próbkę powietrza o objętości 1 m3 w minimum 4 równomiernie rozłożonych punktach pomiarowych, na wysokości 1,20 m nad poziomem podłogi. To zapewnia nam reprezentatywny obraz czystości mikrobiologicznej w całym pomieszczeniu.
Warto podkreślić, że w badanym powietrzu nie mogą znajdować się drożdżaki oraz grzyby pleśniowe. To bardzo rygorystyczne wymaganie, ale z naszego doświadczenia wynika, że jest ono kluczowe dla zapewnienia bezpieczeństwa procesów produkcyjnych.
W przypadku wyników wskazujących na występowanie zanieczyszczeń mikrobiologicznych, zawsze przeprowadzamy dodatkowe badanie czystości mikrobiologicznej powietrza nawiewanego do pomieszczenia czystego podczas nieobecności personelu. To pozwala nam wyeliminować podejrzenie wprowadzania zanieczyszczeń przez układ wentylacji i klimatyzacji.
Podsumowując, kontrola czystości mikrobiologicznej powietrza w pomieszczeniach czystych to złożony proces wymagający systematycznego podejścia i dużego doświadczenia. Regularne testy, prawidłowa interpretacja wyników i szybka reakcja na wszelkie odchylenia są kluczowe dla utrzymania wymaganej czystości zgodnie z normą ISO 14644-1 i zapewnienia bezpieczeństwa procesów produkcyjnych.
Temperatura i wilgotność względna powietrza w pomieszczeniach czystych
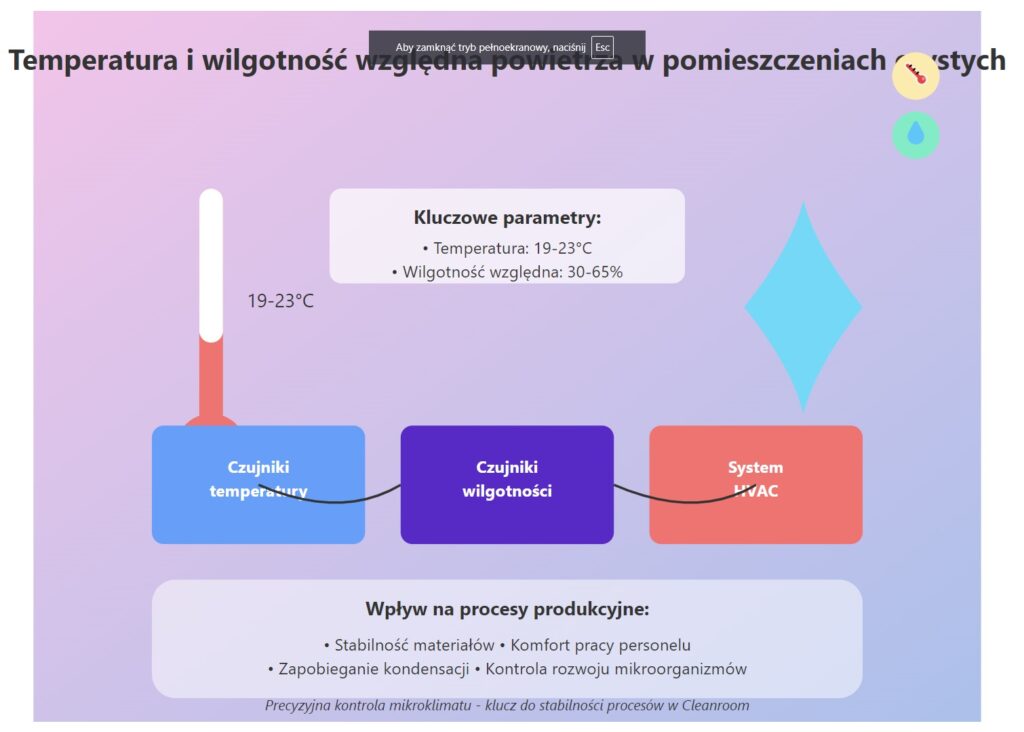
W trakcie mojej 20-letniej kariery w zarządzaniu pomieszczeniami czystymi, kontrola temperatury i wilgotności względnej powietrza zawsze stanowiła jeden z kluczowych aspektów utrzymania odpowiednich warunków w Cleanroom. Te parametry nie tylko wpływają na komfort pracy personelu, ale również mają istotne znaczenie dla procesów produkcyjnych i stabilności materiałów.
Dla pomieszczeń czystych ISO 8, które stanowią znaczną część naszego zakładu, przyjęliśmy następujące parametry projektowe powietrza wewnętrznego, niezależnie od warunków zewnętrznych:
- Temperatura powietrza regulowana w zakresie: 19-23°C
- Wilgotność względna z zakresu 30-65%
Te zakresy okazały się optymalne dla większości naszych procesów produkcyjnych. Jednakże, z mojego doświadczenia wynika, że w niektórych przypadkach konieczne jest przyjęcie innych wartości temperatury i wilgotności. Na przykład, w naszym laboratorium mikrobiologicznym musieliśmy dostosować te parametry do specyficznych wymagań hodowli bakterii.
W takich sytuacjach zawsze ściśle współpracujemy z projektantem, inwestorem i rzeczoznawcą budowlanym z zakresu wentylacji i klimatyzacji. Każde odstępstwo od standardowych wartości musi być dokładnie uzasadnione i udokumentowane. To podejście pozwoliło nam uniknąć wielu potencjalnych problemów w przyszłości.
Dla pomieszczeń czystych kluczowe jest również utrzymanie odpowiedniej temperatury powietrza nawiewanego. Musi ona być zgodna z zaleceniami producenta nawiewników i jednocześnie zapewniać utrzymanie komfortu cieplnego w pomieszczeniu czystym. W naszej praktyce okazało się, że różnica temperatury między powietrzem nawiewanym a temperaturą w pomieszczeniu nie powinna przekraczać 2-3°C. Większe różnice mogą prowadzić do niepożądanych turbulencji i zaburzeń w przepływie laminarnym.
Systemy wentylacji i klimatyzacji w naszym zakładzie muszą zapewnić wymagany poziom wilgotności względnej powietrza. Osiągamy to przez zastosowanie odpowiednio zaprojektowanych systemów nawilżania i osuszania powietrza. Z doświadczenia wiem, że utrzymanie odpowiedniej wilgotności jest szczególnie trudne w zimie, gdy powietrze zewnętrzne jest bardzo suche. Dlatego w naszym zakładzie stosujemy zaawansowane systemy nawilżania, które pozwalają nam utrzymać wilgotność względną na poziomie nie niższym niż 30% nawet w najzimniejsze dni.
Z kolei latem, gdy wilgotność zewnętrzna jest wysoka, musimy dbać o to, aby w pomieszczeniach czystych nie przekraczała ona 65%. Zbyt wysoka wilgotność może prowadzić do rozwoju mikroorganizmów i kondensacji pary wodnej na powierzchniach, co jest absolutnie niedopuszczalne w środowisku Cleanroom.
Dla pomieszczeń czystych gorszych klas, takich jak ISO 9, stosujemy nieco mniej rygorystyczne podejście. Przyjmujemy projektową temperaturę powietrza wewnętrznego wynoszącą 21°C dla zimy i 23°C dla lata. W tych pomieszczeniach nie ma konieczności stosowania systemów z regulacją wilgotności względnej powietrza, jednak staramy się utrzymywać ją w granicach 30-65%. To podejście pozwala nam na znaczne oszczędności energetyczne przy jednoczesnym zapewnieniu odpowiednich warunków dla mniej krytycznych procesów.
Warto podkreślić, że utrzymanie odpowiedniej temperatury i wilgotności względnej w pomieszczeniach czystych wymaga zaawansowanych systemów kontroli i regulacji. W naszym zakładzie stosujemy systemy automatyki, które pozwalają na precyzyjne sterowanie parametrami powietrza i szybką reakcję na wszelkie odchylenia.
Podsumowując, kontrola temperatury i wilgotności względnej powietrza w pomieszczeniach czystych to złożone zadanie, wymagające zaawansowanych systemów i ciągłego monitoringu. Tylko takie kompleksowe podejście pozwala na utrzymanie stabilnych warunków zgodnych z normą ISO 14644-1 i zapewnienie optymalnych warunków dla procesów produkcyjnych.
Prędkość nawiewu powietrza w pomieszczeniach czystych
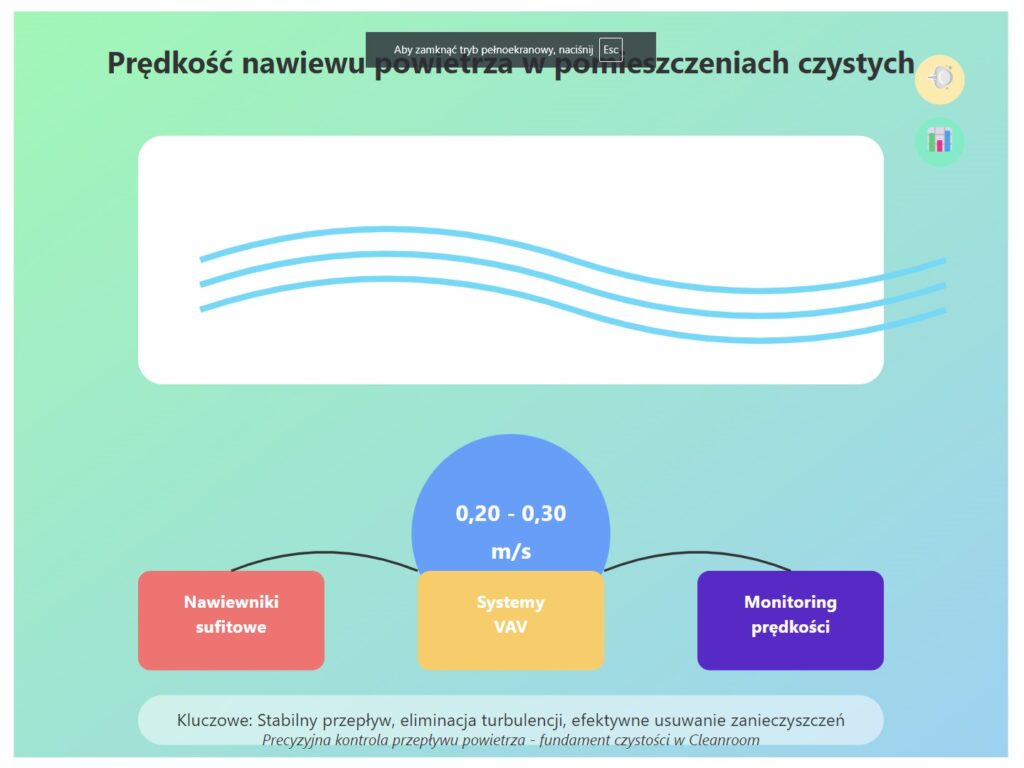
W mojej wieloletniej praktyce zarządzania pomieszczeniami czystymi, kontrola prędkości nawiewu powietrza zawsze stanowiła jeden z kluczowych elementów zapewnienia odpowiedniej czystości i funkcjonalności Cleanroom. Prawidłowa prędkość nawiewu jest niezbędna do skutecznego usuwania zanieczyszczeń i utrzymania laminarnego przepływu powietrza.
W naszym zakładzie, zgodnie z najlepszymi praktykami i normami, przeprowadzamy pomiary prędkości nawiewu powietrza przy temperaturze powietrza nawiewanego wynoszącej 20°C ±0,5. Ta precyzja jest kluczowa, ponieważ temperatura powietrza może wpływać na jego gęstość, a tym samym na prędkość przepływu.
Dla pomieszczeń z nawiewem laminarnym, które są szczególnie istotne w przypadku wyższych klas czystości, stosujemy bardzo dokładną metodykę pomiarową. Ilość punktów pomiarowych nie powinna być mniejsza niż 1 punkt na 1 m2 powierzchni nawiewu laminarnego. To podejście pozwala nam na uzyskanie dokładnego obrazu rozkładu prędkości powietrza w całym pomieszczeniu.
W przypadku pomieszczeń klasy ISO 8, które stanowią znaczną część naszego zakładu, szczególną uwagę zwracamy na to, aby prędkość powietrza nawiewanego nie przekraczała wartości 0,20 m/s w strefie przebywania ludzi. To ograniczenie jest istotne nie tylko ze względu na komfort pracowników, ale także na utrzymanie stabilnego przepływu powietrza i minimalizację turbulencji, które mogłyby prowadzić do redystrybucji zanieczyszczeń.
Dla pozostałych pomieszczeń, minimalny strumień powietrza nawiewanego przyjmujemy zgodnie z aktualnymi rozporządzeniami i normami oraz wymaganiami technologii. W praktyce oznacza to, że dla każdego pomieszczenia musimy indywidualnie określić wymagany strumień powietrza, uwzględniając jego przeznaczenie, wyposażenie i liczbę osób w nim przebywających.
Z mojego doświadczenia wynika, że utrzymanie odpowiedniej prędkości nawiewu powietrza może być szczególnie trudne w pomieszczeniach o wysokich klasach czystości, takich jak ISO 5 czy ISO 6. W tych przypadkach często stosujemy systemy z zmienną prędkością przepływu (VAV – Variable Air Volume), które pozwalają na dynamiczne dostosowanie prędkości nawiewu do aktualnych warunków w pomieszczeniu.
Warto podkreślić, że prędkość nawiewu powietrza ma bezpośredni wpływ na efektywność usuwania zanieczyszczeń z pomieszczenia. Zbyt niska prędkość może prowadzić do gromadzenia się cząstek, podczas gdy zbyt wysoka może powodować turbulencje i redystrybucję zanieczyszczeń. Dlatego w naszym zakładzie prowadzimy ciągły monitoring prędkości nawiewu i regularnie przeprowadzamy testy wizualizacji przepływu powietrza, aby upewnić się, że zachowujemy odpowiedni laminarny przepływ.
Jednym z wyzwań, z którymi często się spotykamy, jest konieczność dostosowania prędkości nawiewu do specyficznych wymagań procesów produkcyjnych. Na przykład, w naszym laboratorium mikrobiologicznym musieliśmy znacznie zmniejszyć prędkość nawiewu nad stanowiskami pracy, aby uniknąć zakłóceń w hodowli mikroorganizmów. W takich przypadkach zawsze ściśle współpracujemy z działem produkcji i działem jakości, aby znaleźć optymalne rozwiązanie, które zapewni zarówno wymaganą czystość powietrza, jak i odpowiednie warunki dla procesów produkcyjnych.
Podsumowując, kontrola prędkości nawiewu powietrza w pomieszczeniach czystych to złożone zadanie, wymagające precyzyjnych pomiarów, zaawansowanych systemów kontroli i ciągłego monitoringu. Tylko takie kompleksowe podejście pozwala na utrzymanie stabilnych warunków zgodnych z normą ISO 14644-1 i zapewnienie optymalnych warunków dla procesów produkcyjnych w Cleanroom.
Kaskada ciśnień w Cleanroom
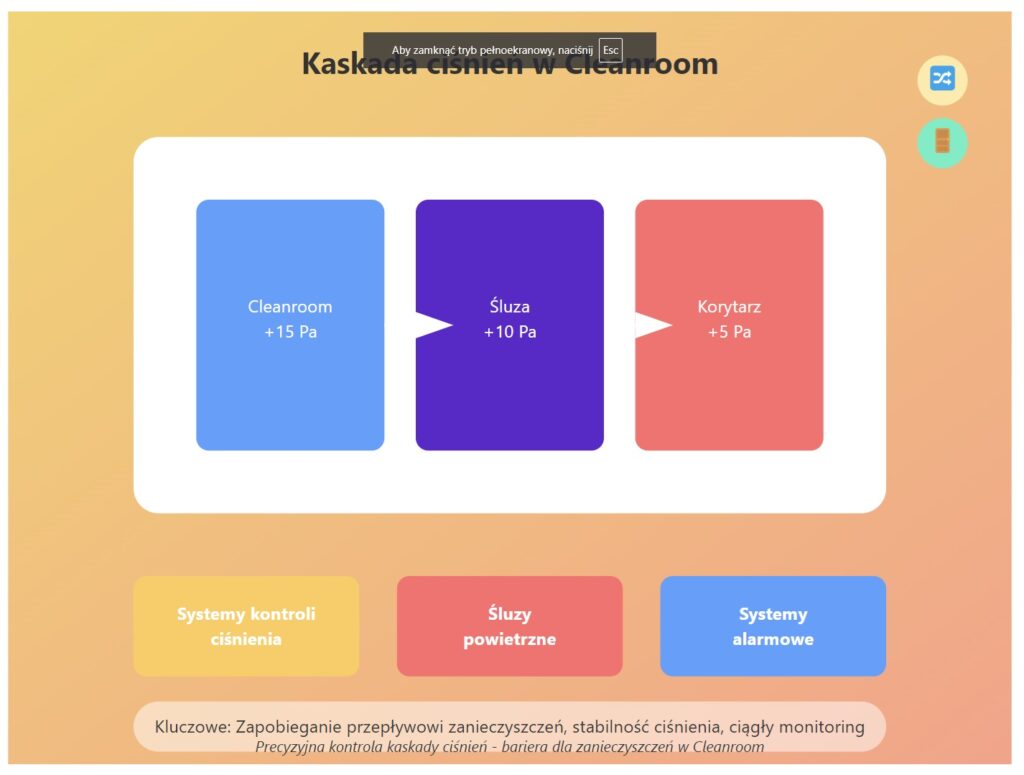
W trakcie mojej 20-letniej kariery w zarządzaniu pomieszczeniami czystymi, zrozumienie i utrzymanie właściwej kaskady ciśnienia powietrza okazało się jednym z najbardziej krytycznych aspektów funkcjonowania Cleanroom. Prawidłowa kaskada ciśnienia jest kluczowa dla zapobiegania przedostawaniu się zanieczyszczeń między pomieszczeniami o różnych klasach czystości.
W naszym zakładzie, aby utrzymać właściwą kaskadę ciśnienia powietrza dla pomieszczeń czystych, stosujemy się do następujących rygorystycznych wymagań:
- Różnica ciśnienia powietrza pomiędzy Cleanroom a wszystkimi pomieszczeniami przylegającymi powinna wynosić nie mniej niż 10 Pa. To minimalna wartość, która w praktyce okazała się skuteczna w zapobieganiu przepływowi zanieczyszczeń z obszarów mniej czystych do bardziej czystych.
- Różnica ciśnienia powietrza pomiędzy pomieszczeniami pomocniczymi a korytarzem powinna wynosić nie mniej niż 5 Pa. To pozwala na utrzymanie hierarchii czystości nawet w obszarach, które nie są bezpośrednio zaangażowane w procesy produkcyjne.
- Różnica ciśnienia powietrza pomiędzy korytarzem czystym a korytarzem brudnym powinna wynosić nie mniej niż 5 Pa. Ta zasada pomaga w utrzymaniu ogólnej czystości w całym kompleksie Cleanroom.
Z mojego doświadczenia wynika, że w przypadku wszystkich pomieszczeń czystych warto dążyć do utrzymania nadciśnienia/podciśnienia powietrza o wartości nie mniejszej niż 10 Pa względem śluzy. To zapewnia dodatkową barierę ochronną i minimalizuje ryzyko przypadkowego zanieczyszczenia.
W przypadku pomieszczeń o szczególnie wysokich wymaganiach czystości lub tych, gdzie prowadzone są krytyczne procesy, stosujemy jeszcze bardziej rygorystyczne podejście. W takich sytuacjach zapewniamy kaskadę ciśnienia wynoszącą minimum 15 Pa nadciśnienia pomiędzy pomieszczeniem a śluzą oraz minimum 5 Pa pomiędzy śluzą a korytarzem. To podejście sprawdziło się w naszym laboratorium mikrobiologicznym, gdzie nawet najmniejsze zanieczyszczenie mogłoby mieć katastrofalne skutki dla prowadzonych badań.
Warto podkreślić, że we wszystkich pomieszczeniach zalecamy utrzymywanie większej różnicy ciśnienia powietrza niż minimalne wartości. Jednakże, zawsze musimy pamiętać o zachowaniu równowagi między skutecznością kaskady ciśnienia a komfortem użytkowników. Zbyt duże różnice ciśnień mogą prowadzić do problemów z otwieraniem drzwi czy dyskomfortu dla personelu. Dlatego w naszej praktyce staramy się nie przekraczać maksymalnego dopuszczalnego poziomu dźwięku A w analizowanych pomieszczeniach.
Jednym z największych wyzwań, z jakimi się spotkałem, było utrzymanie właściwej kaskady ciśnienia w kompleksie pomieszczeń o różnych funkcjach i klasach czystości. Absolutnie niedopuszczalne jest łączenie pomieszczeń o odrębnej funkcji i różnym układzie ciśnienia w obrębie jednego pomieszczenia. To wymaga bardzo starannego planowania układu pomieszczeń i systemu wentylacji już na etapie projektowania.
Kluczowe jest to, że wymagane nadciśnienie/podciśnienie powietrza musi być bezwzględnie utrzymane podczas każdego etapu pracy instalacji. Nie może być ono zależne od zanieczyszczenia filtrów, trybu pracy (pełna lub ograniczona wydajność) czy innych zakłóceń pracy układu wentylacji i klimatyzacji. To wymaga zaawansowanego systemu sterowania i automatyki, który uwzględnia wszystkie te czynniki i dynamicznie dostosowuje pracę systemu.
W naszym zakładzie wprowadziśmy system ciągłego monitoringu różnic ciśnień między pomieszczeniami, z alarmami w przypadku odchyleń od założonych wartości. To pozwala nam na szybką reakcję w przypadku jakichkolwiek nieprawidłowości. Dodatkowo, regularnie przeprowadzamy testy dymowe, które pozwalają na wizualną weryfikację kierunku przepływu powietrza między pomieszczeniami.
Podsumowując, utrzymanie właściwej kaskady ciśnienia powietrza w Cleanroom to złożone zadanie, wymagające precyzyjnego projektowania, zaawansowanych systemów kontroli i ciągłego monitoringu. Jest to jednak absolutnie kluczowe dla zapewnienia odpowiedniej czystości powietrza i skutecznego funkcjonowania pomieszczeń czystych zgodnie z normą ISO 14644-1.
Ciśnienie akustyczne w pomieszczeniach czystych
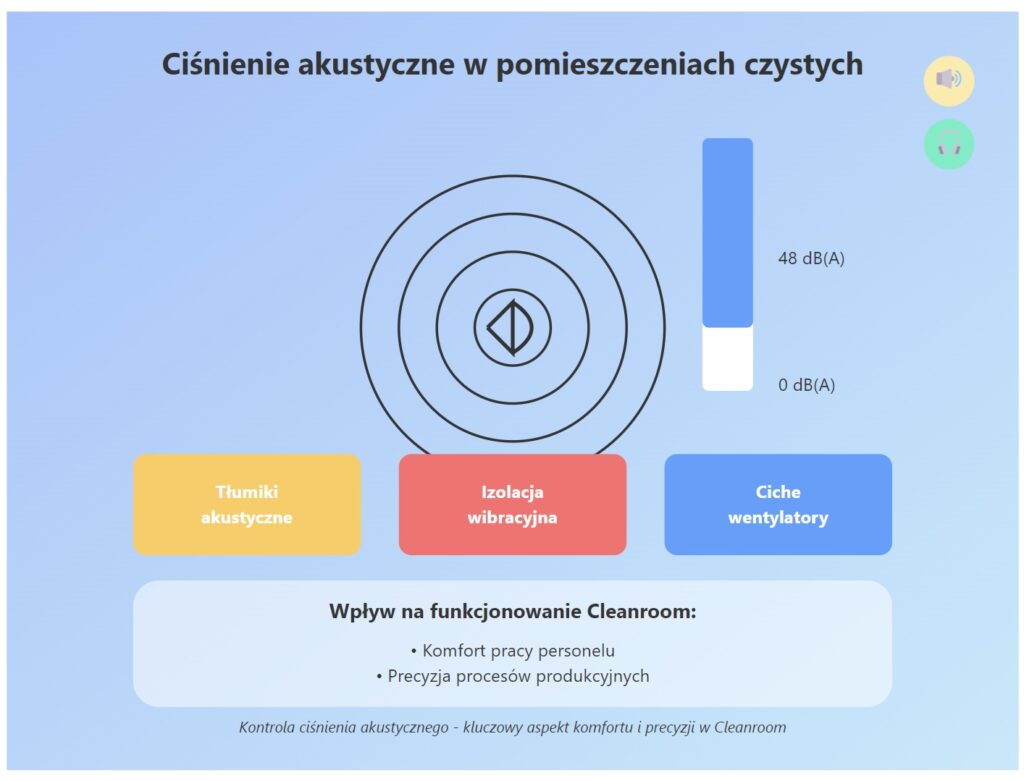
W mojej wieloletniej praktyce zarządzania pomieszczeniami czystymi, kwestia ciśnienia akustycznego, czyli poziomu hałasu, okazała się niezwykle istotna, choć często niedoceniana. Odpowiedni poziom ciśnienia akustycznego jest kluczowy nie tylko dla komfortu personelu, ale także dla precyzji niektórych procesów produkcyjnych i badawczych.
Dla pomieszczeń czystych w naszym zakładzie przyjęliśmy rygorystyczne normy dotyczące dopuszczalnego poziomu ciśnienia akustycznego. Zgodnie z naszymi wytycznymi, podczas pracy systemu wentylacji i klimatyzacji, poziom hałasu nie może przekraczać 48 dB(A). To wartość, która zapewnia komfortowe warunki pracy, jednocześnie nie wpływając negatywnie na procesy produkcyjne.
Pomiar poziomu ciśnienia akustycznego wykonujemy w centralnym punkcie pomieszczenia czystego na wysokości 1,75 m powyżej poziomu podłogi. Ta lokalizacja została wybrana jako reprezentatywna dla typowej pozycji uszu stojącego człowieka. Z mojego doświadczenia wynika, że pomiary w tym punkcie dają najbardziej miarodajne wyniki, odzwierciedlające rzeczywiste warunki pracy personelu.
Warto zaznaczyć, że normy ISO ustalają wejściowe parametry środowiska wewnętrznego do projektowania systemów w budynku i obliczania charakterystyki energetycznej. W praktyce oznacza to, że musimy brać pod uwagę nie tylko hałas generowany przez system wentylacji i klimatyzacji, ale także inne źródła dźwięku w pomieszczeniu czystym.
W naszym zakładzie, oprócz ogólnej normy 48 dB(A), stosujemy bardziej szczegółowe wytyczne dla różnych typów pomieszczeń. Na przykład, dla pomieszczeń biurowych i laboratoryjnych staramy się utrzymać poziom hałasu poniżej 40 dB(A). To zapewnia lepsze warunki do pracy umysłowej i precyzyjnych badań.
Jednym z największych wyzwań, z jakimi się spotkałem, było pogodzenie wymagań dotyczących ciśnienia akustycznego z potrzebą utrzymania odpowiedniej kaskady ciśnień między pomieszczeniami. Większa różnica ciśnień często wiąże się z większym hałasem generowanym przez system wentylacji. W takich przypadkach konieczne było zastosowanie zaawansowanych rozwiązań tłumiących hałas, takich jak specjalne tłumiki akustyczne czy nawiewniki o niskim poziomie generowanego hałasu.
Warto również zwrócić uwagę na fakt, że w pomieszczeniach czystych, które wyposażone są w dużą ilość zróżnicowanego sprzętu, hałas od wentylacji jest istotną, ale nie jedyną składową poziomu dźwięku A. W normie PN-EN 15251 typowy zakres poziomu dźwięku A określono jako 30 dB(A) do 48 dB(A). Jednak z mojego doświadczenia wynika, że w nowoczesnych i w pełni wyposażonych pomieszczeniach czystych poziom dźwięku A często oscyluje wokół górnej granicy tego zakresu.
W praktyce, utrzymanie odpowiedniego poziomu ciśnienia akustycznego wymaga kompleksowego podejścia. W naszym zakładzie wprowadziliśmy szereg rozwiązań, takich jak:
- Stosowanie cichobieżnych wentylatorów i pomp.
- Izolacja akustyczna przewodów wentylacyjnych.
- Używanie tłumików akustycznych w systemach wentylacji.
- Odpowiednie rozmieszczenie urządzeń generujących hałas.
- Regularne przeglądy i konserwacja systemów, aby zapobiec powstawaniu dodatkowego hałasu związanego z zużyciem elementów.
Ponadto, wprowadziśmy system ciągłego monitoringu poziomu hałasu w kluczowych pomieszczeniach. To pozwala nam na szybką reakcję w przypadku przekroczenia dopuszczalnych wartości.
Warto również wspomnieć o aspekcie psychologicznym. Z naszych obserwacji wynika, że personel pracujący w pomieszczeniach czystych jest szczególnie wrażliwy na hałas. Dlatego, oprócz spełnienia norm technicznych, prowadzimy również szkolenia dla pracowników na temat wpływu hałasu na zdrowie i efektywność pracy.
Podsumowując, kontrola ciśnienia akustycznego w pomieszczeniach czystych to złożone zadanie, wymagające kompleksowego podejścia i ciągłego monitoringu. Jest to jednak kluczowy element zapewnienia komfortowych i bezpiecznych warunków pracy, a także utrzymania wysokiej jakości procesów produkcyjnych zgodnie z normą ISO 14644-1.
Elementy systemu rozdziału powietrza w pomieszczeniach czystych
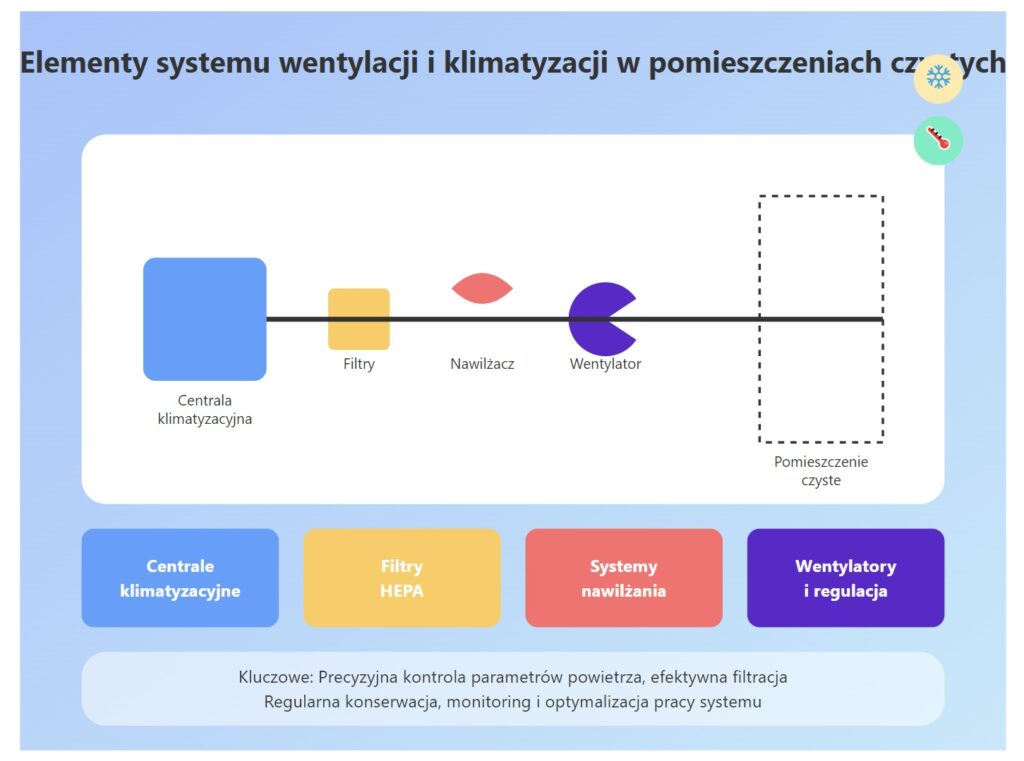
W trakcie mojej 20-letniej kariery w zarządzaniu pomieszczeniami czystymi, zrozumiałem, że elementy systemu rozdziału powietrza są kluczowe dla utrzymania wymaganej czystości i parametrów mikroklimatu. Ich odpowiedni dobór i utrzymanie ma bezpośredni wpływ na efektywność całego systemu wentylacji i klimatyzacji w Cleanroom.
Nawiewniki
Nawiewniki są jednym z najbardziej krytycznych elementów systemu rozdziału powietrza w pomieszczeniach czystych. W naszym zakładzie stosujemy nawiewniki, które muszą spełniać bardzo rygorystyczne wymagania. Przede wszystkim, muszą być one przystosowane do użytkowania w pomieszczeniach o podwyższonych wymaganiach higienicznych.
Z mojego doświadczenia wynika, że kluczową cechą nawiewników w Cleanroom jest łatwość dostępu w celu regularnego czyszczenia. W praktyce oznacza to, że konstrukcja nawiewnika musi umożliwiać szybki i łatwy demontaż wszystkich jego elementów.
Materiały, z których wykonane są nawiewniki, również mają ogromne znaczenie. W naszym zakładzie stosujemy nawiewniki wykonane z materiałów gładkich, odpornych na ścieranie i korozję. Najczęściej wybieramy stal nierdzewną 1.4301, która sprawdziła się jako materiał łatwy w skutecznym czyszczeniu ręcznym i dezynfekcji.
Stropy laminarne
Strop laminarny jest głównym elementem wyposażenia systemu wentylacji i klimatyzacji obsługującego pomieszczenie czyste, szczególnie w przypadku pomieszczeń o najwyższych klasach czystości. W naszej praktyce, przy projektowaniu i eksploatacji stropów laminarnych, kierujemy się kilkoma kluczowymi zasadami:
- Powietrze zewnętrzne wprowadzane jest do pomieszczenia tylko przez strop laminarny. To zapewnia pełną kontrolę nad jakością powietrza wprowadzanego do pomieszczenia.
- Prędkość opadania strugi konieczna do utrzymania stabilnego przepływu laminarnego powinna wynosić w przedziale 0,18-0,25 m/s (pomiar na wysokości 1,20 m nad poziomem podłogi). Utrzymanie tej prędkości jest kluczowe dla efektywnego usuwania zanieczyszczeń.
- Filtrem końcowym, zainstalowanym bezpośrednio w płaszczyźnie nawiewnej stropu, musi być filtr wysokoskuteczny o klasie minimum H13 (zgodnie z PN-EN 1822-1). W szczególnych przypadkach, gdy technologia wymaga umożliwienia wymiany filtrów po stronie brudnej, dopuszczamy umiejscowienie filtra wysokoskutecznego na wlocie powietrza do komory rozprężnej nawiewnika laminarnego.
- W stropie laminarnym montujemy urządzenie stabilizujące strugę nawiewanego powietrza (laminaryzator), wykonane z tkaniny spełniającej wymagania higieniczne dla tego rodzaju produktu.
- Wszystkie elementy wyposażenia i zabudowy stropu laminarnego muszą być szczelne i skonstruowane tak, aby nie było przecieków powietrza w ich obrębie. To obejmuje przecieki na filtrze, na połączeniu ramy filtra z elementem konstrukcyjnym mocującym filtr w stropie laminarnym, pomiędzy ramą filtra a materiałem filtracyjnym, oraz pomiędzy elementem konstrukcyjnym a przewodem wentylacyjnym.
- Zapewniamy łatwy dostęp do króćców pomiarowych, co umożliwia regularne kontrole i pomiary.
Z mojego doświadczenia wynika, że utrzymanie szczelności stropu laminarnego jest jednym z największych wyzwań w eksploatacji pomieszczeń czystych. Dlatego w naszym zakładzie wprowadziłem system regularnych kontroli szczelności, wykorzystujący zaawansowane metody pomiarowe, takie jak testy z użyciem generatorów aerozolu.
Nawiewniki skośne
W pomieszczeniach czystych o mniejszych wymaganiach higienicznych stosujemy nawiewniki skośne. Jednak nawet w tych przypadkach zachowujemy wysokie standardy. Bezpośrednio w nawiewniku musi być zainstalowany filtr wysokoskuteczny o klasie minimum H13.
Umiejscowienie nawiewników skośnych jest kluczowe dla ich efektywności. W naszej praktyce umieszczamy je w narożu ściany i sufitu, tworząc nawiewnik liniowy (tylko z jednej strony sali). Powietrze nawiewane jest w kierunku obszaru chronionego. Prędkość nawiewu określa producent, ale nie powinna być wyższa niż 2 m/s oraz powinna zapewnić prędkość strugi powietrza w rejonie obszaru chronionego na poziomie 0,15 m/s – 0,25 m/s.
Nawiewniki z wypływem turbulentnym
W szczególnych przypadkach, w zależności od przeznaczenia pomieszczeń czystych, stosujemy nawiewniki z wypływem turbulentnym. W tych przypadkach wymagamy zamontowania bezpośrednio w nawiewniku filtrów wysokoskutecznych o klasie minimum H11, z zachowaniem szczelności osadzenia.
Prędkość nawiewu nawiewnika określa jego producent, ale nie powinna być wyższa niż 2 m/s oraz musi zapewnić zalecane parametry prędkości powietrza w strefie przebywania ludzi. To równoważenie między efektywnością filtracji a komfortem personelu jest jednym z największych wyzwań w projektowaniu systemu rozdziału powietrza.
Podsumowując, elementy systemu rozdziału powietrza w pomieszczeniach czystych wymagają starannego doboru, instalacji i konserwacji. Tylko kompleksowe podejście, uwzględniające wszystkie aspekty ich funkcjonowania, pozwala na utrzymanie wymaganej czystości powietrza zgodnie z normą ISO 14644-1 i zapewnienie optymalnych warunków dla procesów produkcyjnych w Cleanroom.
Wywiewniki w pomieszczeniach czystych
W trakcie mojej długoletniej praktyki w zarządzaniu pomieszczeniami czystymi, zrozumiałem, że wywiewniki są równie istotne jak elementy nawiewne. Ich odpowiedni dobór i rozmieszczenie ma kluczowe znaczenie dla utrzymania wymaganej czystości powietrza i prawidłowego funkcjonowania całego systemu wentylacji.
Wywiewniki w pomieszczeniach czystych muszą spełniać bardzo rygorystyczne wymagania. Przede wszystkim, podobnie jak nawiewniki, muszą być przystosowane do użytkowania w pomieszczeniach o podwyższonych wymaganiach higienicznych. W naszym zakładzie kładziemy duży nacisk na to, aby wywiewniki były łatwo dostępne w celu regularnego czyszczenia.
Materiały, z których wykonane są wywiewniki, mają ogromne znaczenie dla utrzymania czystości. Stosujemy wywiewniki wykonane z materiałów gładkich, odpornych na ścieranie i korozję. Najczęściej wybieramy stal nierdzewną, która sprawdziła się jako materiał łatwy w skutecznym czyszczeniu i dezynfekcji. To pozwala nam na utrzymanie wysokiego poziomu higieny i zapobiega gromadzeniu się zanieczyszczeń na powierzchni wywiewników.
Rozkład wywiewników w Cleanroom jest kluczowy dla zapewnienia bezpiecznego, stabilnego i ukierunkowanego przepływu powietrza przez pomieszczenie czyste. W naszej praktyce staramy się tak rozmieścić wywiewniki, aby uniemożliwić przekroczenie wartości granicznych stężeń szkodliwych zanieczyszczeń w każdym punkcie pomieszczenia. Jednocześnie musimy minimalizować zakłócenia wywołane zmieszaniem się strugi czystego powietrza z powietrzem wywiewanym.
Kratki wywiewne w pomieszczeniach klasy ISO 8 i ISO 5
W pomieszczeniach klasy ISO 8 i ISO 5, które stanowią znaczną część naszego zakładu, stosujemy specjalne rozwiązania dla kratek wywiewnych. Wywiew powietrza odbywa się za pośrednictwem ściennych kratek wentylacyjnych w wykonaniu higienicznym. Umieszczamy je przy podłodze i pod sufitem, w odległości nie większej niż 0,30 m od powierzchni podłogi i sufitu, rozmieszczonych równomiernie w Cleanroom.
Szczególną uwagę zwracamy na wyposażenie kratek wywiewnych w separatory kłaczków o oczkach mniejszych niż 0,8 mm. To rozwiązanie okazało się niezwykle skuteczne w zapobieganiu przedostawaniu się większych cząstek z powrotem do systemu wentylacji.
Z mojego doświadczenia wynika, że kluczowe jest zapewnienie możliwości łatwego demontażu kratki wywiewnej w celu wymiany separatora kłaczków i czyszczenia. W naszym zakładzie wprowadziłem procedurę regularnej kontroli i czyszczenia kratek wywiewnych, co znacząco przyczyniło się do utrzymania wysokiej czystości powietrza.
Elementy wywiewne w pozostałych pomieszczeniach
W pomieszczeniach klasy ISO 9 podejście do elementów wywiewnych jest nieco mniej rygorystyczne, ale nadal wymaga uwagi. Elementy wywiewne rozmieszczamy zgodnie z zasadami sztuki inżynierskiej oraz obowiązującymi przepisami, zawsze uwzględniając ich dostępność dla personelu technicznego.
W przypadku pomieszczeń o podwyższonych wymaganiach higienicznych, nawet jeśli nie są to pomieszczenia najwyższej klasy czystości, stosujemy wywiewniki w wykonaniu higienicznym. Są one przystosowane do regularnego czyszczenia i dezynfekcji, co pozwala na utrzymanie wysokiego poziomu czystości w całym kompleksie Cleanroom.
Jednym z największych wyzwań, z jakimi się spotkałem, było zapewnienie odpowiedniego balansu między ilością powietrza nawiewanego a wywiewanego. W praktyce oznacza to, że system wywiewny musi być precyzyjnie dostosowany do systemu nawiewnego, aby utrzymać wymagane nadciśnienie w pomieszczeniu czystym. Wymaga to starannego projektowania i regularnej kalibracji systemu.
Warto również wspomnieć o kwestii hałasu generowanego przez elementy wywiewne. W naszym zakładzie zwracamy szczególną uwagę na to, aby wywiewniki nie powodowały nadmiernego hałasu, który mógłby zakłócać pracę personelu lub wpływać na precyzję procesów produkcyjnych.
Podsumowując, elementy wywiewne w pomieszczeniach czystych, choć często niedoceniane, są kluczowe dla utrzymania wymaganej czystości powietrza. Ich odpowiedni dobór, rozmieszczenie i konserwacja są niezbędne do zapewnienia prawidłowego funkcjonowania całego systemu wentylacji i klimatyzacji w Cleanroom, zgodnie z wymaganiami normy ISO 14644-1.
Elementy systemu wentylacji i klimatyzacji w pomieszczeniach czystych
W mojej wieloletniej praktyce zarządzania pomieszczeniami czystymi, zrozumiałem, że prawidłowe funkcjonowanie elementów systemu wentylacji i klimatyzacji jest fundamentem utrzymania wymaganej czystości powietrza. Każdy element tego systemu ma kluczowe znaczenie i wymaga szczególnej uwagi.
Dostępność i umiejscowienie elementów
Jedną z najważniejszych zasad, którą zawsze się kieruję, jest zapewnienie łatwego dostępu do wszystkich elementów składowych systemu wentylacji i klimatyzacji. W naszym zakładzie wszystkie te elementy są usytuowane tak, aby ograniczyć do minimum konieczność wchodzenia do pomieszczeń najwyższych klas czystości na potrzeby eksploatacji, regulacji i czyszczenia.
W przypadku, gdy dostęp do takich elementów możliwy jest tylko poprzez pomieszczenia klasy ISO 8, wprowadziliśmy rygorystyczną procedurę czyszczenia i dezynfekcji tych pomieszczeń po każdych działaniach serwisowych. To podejście pozwala nam na utrzymanie wysokiego poziomu czystości nawet podczas prac konserwacyjnych.
Centrale klimatyzacyjne i wentylacyjne
Centrale klimatyzacyjne i wentylacyjne to serce systemu wentylacji w pomieszczeniach czystych. W naszym zakładzie przestrzegamy kilku kluczowych zasad dotyczących tych urządzeń:
- Urządzenia do uzdatnienia powietrza zewnętrznego (centrala lub szafa klimatyzacyjna) muszą znajdować się poza pomieszczeniami czystymi. To pozwala na łatwy dostęp dla personelu technicznego bez ryzyka zanieczyszczenia pomieszczeń czystych.
- Wszystkie komponenty central muszą spełniać wymagania norm PN-EN 13093 oraz PN-EN 1886. To zapewnia nam wysoką jakość i niezawodność tych urządzeń.
- Każda centrala posiada swoją indywidualną kartę katalogową. To ułatwia nam zarządzanie i konserwację tych urządzeń.
- Wszystkie powierzchnie wewnętrzne central są gładkie, pozbawione ostrych krawędzi oraz wykonane tak, aby zapobiegać rozwojowi mikroorganizmów. Z mojego doświadczenia wynika, że to kluczowy element w utrzymaniu czystości powietrza.
- Centrale są wyposażone w okna inspekcyjne oraz oświetlenie wewnętrzne, co ułatwia regularne kontrole i konserwację.
- Szczelność obudowy centrali odpowiada wymaganiom co najmniej klasy L2(R) zgodnie z normą PN-EN 1886. To zapewnia minimalne straty powietrza i energii.
Filtry powietrza
Filtry powietrza są kluczowym elementem w utrzymaniu czystości powietrza w pomieszczeniach czystych. W naszym zakładzie stosujemy filtry spełniające wymagania norm PN-EN 779 oraz PN-EN 1822-1.
Szczególną uwagę zwracamy na to, aby w pobliżu filtrów powietrza temperatura była zawsze wyższa od temperatury punktu rosy, również w okresie postoju systemu. To zapobiega kondensacji pary wodnej i potencjalnemu rozwojowi mikroorganizmów.
Konstrukcja ram i kaset filtrów jest tak zaprojektowana, aby zapewnić brak możliwości rozwoju mikroorganizmów i umożliwić łatwy i bezpieczny montaż. Szczelność zamontowania filtra jest dla nas priorytetem.
W naszej praktyce okazało się, że kluczowe jest regularne monitorowanie stanu filtrów. Każda sekcja filtracyjna w centrali wentylacyjno-klimatyzacyjnej jest wyposażona w presostat lub przetwornik ciśnienia do kontroli zabrudzenia filtra. To pozwala nam na wymianę filtrów w optymalnym momencie, co zapewnia ciągłą wysoką skuteczność filtracji przy jednoczesnej optymalizacji kosztów eksploatacji.
Urządzenia do odzysku ciepła
W naszym zakładzie stosujemy różne urządzenia do pośredniego odzysku ciepła z powietrza wywiewanego, takie jak wymienniki z czynnikiem pośrednim, rurki cieplne, pompy ciepła czy wymienniki krzyżowe i przeciwprądowe. Kluczowe jest, aby te urządzenia były łatwe do czyszczenia i dezynfekcji.
Z mojego doświadczenia wynika, że umiejscowienie wymiennika do odzysku ciepła za pierwszym stopniem filtracji w centrali klimatyzacyjnej jest optymalnym rozwiązaniem. Ponadto, w jednostce powietrza wywiewanego przed wymiennikiem zawsze montujemy filtr powietrza klasy co najmniej M6.
Chłodnice i nagrzewnice
W fazie projektowania pomieszczeń czystych zawsze starannie szacujemy potencjalne zyski wilgoci, które będą wydzielane w Cleanroom. To pozwala nam na dobór odpowiedniej chłodnicy (pracującej na „sucho” lub na „mokro”). Z praktyki wiem, że warto przewidzieć rezerwę mocy chłodniczej na poziomie co najmniej 10-15%.
W przypadku nagrzewnic, dopuszczamy stosowanie wodnych lub elektrycznych nagrzewnic powietrza. Kluczowe jest zastosowanie odpowiednich zabezpieczeń, szczególnie w przypadku nagrzewnic elektrycznych, gdzie bezwzględnie przestrzegamy minimalnej prędkości przepływu przez nagrzewnicę.
Podsumowując, prawidłowe funkcjonowanie wszystkich elementów systemu wentylacji i klimatyzacji jest kluczowe dla utrzymania wymaganej czystości powietrza w pomieszczeniach czystych zgodnie z normą ISO 14644-1. Wymaga to starannego doboru, instalacji i regularnej konserwacji wszystkich komponentów systemu.
Wentylatory do pomieszczeń czystych
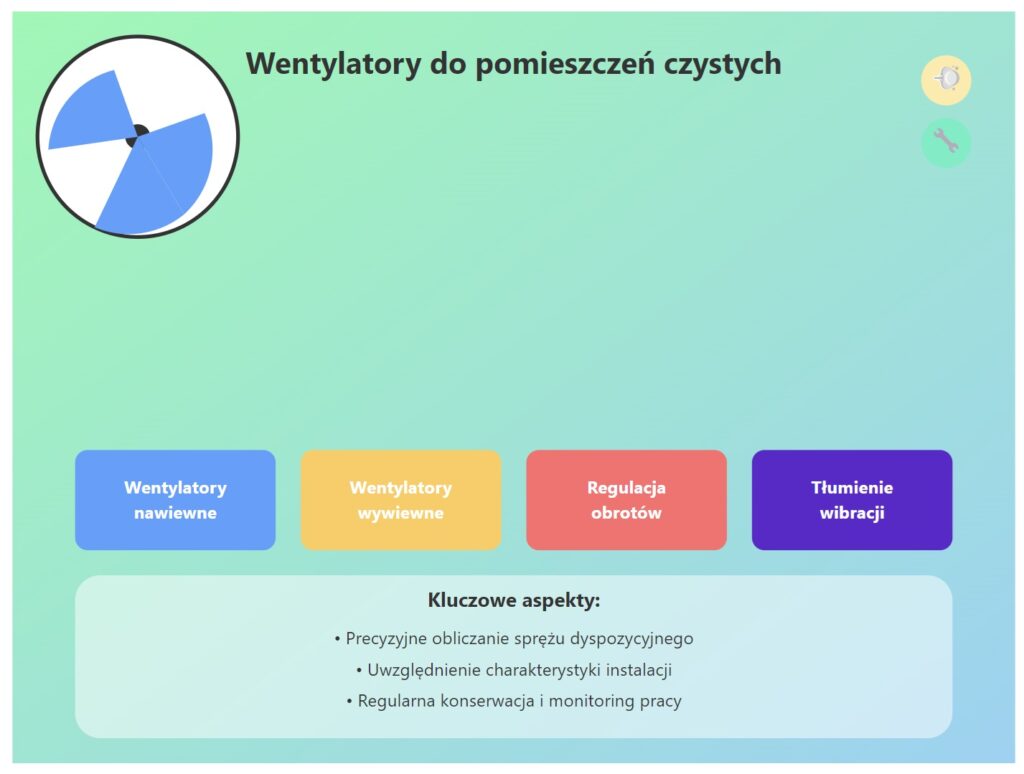
W mojej 20-letniej praktyce zarządzania pomieszczeniami czystymi, dobór i utrzymanie odpowiednich wentylatorów zawsze stanowiło jedno z kluczowych wyzwań. Wentylatory są sercem systemu wentylacji i klimatyzacji, a ich prawidłowe działanie jest niezbędne do utrzymania wymaganej czystości powietrza.
W naszym zakładzie stosujemy się do kilku kluczowych zasad dotyczących wentylatorów:
- Wentylatory nawiewne umieszczamy między pierwszym a drugim stopniem filtracji. To pozwala na ochronę wentylatora przed zanieczyszczeniami z powietrza zewnętrznego, a jednocześnie zapewnia, że powietrze po wentylatorze przechodzi jeszcze przez drugi stopień filtracji.
- Wentylator wywiewny instalujemy za sekcją filtracji w części wywiewnej centrali. Dzięki temu chronimy wentylator przed zanieczyszczeniami z pomieszczeń czystych.
- W pomieszczeniach czystych ISO 8 i wyższych, gdzie musimy zapewnić nadciśnienie i utrzymać stały strumień powietrza wentylacyjnego, stosujemy specjalne podejście do obliczania sprężu dyspozycyjnego. Przyjmujemy maksymalny dopuszczalny przez producenta filtrów spadek ciśnienia na filtrach pierwszego i drugiego stopnia, a dla filtra trzeciego stopnia przyjmujemy opór początkowy powiększony o co najmniej 200%.
To podejście pozwala nam na zachowanie stałej prędkości opadania strugi laminarnej w całym okresie pracy filtra – od stanu oporu początkowego, poprzez fazę przyrostu oporu wynikającego z procesu zabrudzenia filtra, aż do stanu zabrudzenia zagrażającego utracie nadciśnienia.
W praktyce, przy doborze wentylatora, zawsze uwzględniamy kilka kluczowych aspektów:
- Przyjętą klasę szczelności kanałów. To ma bezpośredni wpływ na rzeczywisty przepływ powietrza i wymagany spręż wentylatora.
- Nadwyżkę wydajności wentylatora na ewentualne błędy montażowe podczas fazy wykonawczej. Z doświadczenia wiem, że ta rezerwa często okazuje się nieoceniona.
- Charakterystykę instalacji. Zawsze nanosimy ją na charakterystykę dobranego wentylatora i oznaczamy punkty pracy wentylatora nawiewnego w czterech fazach:
- Fazie początkowej: przy początkowych oporach przepływu na filtrach
- Fazie nominalnej: przy oporach na filtrach równych połowie wartości między początkowym a dopuszczalnym końcowym spadkiem ciśnienia
- Fazie końcowej: przy założonych maksymalnych oporach na filtrach
- Trybie ograniczonego wydatku (tzw. trybie nocnym)
To podejście, choć czasochłonne, pozwala nam na precyzyjne dobranie wentylatora i uniknięcie problemów z wydajnością systemu w późniejszej eksploatacji.
Jednym z największych wyzwań, z jakimi się spotkałem, było zapewnienie stabilnej pracy wentylatorów przy zmieniających się oporach filtrów. Rozwiązaniem okazało się zastosowanie wentylatorów z płynną regulacją obrotów, sterowanych przez zaawansowany system automatyki. System ten na bieżąco monitoruje opory filtrów i dostosowuje wydajność wentylatorów, zapewniając stały przepływ powietrza.
Warto również wspomnieć o kwestii hałasu generowanego przez wentylatory. W pomieszczeniach czystych, gdzie często prowadzone są precyzyjne procesy produkcyjne, nadmierny hałas może być problematyczny. Dlatego w naszym zakładzie stosujemy wentylatory o niskim poziomie generowanego hałasu, a dodatkowo instalujemy je na specjalnych podstawach antywibracyjnych.
Podsumowując, prawidłowy dobór i eksploatacja wentylatorów w pomieszczeniach czystych to złożone zadanie, wymagające kompleksowego podejścia i głębokiej wiedzy technicznej. Tylko takie podejście pozwala na utrzymanie wymaganej czystości powietrza zgodnie z normą ISO 14644-1 i zapewnienie optymalnych warunków dla procesów produkcyjnych w Cleanroom.
Nawilżacze powietrza w pomieszczeniach czystych
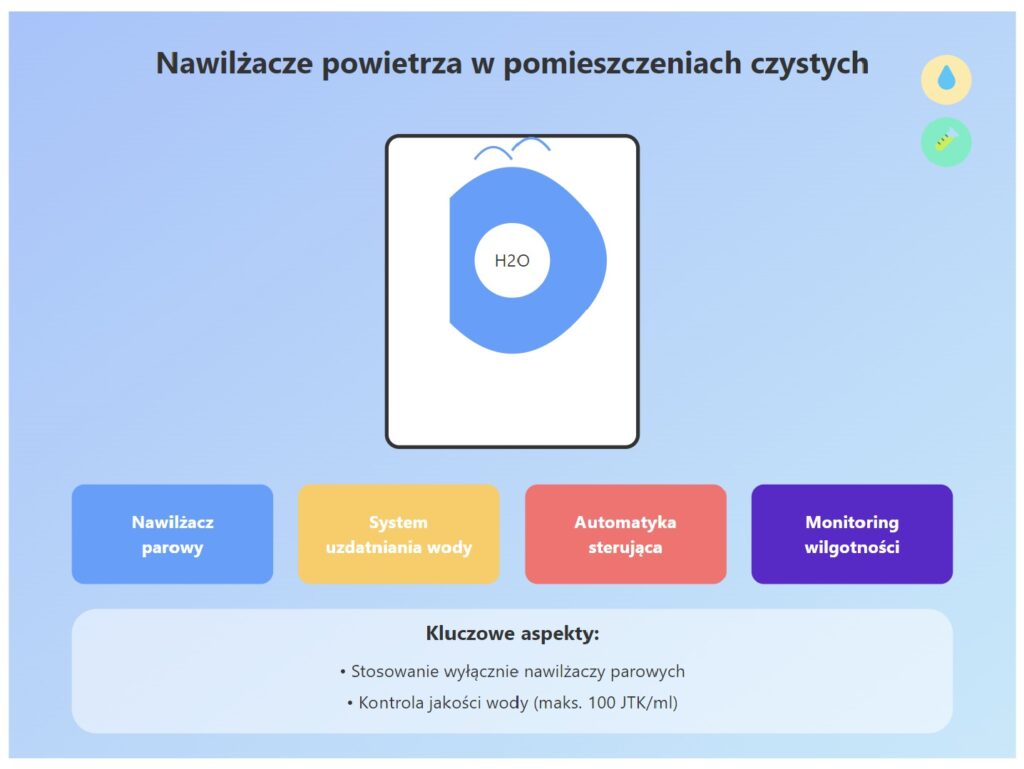
W mojej 20-letniej praktyce zarządzania pomieszczeniami czystymi, kwestia nawilżania powietrza zawsze stanowiła istotny element w utrzymaniu odpowiednich warunków mikroklimatu. Ze względów higienicznych, w pomieszczeniach czystych dopuszczamy stosowanie jedynie nawilżaczy parowych. To rozwiązanie sprawdziło się najlepiej w zapewnieniu czystości i kontroli wilgotności powietrza.
Kluczową kwestią jest jakość pary wodnej używanej do nawilżania. W naszym zakładzie zwracamy szczególną uwagę na to, aby para wodna nie zawierała żadnych szkodliwych substancji. To wymaga regularnych kontroli jakości wody używanej do produkcji pary oraz konserwacji systemu nawilżania.
W praktyce, instalacja nawilżaczy wymaga starannego planowania i precyzyjnego wykonania. W naszym zakładzie stosujemy się do następujących zasad:
- Nawilżacze powietrza instalujemy wewnątrz centrali lub szafy klimatyzacyjnej przed drugim stopniem filtracji. To zapewnia, że nawilżone powietrze przechodzi jeszcze przez filtr, co eliminuje ryzyko wprowadzenia ewentualnych zanieczyszczeń do pomieszczenia czystego.
- W niektórych przypadkach dopuszczamy zastosowanie kanałowego nawilżacza powietrza z lancą (lub lancami) zainstalowaną w przewodzie wentylacyjnym za drugim stopniem filtracji. Jednak w takich sytuacjach konieczne jest precyzyjne określenie drogi nawilżania oraz zapewnienie systemu odprowadzenia skroplin. Z doświadczenia wiem, że to rozwiązanie wymaga szczególnej uwagi podczas projektowania i instalacji.
- Zawsze dbamy o to, aby wilgotność względna powietrza na końcu drogi nawilżania nie przekraczała 90%. To kluczowe dla uniknięcia kondensacji pary wodnej w systemie wentylacji.
- Bezwzględnie nie dopuszczamy do zawilgocenia filtra spowodowanego pracą nawilżacza. To mogłoby prowadzić do rozwoju mikroorganizmów i pogorszenia jakości powietrza.
Automatyka nawilżacza to kolejny kluczowy element, któremu poświęcamy dużo uwagi. W naszym zakładzie system automatyki nawilżacza jest zaprojektowany tak, aby gwarantować:
- Zatrzymanie pracy nawilżacza w wypadku awarii systemu nawiewnego.
- Wyłączenie nawilżacza przy zbyt małym przepływie powietrza.
- Zatrzymanie pracy przy przekroczeniu maksymalnej zawartości wilgoci w powietrzu nawiewanym.
Ponadto, zawsze stosujemy zwłokę czasową załączenia nawilżacza do pracy w stosunku do wentylatorów nawiewnych po uruchomieniu centrali. To zapobiega nagłemu wzrostowi wilgotności w systemie wentylacji.
Jednym z największych wyzwań, z jakimi się spotkałem, była kontrola jakości wody używanej do nawilżania. Zgodnie z normą PN-EN 13053, zanieczyszczenia biologiczne w wodzie nie powinny przekroczyć 100 JTK/ml. Aby spełnić ten wymóg, wprowadziliśmy system regularnego monitoringu jakości wody oraz zaawansowany system jej uzdatniania.
Instalacja doprowadzająca wodę do nawilżacza w naszym zakładzie jest wyposażona w filtr siatkowy oraz zawór odcinający. Ponadto, woda musi spełniać wymagania producenta urządzenia pod względem twardości i przewodności. To wymaga regularnych kontroli i konserwacji systemu uzdatniania wody.
W przypadku montażu nawilżacza na zewnątrz budynku, co czasami jest konieczne ze względów przestrzennych, zawsze pamiętamy o zabezpieczeniu systemu zasilania w wodę oraz systemu odprowadzania kondensatu przed zamarznięciem. To kluczowe dla zapewnienia ciągłości pracy systemu nawilżania w okresie zimowym.
Podsumowując, prawidłowe nawilżanie powietrza w pomieszczeniach czystych to złożone zadanie, wymagające starannego planowania, precyzyjnego wykonania i ciągłego monitoringu. Tylko takie kompleksowe podejście pozwala na utrzymanie odpowiedniej wilgotności powietrza przy jednoczesnym zachowaniu wysokiej czystości, zgodnie z wymaganiami normy ISO 14644-1.
Przewody wentylacyjne do pomieszczeń czystych
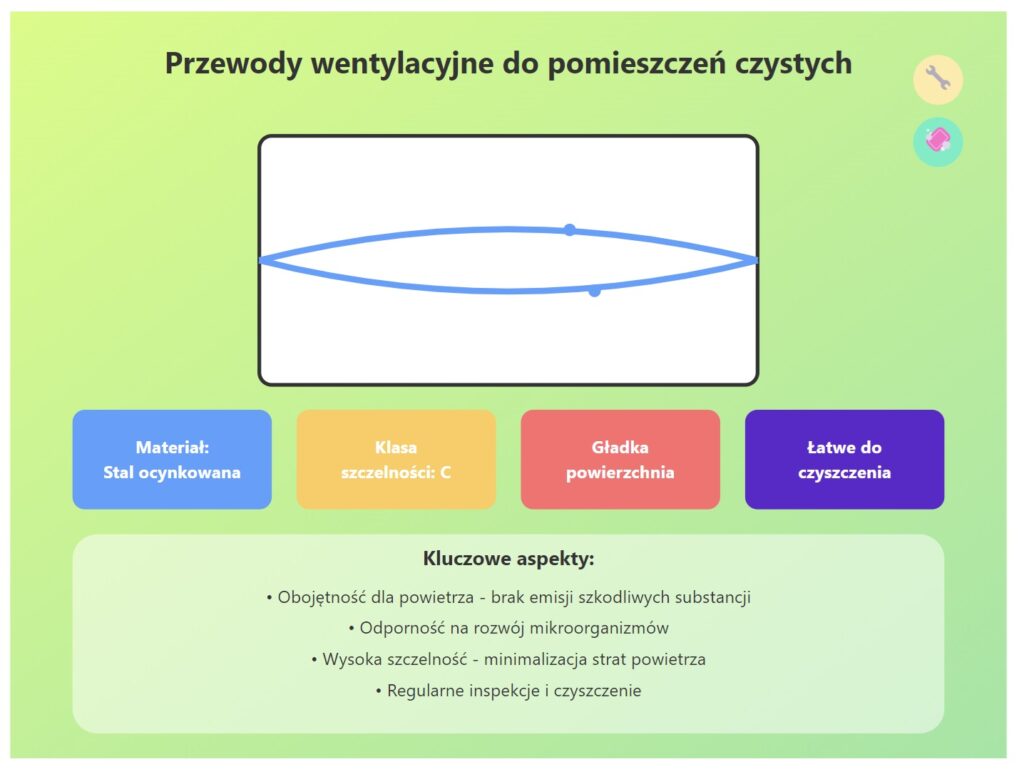
W mojej wieloletniej praktyce zarządzania pomieszczeniami czystymi, kwestia doboru i instalacji odpowiednich przewodów wentylacyjnych zawsze stanowiła jeden z kluczowych elementów systemu. Prawidłowo zaprojektowane i wykonane przewody wentylacyjne są niezbędne do utrzymania wymaganej czystości powietrza i efektywności całego systemu.
Materiały i powierzchnie
Z doświadczenia wiem, że dobór odpowiednich materiałów do wykonania przewodów wentylacyjnych jest kluczowy. W naszym zakładzie stosujemy się do następujących zasad:
- Wszystkie materiały używane do produkcji przewodów muszą być całkowicie obojętne dla powietrza. Nie mogą wydzielać szkodliwych substancji, włókien ani zapachów do nawiewanego powietrza oraz pomieszczeń.
- Materiały nie mogą stanowić pożywki dla mikroorganizmów ani sprzyjać ich rozwojowi. To kluczowe dla utrzymania czystości mikrobiologicznej powietrza.
- Powierzchnie przewodów muszą być gładkie i nie sprzyjać osadzaniu się zanieczyszczeń.
W praktyce, najczęściej stosujemy przewody wykonane z blachy ze stali ocynkowanej, zgodnie z normami PN-EN 1505 dla przewodów o przekroju prostokątnym oraz PN-EN 1506 dla przewodów o przekroju kołowym. Te materiały sprawdziły się najlepiej pod względem trwałości i łatwości utrzymania w czystości.
Warto zaznaczyć, że do podłączenia urządzeń nawiewnych w pomieszczeniach czystych ISO 6 i ISO 5 bezwzględnie nie dopuszczamy stosowania przewodów elastycznych, np. typu flex. Z mojego doświadczenia wynika, że takie przewody są trudne do utrzymania w czystości i mogą stanowić źródło zanieczyszczeń.
Szczelność przewodów
Szczelność przewodów wentylacyjnych to kolejny kluczowy aspekt, któremu poświęcamy dużo uwagi. W naszym zakładzie stosujemy się do następujących zasad:
- Dla instalacji, w której zamontowany jest filtr HEPA, projektujemy sieć przewodów z zachowaniem klasy szczelności C zgodnie z normami PN-EN 1507 oraz PN-EN 12237, przyjmując testowe nadciśnienie statyczne wynoszące 1000 Pa.
- W szczególnych, uzasadnionych przypadkach dopuszczamy obniżenie klasy szczelności do B, ale zawsze musi to być poparte dokładną analizą i uzasadnieniem.
- Dla instalacji bez zastosowanych filtrów HEPA projektujemy sieć przewodów z zachowaniem klasy szczelności B.
Klasa szczelności przewodów zawsze jest jednoznacznie określona w projekcie systemu wentylacji i klimatyzacji. W przypadku braku takiego określenia, dla instalacji z filtrami HEPA przyjmujemy domyślnie klasę szczelności C, a dla instalacji bez filtrów HEPA – klasę B.
Czystość instalacji
Utrzymanie czystości instalacji wentylacyjnej to jedno z największych wyzwań w zarządzaniu pomieszczeniami czystymi. W naszej praktyce stosujemy następujące podejście:
- Wszystkie elementy składowe instalacji są dostarczane w stanie czystym i zabezpieczone przed zanieczyszczeniem w trakcie montażu.
- Systemy wentylacji i klimatyzacji instalujemy w taki sposób, aby wszystkie elementy dystrybucji powietrza w momencie odbioru instalacji były czyste w najwyższym możliwym do uzyskania stopniu.
- Przed przystąpieniem do czyszczenia zawsze przeprowadzamy kontrolę, która poprzedza decyzję o konieczności oczyszczenia instalacji.
- W przypadku konieczności dezynfekcji, przeprowadzamy ją zawsze po mechanicznym oczyszczeniu instalacji z osadu. Dezynfekcja nigdy nie zastępuje mechanicznego czyszczenia.
- Do dezynfekcji stosujemy wyłącznie preparaty biobójcze posiadające atest PZH i przeznaczone do stosowania w systemach wentylacji i klimatyzacji.
Warto zaznaczyć, że po każdym czyszczeniu zalecamy wymianę filtrów HEPA. To zapewnia nam pewność, że cały system jest w pełni czysty i gotowy do pracy.
Podsumowując, prawidłowe zaprojektowanie, wykonanie i utrzymanie przewodów wentylacyjnych w pomieszczeniach czystych to złożone zadanie, wymagające dużej wiedzy i doświadczenia. Tylko kompleksowe podejście, uwzględniające wszystkie aspekty – od doboru materiałów, przez zapewnienie szczelności, aż po regularne czyszczenie i konserwację – pozwala na utrzymanie wymaganej czystości powietrza zgodnie z normą ISO 14644-1.
Otwory rewizyjne w przewodach wentylacyjnych
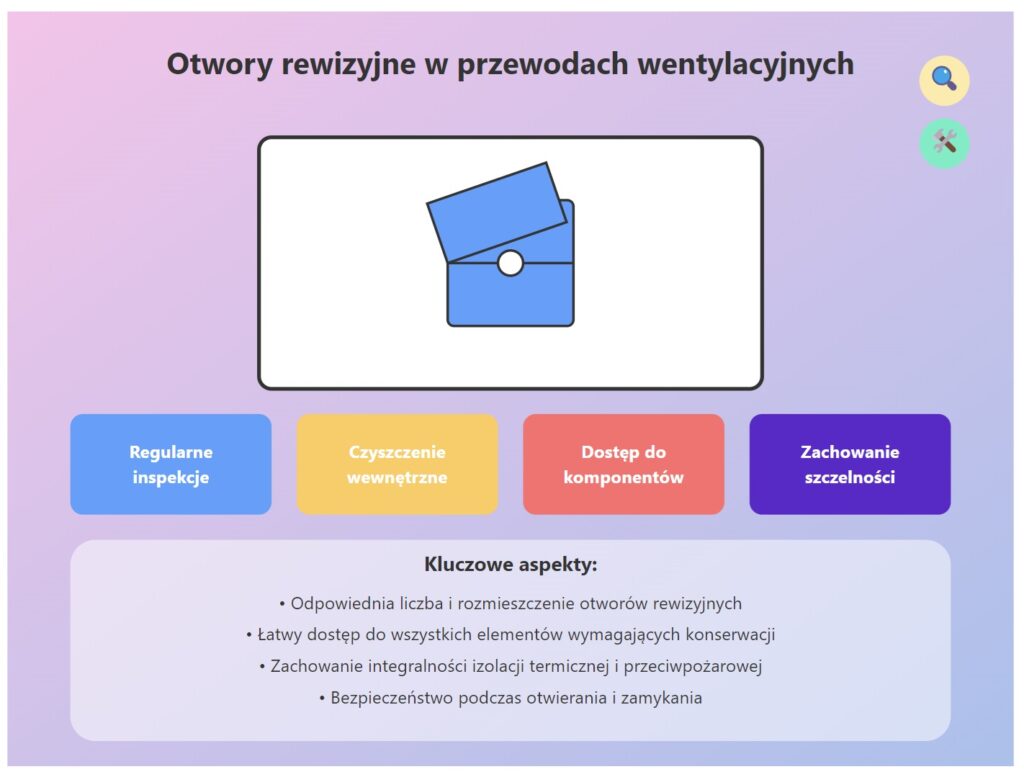
W trakcie mojej 20-letniej kariery w zarządzaniu pomieszczeniami czystymi, zrozumiałem, że prawidłowe rozmieszczenie i wykonanie otworów rewizyjnych w przewodach wentylacyjnych jest kluczowe dla efektywnej konserwacji i utrzymania czystości systemu.
Otwory rewizyjne mają fundamentalne znaczenie, ponieważ umożliwiają czyszczenie wewnętrznych powierzchni przewodów, a także dostęp do urządzeń i elementów instalacji, jeśli ich konstrukcja nie pozwala na czyszczenie w inny sposób. Z mojego doświadczenia wynika, że brak odpowiednich otworów rewizyjnych może znacząco utrudnić, a czasem wręcz uniemożliwić, prawidłową konserwację systemu wentylacyjnego.
W naszym zakładzie stosujemy się do zaleceń normy PN-EN 12097 dotyczących wykonania otworów rewizyjnych. Kluczowe jest zapewnienie wystarczającej ilości odpowiedniej wielkości otworów rewizyjnych, aby umożliwić dostęp do wszystkich obszarów podlegających czyszczeniu. W praktyce oznacza to, że czasem musimy uwzględnić demontaż pojedynczych elementów składowych instalacji, aby zapewnić pełny dostęp.
Rozmieszczenie otworów rewizyjnych wraz z ich wymiarami zawsze uwzględniamy w projekcie. To pozwala nam na optymalne zaplanowanie prac konserwacyjnych i czyszczenia. Ponadto, zawsze dbamy o to, aby konstrukcja przegród budowlanych oraz pozostałych elementów wyposażenia budynku zapewniała technologiczny i swobodny dostęp do otworu rewizyjnego przez służby serwisowe.
Z mojego doświadczenia wynika, że szczególnie trudne w czyszczeniu są niektóre elementy wyposażenia instalacji. Dlatego zawsze zapewniamy dostęp z obu stron (otwory serwisowe) dla następujących elementów:
- Przepustnice regulacyjne i odcinające
- Klapy przeciwpożarowe
- Nagrzewnice i chłodnice
- Nawilżacze
- Tłumiki hałasu z wewnętrznymi płytami
- Sekcje filtracji
- Wentylatory przewodowe
- Urządzenia do odzyskiwania ciepła
- Urządzenia do regulacji strumienia powietrza
- Kierownice powietrza
W przypadku, gdy nie ma możliwości zapewnienia dostępu z obu stron, zawsze projektujemy system w taki sposób, aby umożliwić demontaż tych elementów w celu konserwacji.
Szczególną uwagę zwracamy na przewody z dodatkową izolacją (izolacja cieplna lub przeciwpożarowa). W takich przypadkach wykonanie otworu rewizyjnego nie może wpłynąć negatywnie na działanie ochronne izolacji/osłony. To wymaga precyzyjnego projektowania i wykonania, ale jest kluczowe dla zachowania integralności systemu.
Jednym z największych wyzwań, z jakimi się spotkałem, było zapewnienie, aby otwory rewizyjne nie obniżały klasy szczelności przewodów wentylacyjnych. Rozwiązaniem okazało się stosowanie specjalnie zaprojektowanych, certyfikowanych otworów rewizyjnych, które gwarantują zachowanie wymaganej szczelności.
Warto również wspomnieć o kwestii bezpieczeństwa. W naszym zakładzie wprowadziliśmy procedurę, zgodnie z którą przed każdym otwarciem otworu rewizyjnego konieczne jest wyłączenie systemu wentylacji. To zapobiega potencjalnym wypadkom związanym z nagłym wypływem powietrza lub wciągnięciem narzędzi do systemu.
Podsumowując, prawidłowe zaprojektowanie i wykonanie otworów rewizyjnych w przewodach wentylacyjnych to kluczowy element w utrzymaniu czystości i efektywności systemu wentylacji w pomieszczeniach czystych. Wymaga to starannego planowania, precyzyjnego wykonania i regularnej kontroli. Tylko takie kompleksowe podejście pozwala na utrzymanie wymaganej czystości powietrza zgodnie z normą ISO 14644-1 i zapewnienie optymalnych warunków dla procesów produkcyjnych w Cleanroom.
Tłumiki w systemach wentylacyjnych pomieszczeń czystych
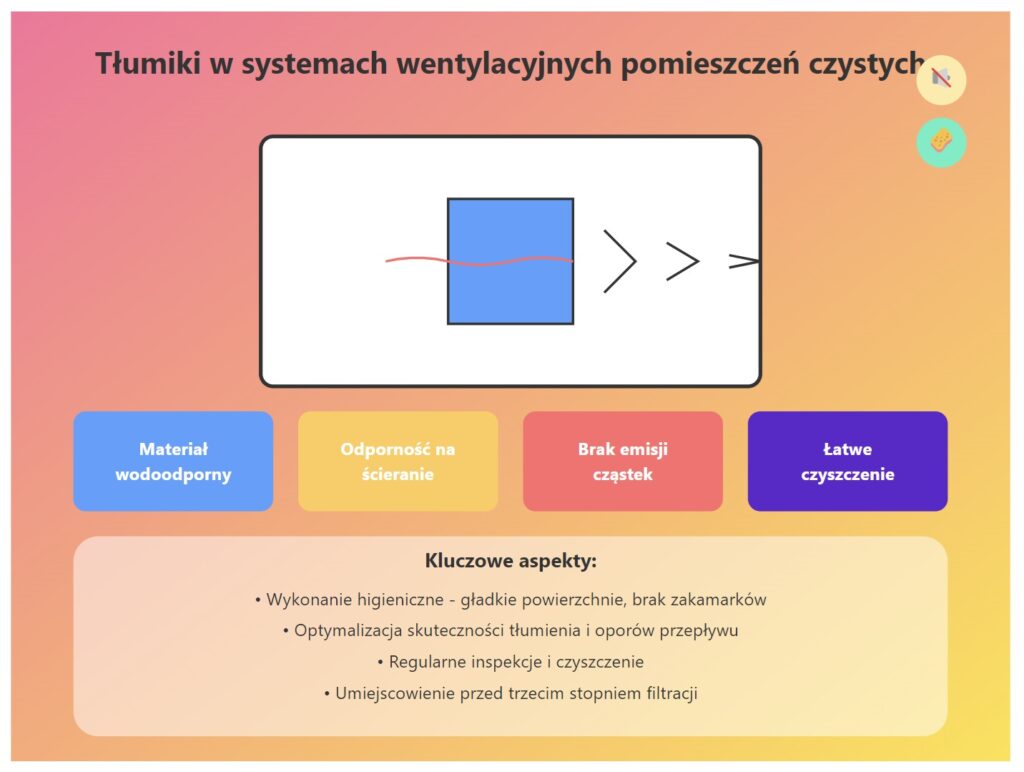
W mojej wieloletniej praktyce zarządzania pomieszczeniami czystymi, kwestia kontroli hałasu generowanego przez systemy wentylacyjne zawsze stanowiła istotne wyzwanie. Tłumiki odgrywają kluczową rolę w redukcji hałasu, jednocześnie muszą spełniać rygorystyczne wymagania dotyczące czystości i higieny.
Wymagania dla tłumików
W naszym zakładzie stosujemy tłumiki, które muszą spełniać następujące kryteria:
- Powierzchnia tłumika, która ma kontakt z powietrzem, musi być gładka. To kluczowe dla zapobiegania gromadzeniu się zanieczyszczeń i ułatwia czyszczenie.
- Materiał, z którego wykonany jest tłumik, musi być odporny na ścieranie. W praktyce oznacza to, że nawet przy regularnym czyszczeniu i przepływie powietrza, tłumik nie może uwalniać cząstek do strumienia powietrza.
- Tłumik musi być wodoodporny. To ważne nie tylko ze względu na możliwość kondensacji pary wodnej, ale także w kontekście regularnego czyszczenia i dezynfekcji.
- Materiał tłumika nie może ulegać rozkładowi. Stabilność materiału w czasie jest kluczowa dla utrzymania stałej efektywności tłumienia i zapobiegania uwalnianiu cząstek.
- Tłumik musi być niepylący. To absolutnie kluczowe w kontekście utrzymania czystości powietrza w pomieszczeniach czystych.
Umiejscowienie tłumików
Z mojego doświadczenia wynika, że umiejscowienie tłumików w systemie wentylacyjnym jest równie ważne jak ich konstrukcja. W naszej praktyce nigdy nie stosujemy tłumików za trzecim stopniem filtracji. To podejście zapewnia, że powietrze po przejściu przez najwyższy stopień filtracji nie ma kontaktu z potencjalnym źródłem zanieczyszczeń, jakim mógłby być tłumik.
Wykonanie higieniczne
We wszystkich naszych instalacjach stosujemy wyłącznie tłumiki w wykonaniu higienicznym. Oznacza to, że są one specjalnie zaprojektowane do użytku w środowiskach o podwyższonych wymaganiach czystości. Takie tłumiki charakteryzują się gładkimi powierzchniami, brakiem zakamarków trudnych do czyszczenia i wykorzystaniem materiałów odpornych na rozwój mikroorganizmów.
Wyzwania i rozwiązania
Jednym z największych wyzwań, z jakimi się spotkałem w kontekście tłumików, było znalezienie równowagi między skutecznością tłumienia hałasu a łatwością utrzymania w czystości. Tradycyjne materiały dźwiękochłonne, takie jak wełna mineralna, są trudne do czyszczenia i mogą stanowić źródło zanieczyszczeń.
Rozwiązaniem okazało się zastosowanie innowacyjnych materiałów, takich jak pianki poliuretanowe o otwartych komórkach, pokryte specjalną powłoką. Takie tłumiki łączą w sobie wysoką skuteczność tłumienia z łatwością czyszczenia i odpornością na rozwój mikroorganizmów.
Innym wyzwaniem było zapewnienie odpowiedniej skuteczności tłumienia przy jednoczesnym minimalizowaniu oporów przepływu powietrza. W tym przypadku kluczowe okazało się precyzyjne modelowanie akustyczne i przepływowe na etapie projektowania. Wykorzystujemy zaawansowane narzędzia do symulacji, które pozwalają nam optymalizować geometrię tłumików dla konkretnych warunków.
Konserwacja i czyszczenie
Regularna konserwacja i czyszczenie tłumików są kluczowe dla utrzymania ich skuteczności i zapobiegania zanieczyszczeniom. W naszym zakładzie wprowadziłem procedurę regularnych inspekcji wizualnych tłumików, co najmniej raz na kwartał. Dodatkowo, co roku przeprowadzamy gruntowne czyszczenie i dezynfekcję wszystkich tłumików.
Do czyszczenia używamy specjalistycznych środków, które skutecznie usuwają zanieczyszczenia, nie uszkadzając przy tym powierzchni tłumika. Proces czyszczenia zawsze kończymy dokładnym płukaniem czystą wodą i suszeniem strumieniem czystego powietrza.
Podsumowując, prawidłowy dobór, instalacja i konserwacja tłumików w systemach wentylacyjnych pomieszczeń czystych to złożone zadanie, wymagające specjalistycznej wiedzy i doświadczenia. Tylko kompleksowe podejście, uwzględniające wszystkie aspekty – od materiałów i konstrukcji, przez umiejscowienie, aż po regularną konserwację – pozwala na skuteczne tłumienie hałasu przy jednoczesnym utrzymaniu wymaganej czystości powietrza zgodnie z normą ISO 14644-1.
Przepustnice w systemach wentylacyjnych pomieszczeń czystych
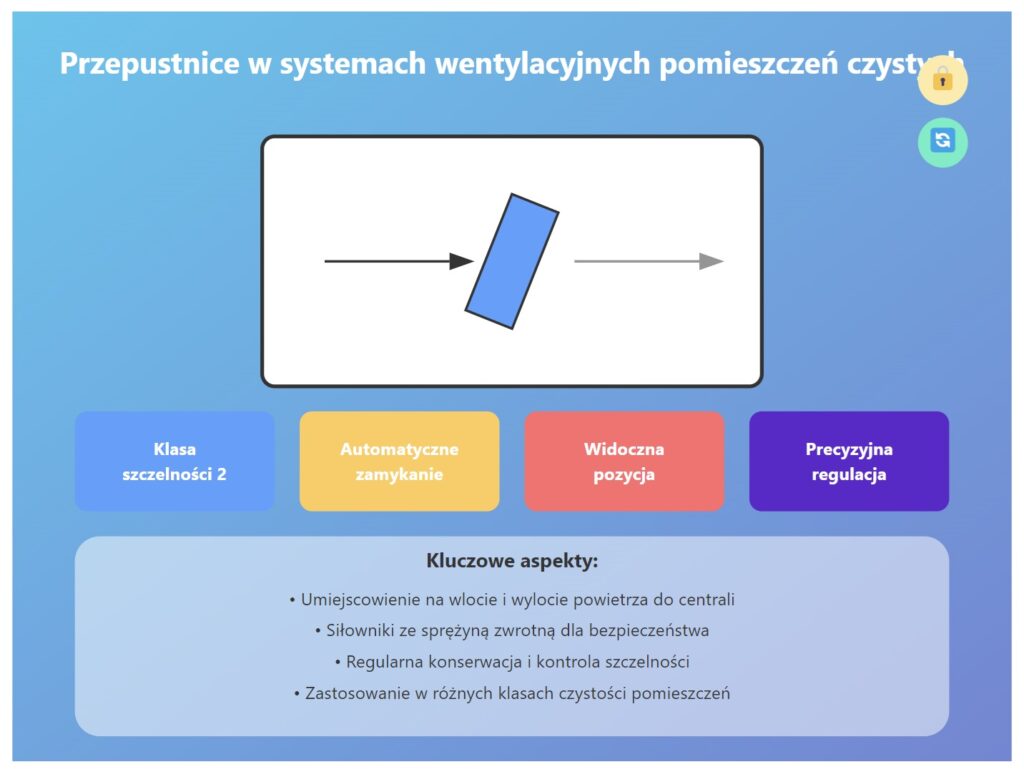
W trakcie mojej 20-letniej kariery w zarządzaniu pomieszczeniami czystymi, zrozumiałem, że przepustnice odgrywają kluczową rolę w kontroli przepływu powietrza i utrzymaniu odpowiednich parametrów w systemach wentylacyjnych. Ich prawidłowy dobór, instalacja i konserwacja są niezbędne dla zapewnienia efektywności całego systemu.
Umiejscowienie przepustnic
W naszym zakładzie stosujemy się do następujących zasad dotyczących umiejscowienia przepustnic:
- Przepustnice odcinające powietrza zewnętrznego umieszczamy na wlocie i wylocie powietrza do centrali/szafy klimatyzacyjnej. To kluczowe dla kontroli przepływu powietrza i zapobiegania przedostawaniu się zanieczyszczeń z zewnątrz w przypadku awarii lub postoju systemu.
- Wszystkie przepustnice odcinające wyposażamy w siłowniki ze sprężyną zwrotną lub inny system automatycznego zamykania. To zapewnia samoczynne zamknięcie w przypadku awarii, zaniku zasilania lub postoju urządzenia.
- W przewodach nawiewnych i wywiewnych montujemy przepustnice w następujących przypadkach:
- Na rozgałęzieniach przewodów zasilających pomieszczenia o różnych klasach czystości.
- Na odejściach do pomieszczeń, nawet tej samej klasy czystości, jeśli istnieje ryzyko cofnięcia się powietrza podczas postoju systemu.
Wymagania techniczne
Wszystkie przepustnice w naszych systemach muszą spełniać klasę szczelności 2 zgodnie z PN-EN 1751. To zapewnia minimalne straty powietrza i energii, co jest kluczowe dla efektywności systemu.
Zwracamy także uwagę na to, aby aktualna pozycja przepustnic (otwarte/zamknięte) była zawsze widoczna dla obsługi. To ułatwia szybką diagnostykę w przypadku problemów z przepływem powietrza.
Wyzwania i rozwiązania
Jednym z największych wyzwań, z jakimi się spotkałem, było zapewnienie odpowiedniej szczelności przepustnic w systemach o wysokich wymaganiach czystości. Tradycyjne przepustnice często nie spełniały naszych rygorystycznych wymagań.
Rozwiązaniem okazało się zastosowanie przepustnic z podwójnym uszczelnieniem i precyzyjnie wykonanymi łopatkami. Dodatkowo, w krytycznych punktach systemu stosujemy przepustnice z napędem elektrycznym i systemem monitorowania pozycji. To pozwala nam na ciągłą kontrolę i szybką reakcję w przypadku jakichkolwiek odchyleń.
Innym wyzwaniem było zapewnienie odpowiedniej regulacji przepływu powietrza w systemach o zmiennym obciążeniu. W tym przypadku kluczowe okazało się zastosowanie przepustnic regulacyjnych z precyzyjnymi siłownikami i zaawansowanym systemem sterowania. Dzięki temu możemy płynnie dostosowywać przepływ powietrza do aktualnych potrzeb, utrzymując jednocześnie wymagane parametry czystości.
Konserwacja i czyszczenie
Regularna konserwacja i czyszczenie przepustnic są kluczowe dla utrzymania ich sprawności i szczelności. W naszym zakładzie wprowadziłem procedurę kwartalnych przeglądów wszystkich przepustnic. Obejmują one:
- Kontrolę szczelności
- Sprawdzenie poprawności działania siłowników
- Czyszczenie i smarowanie elementów ruchomych
- Kontrolę stanu uszczelek i ich wymianę w razie potrzeby
Do czyszczenia przepustnic używamy specjalistycznych środków, które skutecznie usuwają zanieczyszczenia, nie uszkadzając przy tym powierzchni i uszczelek. Proces czyszczenia zawsze kończymy dokładnym płukaniem czystą wodą i suszeniem.
Dokumentacja i szkolenia
Z mojego doświadczenia wynika, że kluczowe jest prowadzenie dokładnej dokumentacji dotyczącej przepustnic. W naszym zakładzie dla każdej przepustnicy prowadzimy kartę, w której zapisujemy wszystkie czynności konserwacyjne, naprawy i wymiany.
Ponadto, regularnie szkolimy personel techniczny w zakresie obsługi i konserwacji przepustnic. To pozwala na szybkie wykrywanie potencjalnych problemów i efektywną konserwację.
Podsumowując, prawidłowy dobór, instalacja i konserwacja przepustnic w systemach wentylacyjnych pomieszczeń czystych to złożone zadanie, wymagające specjalistycznej wiedzy i doświadczenia. Tylko kompleksowe podejście, uwzględniające wszystkie aspekty – od wyboru odpowiedniego typu przepustnicy, przez jej umiejscowienie, aż po regularną konserwację – pozwala na efektywne kontrolowanie przepływu powietrza i utrzymanie wymaganej czystości zgodnie z normą ISO 14644-1.
Regulatory wydatku w systemach wentylacyjnych pomieszczeń czystych
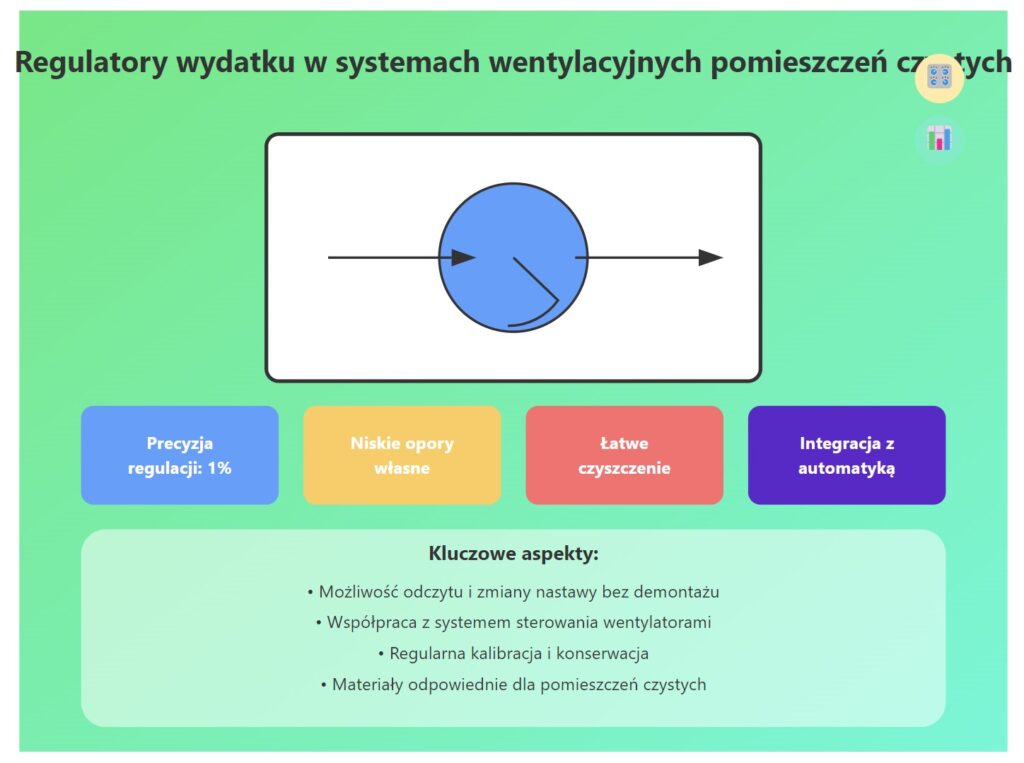
W mojej wieloletniej praktyce zarządzania pomieszczeniami czystymi, regulatory wydatku (strumienia powietrza wentylacyjnego) okazały się kluczowym elementem w utrzymaniu stabilnych warunków w Cleanroomach. Ich rola w precyzyjnej kontroli przepływu powietrza jest nie do przecenienia, szczególnie w kontekście utrzymania odpowiednich parametrów czystości zgodnie z normą ISO 14644-1.
Wybór i instalacja regulatorów wydatku
W naszym zakładzie stosujemy regulatory wydatku, które spełniają następujące kryteria:
- Umożliwiają odczyt oraz zmianę nastawionego wydatku bez konieczności ich demontażu. To kluczowe dla łatwej i szybkiej regulacji systemu bez naruszania integralności instalacji.
- Charakteryzują się wysoką precyzją regulacji. W praktyce oznacza to, że jesteśmy w stanie kontrolować przepływ powietrza z dokładnością do 1% nastawionej wartości.
- Posiadają niskie opory własne. To ważne dla efektywności energetycznej całego systemu wentylacyjnego.
- Są wykonane z materiałów odpowiednich dla pomieszczeń czystych, łatwych do czyszczenia i odpornych na środki dezynfekcyjne.
Współpraca z systemem sterowania
Jednym z największych wyzwań, z jakimi się spotkałem, była integracja regulatorów wydatku z ogólnym systemem sterowania wentylacją. Kluczowe jest, aby praca regulatorów wydatku nie zakłócała sterowania pracą wentylatora nawiewnego w danym systemie wentylacyjnym.
W naszej praktyce, w przypadku zastosowania na instalacji regulatorów wydatku oraz płynnej regulacji wydatku wentylatorów, zawsze szczegółowo opisujemy zasady współpracy regulatora wydatku i przetwornic częstotliwości zarządzających pracą wentylatorów. Te zasady są następnie uwzględniane w założeniach dla układu automatyki.
Typowy schemat współpracy wygląda następująco:
- System nadrzędny określa wymagane natężenie przepływu powietrza dla danego pomieszczenia na podstawie aktualnych parametrów (np. różnicy ciśnień, poziomu zanieczyszczeń).
- Sygnał jest przekazywany do regulatora wydatku, który dostosowuje swoje położenie.
- Jednocześnie, sygnał jest przekazywany do przetwornicy częstotliwości wentylatora, która dostosowuje jego obroty, aby utrzymać wymagane ciśnienie w systemie.
- System ciągle monitoruje rzeczywisty przepływ powietrza i dokonuje korekt w razie potrzeby.
Kalibracja i konserwacja
Regularna kalibracja i konserwacja regulatorów wydatku są kluczowe dla utrzymania ich dokładności i niezawodności. W naszym zakładzie stosujemy następującą procedurę:
- Kalibracja regulatorów wydatku co najmniej raz w roku, a w przypadku krytycznych pomieszczeń – co 6 miesięcy.
- Podczas kalibracji sprawdzamy zgodność rzeczywistego przepływu powietrza z wartością wskazywaną przez regulator. Do pomiarów używamy certyfikowanych anemometrów.
- Regularna inspekcja wizualna regulatorów pod kątem zanieczyszczeń lub uszkodzeń mechanicznych.
- Czyszczenie regulatorów specjalistycznymi środkami, które nie pozostawiają osadów i są bezpieczne dla materiałów, z których wykonane są regulatory.
Dokumentacja i szkolenia
Prowadzenie dokładnej dokumentacji dotyczącej regulatorów wydatku jest kluczowe dla efektywnego zarządzania systemem. W naszym zakładzie dla każdego regulatora prowadzimy kartę, w której zapisujemy:
- Datę instalacji
- Parametry nastawy
- Daty i wyniki kalibracji
- Wszelkie naprawy lub modyfikacje
Ponadto, regularnie szkolimy personel techniczny w zakresie obsługi i konserwacji regulatorów wydatku. Obejmuje to zarówno aspekty techniczne, jak i zrozumienie wpływu regulatorów na ogólne funkcjonowanie systemu wentylacji w pomieszczeniach czystych.
Wnioski i rekomendacje
Z mojego doświadczenia wynika, że inwestycja w wysokiej jakości regulatory wydatku oraz ich prawidłowa integracja z systemem sterowania są kluczowe dla utrzymania stabilnych warunków w pomieszczeniach czystych. Choć początkowo może to generować wyższe koszty, w dłuższej perspektywie przekłada się na lepszą kontrolę parametrów, niższe koszty energii i mniejsze ryzyko przekroczenia limitów czystości.
Rekomendowałbym również rozważenie zastosowania regulatorów wydatku z funkcją autodiagnostyki i możliwością zdalnego monitoringu. Takie rozwiązania, choć droższe, pozwalają na szybkie wykrycie potencjalnych problemów i minimalizację przestojów.
Podsumowując, prawidłowy dobór, instalacja i konserwacja regulatorów wydatku w systemach wentylacyjnych pomieszczeń czystych to złożone zadanie, wymagające specjalistycznej wiedzy i doświadczenia. Tylko kompleksowe podejście pozwala na efektywne kontrolowanie przepływu powietrza i utrzymanie wymaganej czystości zgodnie z normą ISO 14644-1.
Czerpnie i wyrzutnie powietrza w systemach wentylacyjnych pomieszczeń czystych
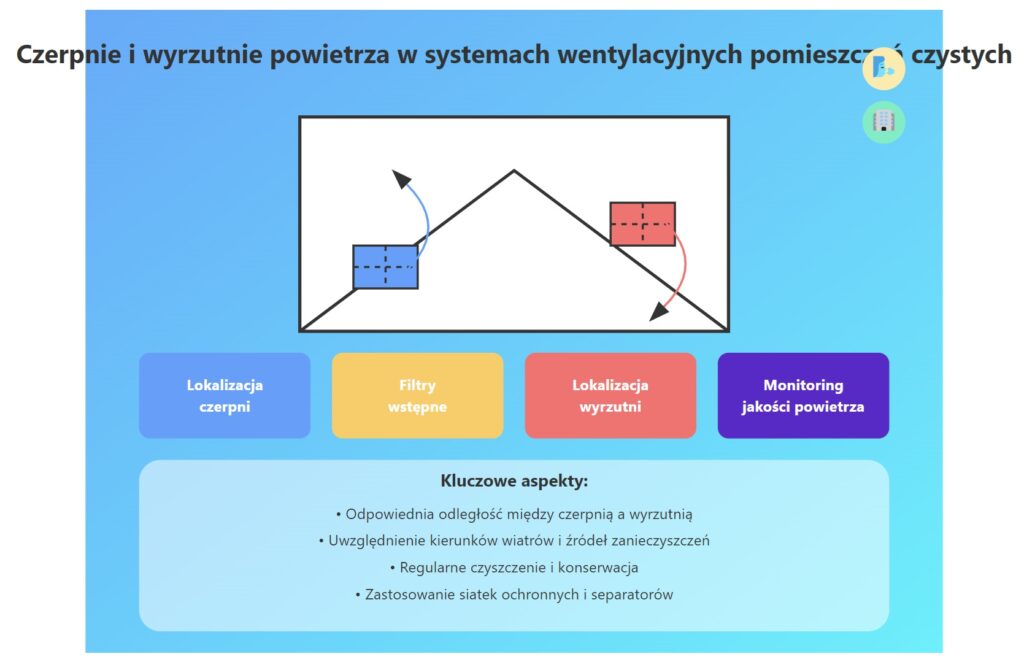
W trakcie mojej 20-letniej kariery w zarządzaniu pomieszczeniami czystymi, zrozumiałem, że prawidłowe zaprojektowanie i umiejscowienie czerpni i wyrzutni powietrza jest kluczowe dla utrzymania wysokiej jakości powietrza w Cleanroomach. Te elementy systemu wentylacyjnego stanowią pierwsze i ostatnie ogniwo w łańcuchu kontroli czystości powietrza, dlatego wymagają szczególnej uwagi.
Lokalizacja czerpni i wyrzutni
W naszym zakładzie, przy projektowaniu lokalizacji czerpni i wyrzutni, zawsze kierujemy się wymaganiami zawartymi w Dz.U.2002.75.690. Jednak z mojego doświadczenia wynika, że same przepisy to za mało – konieczne jest uwzględnienie wielu dodatkowych czynników:
- Warunki meteorologiczne: Analizujemy dane dotyczące kierunków wiatrów i ich siły w różnych porach roku. W naszym przypadku okazało się, że dominujący kierunek wiatru w zimie mógł powodować nawiewanie zanieczyszczonego powietrza z pobliskiej drogi bezpośrednio na czerpnię. Rozwiązaliśmy ten problem, instalując dodatkowe osłony i filtry wstępne.
- Lokalizacja chłodni kominowych: W przypadku naszego zakładu, musieliśmy przenieść czerpnię powietrza, gdy okazało się, że znajduje się zbyt blisko chłodni kominowej instalacji chłodzenia wtórnego. Para wodna z chłodni mogła potencjalnie przenosić zanieczyszczenia mikrobiologiczne.
- Źródła intensywnych zapachów: Szczególną uwagę zwracamy na lokalizację wylotów wentylacji sanitarnej czy kuchennej. W jednym przypadku musieliśmy zainstalować dodatkowe filtry z węglem aktywnym, gdy okazało się, że zapachy z pobliskiej stołówki zakładowej przenikają do systemu wentylacyjnego Cleanroomu.
- Istniejące lub planowane budynki w sąsiedztwie: Zawsze bierzemy pod uwagę nie tylko aktualną sytuację, ale także plany rozbudowy. W naszym przypadku musieliśmy przenieść wyrzutnię powietrza, gdy dowiedzieliśmy się o planach budowy wysokiego budynku biurowego w sąsiedztwie.
- Ruch uliczny i parkingi: Lokalizujemy czerpnie z dala od obszarów o dużym natężeniu ruchu samochodowego. W jednym przypadku musieliśmy zainstalować dodatkowe filtry, gdy nowy parking został zlokalizowany zbyt blisko istniejącej czerpni.
- Duże zewnętrzne źródła ciepła: Unikamy lokalizowania czerpni w pobliżu transformatorów, agregatów chłodniczych czy innych urządzeń emitujących duże ilości ciepła, które mogłyby zaburzać pracę systemu klimatyzacji.
Konstrukcja czerpni
Czerpnia powinna być wyposażona w odporną na korozję siatkę ochronną, o maksymalnym wymiarze oczek 20×20 mm. W naszej praktyce stosujemy siatki ze stali nierdzewnej, które są odporne na warunki atmosferyczne i łatwe do czyszczenia.
Kluczowe jest zapewnienie możliwości zewnętrznego czyszczenia mechanicznego czerpni. W naszym zakładzie wprowadziliśmy procedurę regularnego czyszczenia czerpni co najmniej raz na kwartał, a w okresach o zwiększonym zanieczyszczeniu powietrza (np. okres pylenia roślin) – nawet co miesiąc.
Filtry wstępne
Choć nie jest to wymagane przepisami, w naszej praktyce zawsze instalujemy filtry wstępne na czerpniach. Stosujemy filtry klasy G4, które skutecznie zatrzymują większe zanieczyszczenia, takie jak liście, owady czy pyłki roślin. To rozwiązanie znacząco wydłuża żywotność droższych filtrów w centrali wentylacyjnej.
Monitoring jakości powietrza
W krytycznych instalacjach zainstalowaliśmy systemy ciągłego monitoringu jakości powietrza na czerpniach. Mierzymy takie parametry jak stężenie pyłów PM10 i PM2.5, poziom CO2, temperaturę i wilgotność. Dane te są analizowane w czasie rzeczywistym i w przypadku przekroczenia ustalonych progów system automatycznie zwiększa stopień filtracji lub, w skrajnych przypadkach, przełącza się na tryb recyrkulacji powietrza.
Wyrzutnie powietrza
Przy projektowaniu wyrzutni powietrza kluczowe jest zapewnienie, że zużyte powietrze nie będzie ponownie zasysane przez czerpnię. W naszym zakładzie stosujemy zasadę, że wyrzutnia powinna być zlokalizowana co najmniej 10 metrów od czerpni i na wyższym poziomie.
Dodatkowo, w przypadku pomieszczeń o najwyższych klasach czystości (ISO 5 i ISO 6), przed wyrzutem powietrza stosujemy dodatkową filtrację HEPA. To zapobiega potencjalnemu rozprzestrzenianiu się zanieczyszczeń z Cleanroomu do środowiska.
Wnioski i rekomendacje
Z mojego doświadczenia wynika, że prawidłowe zaprojektowanie i utrzymanie czerpni i wyrzutni powietrza jest kluczowe dla efektywnego funkcjonowania systemu wentylacji w pomieszczeniach czystych. Rekomendowałbym:
- Przeprowadzenie szczegółowej analizy lokalizacji przed instalacją czerpni i wyrzutni, uwzględniającej nie tylko aktualne warunki, ale także potencjalne przyszłe zmiany w otoczeniu.
- Instalację systemów monitoringu jakości powietrza na czerpniach, szczególnie w przypadku krytycznych instalacji.
- Regularne inspekcje i czyszczenie czerpni i wyrzutni, co najmniej raz na kwartał.
- Stosowanie filtrów wstępnych na czerpniach, co znacząco wydłuża żywotność droższych filtrów w centrali wentylacyjnej.
- W przypadku pomieszczeń o najwyższych klasach czystości, rozważenie dodatkowej filtracji powietrza przed wyrzutem.
Podsumowując, prawidłowe zaprojektowanie i utrzymanie czerpni i wyrzutni powietrza to kluczowy element w zapewnieniu wysokiej jakości powietrza w pomieszczeniach czystych zgodnie z normą ISO 14644-1. Wymaga to kompleksowego podejścia, uwzględniającego wiele czynników i ciągłego monitoringu.
Tace ociekowe i odprowadzenie kondensatu w pomieszczeniach czystych
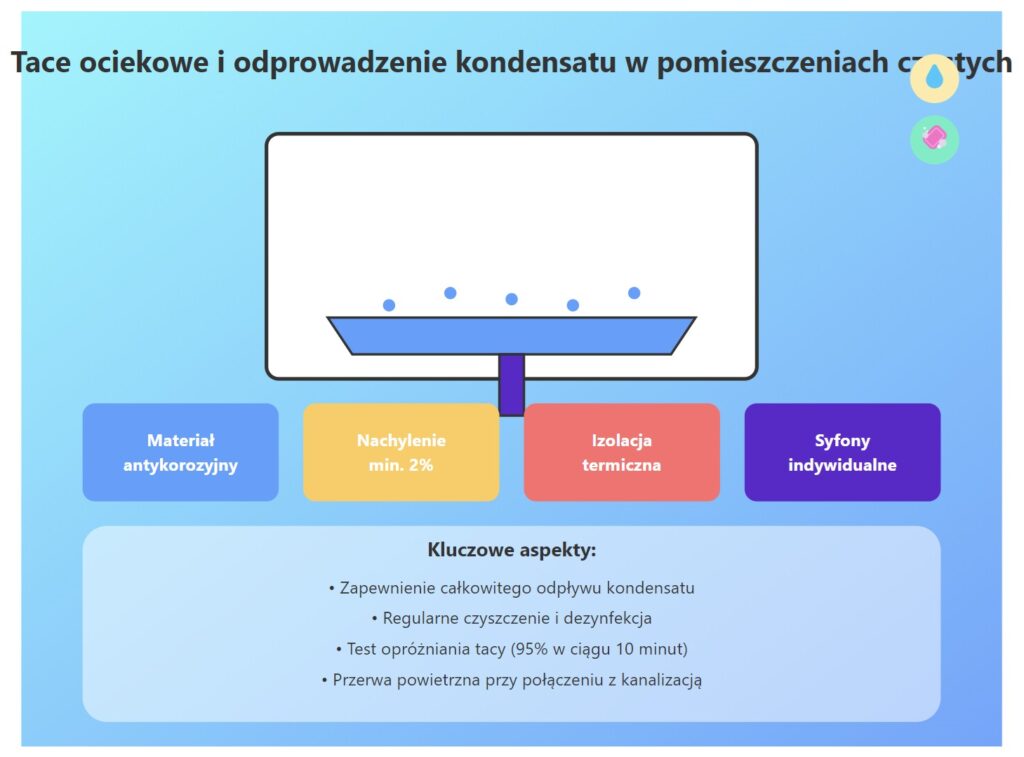
W trakcie mojej 20-letniej kariery w zarządzaniu pomieszczeniach czystych, zrozumiałem, że prawidłowe zaprojektowanie i utrzymanie systemu odprowadzania kondensatu jest kluczowe dla utrzymania higieny i prawidłowego funkcjonowania instalacji klimatyzacyjnych. Szczególnie w środowisku Cleanroom, gdzie nawet najmniejsze zaniedbanie może prowadzić do rozwoju mikroorganizmów i zanieczyszczenia powietrza.
Konstrukcja tac ociekowych
W naszym zakładzie stosujemy następujące zasady dotyczące tac ociekowych:
- Materiał: Wszystkie tace ociekowe pod urządzeniami klimatyzacyjnymi są wykonane z materiałów odpornych na korozję. Najczęściej stosujemy stal nierdzewną 1.4301, która wykazuje doskonałą odporność na korozję i jest łatwa do czyszczenia.
- Kształt: Tace są zaprojektowane tak, aby zapewniać stały i całkowity odpływ kondensatu. Stosujemy odpowiednie nachylenie (minimum 2%) w kierunku odpływu, co zapobiega zastojom wody.
- Izolacja: Wszystkie tace ociekowe są izolowane termicznie, co zapobiega kondensacji na ich zewnętrznej powierzchni.
System odprowadzania kondensatu
Przy projektowaniu systemu odprowadzania kondensatu kierujemy się następującymi zasadami:
- Średnica przewodów: Przewody odprowadzenia skroplin mają średnicę nie mniejszą niż 40 mm. Z doświadczenia wiemy, że mniejsze średnice mogą prowadzić do zatorów i problemów z odpływem.
- Syfony: Odpływy kondensatu z poszczególnych sekcji centrali posiadają osobne syfony. To kluczowe dla zapobiegania przedostawaniu się zanieczyszczeń z jednej sekcji do drugiej.
- Przerwa powietrzna: Połączenie instalacji odprowadzającej kondensat z instalacją kanalizacyjną zawsze wykonujemy z zastosowaniem przerwy powietrznej. Nigdy nie łączymy bezpośrednio odpływu kondensatu z centrali klimatyzacyjnej z systemem kanalizacji. To zapobiega przedostawaniu się zanieczyszczeń z kanalizacji do systemu klimatyzacji.
Testowanie systemu odprowadzania kondensatu
W celu potwierdzenia prawidłowego odpływu kondensatu, przeprowadzamy test zgodnie z zaleceniami normy DIN 1946-4. Procedura wygląda następująco:
- Napełniamy tacę ociekową wodą w ilości 5 litrów na każdy m2 powierzchni tacy.
- Mierzymy czas opróżnienia tacy.
- System uznajemy za prawidłowo działający, jeśli 95% powierzchni tacy ociekowej opróżni się w czasie 10 minut od napełnienia.
Ten test przeprowadzamy podczas odbioru instalacji, a następnie regularnie, co najmniej raz w roku, jako część naszego programu konserwacji prewencyjnej.
Wyzwania i rozwiązania
Jednym z największych wyzwań, z jakimi się spotkałem, było zapobieganie rozwojowi mikroorganizmów w systemie odprowadzania kondensatu. Rozwiązaniem okazało się wprowadzenie kilku kluczowych praktyk:
- Regularne czyszczenie i dezynfekcja: Wprowadziliśmy procedurę kwartalnego czyszczenia i dezynfekcji tac ociekowych oraz syfonów. Używamy do tego celu specjalistycznych środków biobójczych dopuszczonych do stosowania w pomieszczeniach czystych.
- Monitoring wizualny: Personel techniczny ma obowiązek codziennej kontroli wizualnej tac ociekowych pod kątem zastojów wody lub oznak rozwoju mikroorganizmów.
- Automatyczne systemy płukania: W krytycznych instalacjach zainstalowaliśmy automatyczne systemy płukania syfonów, które uruchamiają się regularnie, zapobiegając wysychaniu syfonów i rozwojowi mikroorganizmów.
- Stosowanie materiałów antybakteryjnych: W niektórych przypadkach zdecydowaliśmy się na zastosowanie tac ociekowych z powłoką antybakteryjną, co dodatkowo ogranicza ryzyko rozwoju mikroorganizmów.
Dokumentacja i szkolenia
Prowadzenie dokładnej dokumentacji dotyczącej systemu odprowadzania kondensatu jest kluczowe. W naszym zakładzie dla każdej instalacji prowadzimy kartę, w której zapisujemy:
- Daty i wyniki testów odpływu kondensatu
- Daty czyszczenia i dezynfekcji
- Wszelkie naprawy lub modyfikacje systemu
Ponadto, regularnie szkolimy personel techniczny w zakresie prawidłowej obsługi i konserwacji systemu odprowadzania kondensatu. Szkolenia obejmują zarówno aspekty techniczne, jak i higieniczne.
Wnioski i rekomendacje
Z mojego doświadczenia wynika, że prawidłowe zaprojektowanie i utrzymanie systemu odprowadzania kondensatu jest często niedocenianym, ale kluczowym elementem w utrzymaniu czystości powietrza w Cleanroomach. Rekomendowałbym:
- Stosowanie wysokiej jakości materiałów odpornych na korozję do konstrukcji tac ociekowych.
- Regularne przeprowadzanie testów odpływu kondensatu, co najmniej raz w roku.
- Wdrożenie rygorystycznego programu czyszczenia i dezynfekcji.
- Rozważenie instalacji automatycznych systemów płukania syfonów w krytycznych instalacjach.
- Ciągłe szkolenie personelu technicznego w zakresie prawidłowej obsługi i konserwacji systemu.
Podsumowując, prawidłowe zaprojektowanie i utrzymanie systemu odprowadzania kondensatu to kluczowy element w zapewnieniu wysokiej jakości powietrza w pomieszczeniach czystych zgodnie z normą ISO 14644-1. Wymaga to kompleksowego podejścia, uwzględniającego aspekty techniczne, higieniczne i organizacyjne.
System automatyki instalacji wentylacji i klimatyzacji w pomieszczeniach czystych
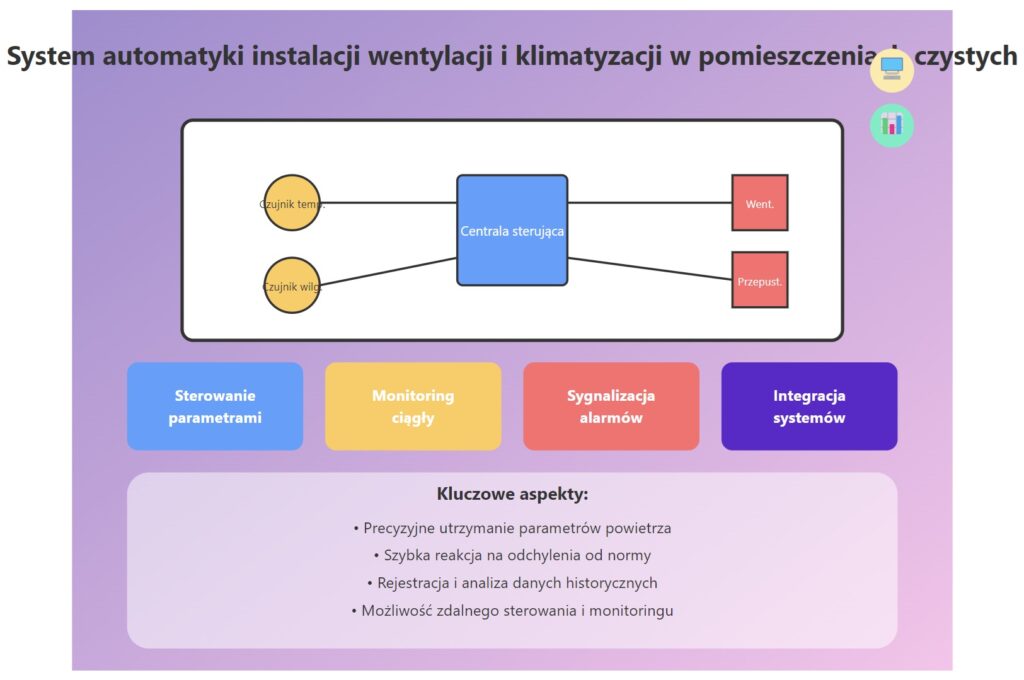
W trakcie mojej 20-letniej kariery w zarządzaniu pomieszczeniami czystymi, zrozumiałem, że zaawansowany system automatyki jest sercem efektywnej instalacji wentylacji i klimatyzacji. To właśnie automatyka zapewnia precyzyjną kontrolę wszystkich parametrów, co jest kluczowe dla utrzymania wymaganej klasy czystości zgodnie z normą ISO 14644-1.
Projektowanie systemu automatyki
W naszym zakładzie, projektant systemu wentylacji i klimatyzacji zawsze umieszcza w projekcie szczegółowe zalecenia dotyczące systemu automatyki. To kluczowe dla zapewnienia, że system będzie spełniał wszystkie wymagania funkcjonalne. Proces projektowania obejmuje następujące etapy:
- Opracowanie szczegółowych założeń do projektu układu automatyki.
- Konsultacje z inwestorem i uzyskanie akceptacji założeń.
- W przypadku wątpliwości, korzystamy z konsultacji rzeczoznawcy budowlanego w zakresie wentylacji i klimatyzacji.
Kluczowe funkcje systemu automatyki
System automatyki wentylacji i klimatyzacji w naszych pomieszczeniach czystych musi spełniać następujące funkcje:
- Utrzymanie parametrów roboczych: System musi zapewniać utrzymanie strumienia objętości powietrza, temperatury i wilgotności względnej powietrza zgodnie ze spełnianą funkcją, przy zmiennych warunkach zewnętrznych i wewnętrznych.
- Sygnalizacja stanów alarmowych: System musi sygnalizować wszelkie stany alarmowe występujące w układzie i im przeciwdziałać. W naszej praktyce okazało się to kluczowe dla szybkiej reakcji na potencjalne problemy.
- Historia zdarzeń: Umożliwiamy śledzenie historii zdarzeń awaryjnych, co pozwala nam na analizę trendów i proaktywne zapobieganie awariom.
- Zabezpieczenie funkcjonowania: System musi zabezpieczać prawidłowe funkcjonowanie centrali/szafy wentylacyjno-klimatyzacyjnej zarówno w okresie jej pracy, jak i postoju.
Specyfika automatyki dla pomieszczeń czystych
System automatyki przeznaczonej dla pomieszczeń czystych musi uwzględniać specyficzne wymagania tych przestrzeni:
- Bezpieczeństwo funkcjonowania: W przypadku wystąpienia awarii, system powinien (w miarę możliwości technicznych) zapewnić utrzymanie mierników funkcjonalności przynajmniej do czasu zakończenia bieżącej produkcji.
- Monitoring parametrów: System musi posiadać instrumenty umożliwiające odczyt aktualnego trybu pracy, aktywnych stanów awaryjnych, wartości temperatury, wilgotności względnej powietrza i aktualnego nadciśnienia powietrza w Cleanroom, bezpośrednio przez personel.
- Ciągły monitoring: System musi zapewniać możliwość stałego monitorowania pracy instalacji przez służby techniczne operatora Cleanroom lub zewnętrzne służby serwisowe.
- Współpraca elementów: System musi zapewniać współpracę wszystkich elementów instalacji wentylacji i klimatyzacji w sposób gwarantujący bezpieczeństwo funkcjonowania oraz ekonomiczną pracę systemu.
- Nadzór nad recyrkulacją: System musi zapewniać stały nadzór nad instalacją recyrkulacji i prawidłową współpracę systemu doprowadzającego powietrze zewnętrzne i recyrkulacyjne.
Wyzwania i rozwiązania
Jednym z największych wyzwań, z jakimi się spotkałem, była integracja systemu automatyki z istniejącymi systemami w zakładzie. Rozwiązaniem okazało się zastosowanie otwartych protokołów komunikacyjnych (takich jak BACnet czy Modbus) oraz wykorzystanie bramek komunikacyjnych do integracji starszych systemów.
Innym wyzwaniem było zapewnienie niezawodności systemu automatyki. W naszej praktyce wprowadziliśmy redundancję kluczowych elementów systemu, takich jak sterowniki czy czujniki. Dodatkowo, zastosowaliśmy systemy zasilania awaryjnego (UPS) dla krytycznych elementów automatyki.
Dostęp do elementów automatyki
Kluczowe jest zapewnienie dostępu do wszystkich elementów wykonawczych automatyki systemu wentylacji i klimatyzacji. W naszym zakładzie odpowiedzialność za to spoczywa na wykonawcy, inspektorze nadzoru budowlanego oraz inspektorze nadzoru budowlanego w branży sanitarnej.
Prawa autorskie i dokumentacja
W naszej praktyce, wykonawca zawsze przekazuje inwestorowi prawa autorskie (wraz z prawem do wykonywania zależnego prawa autorskiego oraz prawem do udzielania zezwoleń na wykonywanie zależnego prawa autorskiego) do kodów źródłowych dla systemów automatyki. To kluczowe dla zapewnienia możliwości modyfikacji i rozwoju systemu w przyszłości.
Dodatkowo, wymagamy przekazania w pełni funkcjonalnych wersji kodów źródłowych, a w przypadku możliwości ich bezpośredniego pobrania ze sterowników, przekazania niezbędnych haseł dostępu pozwalających na ich pobranie oraz modyfikację.
Wnioski i rekomendacje
Z mojego doświadczenia wynika, że zaawansowany system automatyki jest kluczowy dla efektywnego funkcjonowania pomieszczeń czystych. Rekomendowałbym:
- Szczegółowe planowanie systemu automatyki już na etapie projektowania instalacji wentylacji i klimatyzacji.
- Stosowanie otwartych protokołów komunikacyjnych dla łatwiejszej integracji i rozbudowy systemu.
- Wprowadzenie redundancji kluczowych elementów systemu automatyki.
- Zapewnienie możliwości ciągłego monitoringu i zdalnego dostępu do systemu.
- Regularne szkolenia personelu w zakresie obsługi systemu automatyki.
Podsumowując, prawidłowo zaprojektowany i wdrożony system automatyki jest niezbędny dla utrzymania wymaganej klasy czystości w pomieszczeniach czystych zgodnie z normą ISO 14644-1. Wymaga to kompleksowego podejścia, uwzględniającego aspekty techniczne, prawne i organizacyjne.
Ogrzewanie w pomieszczeniach czystych
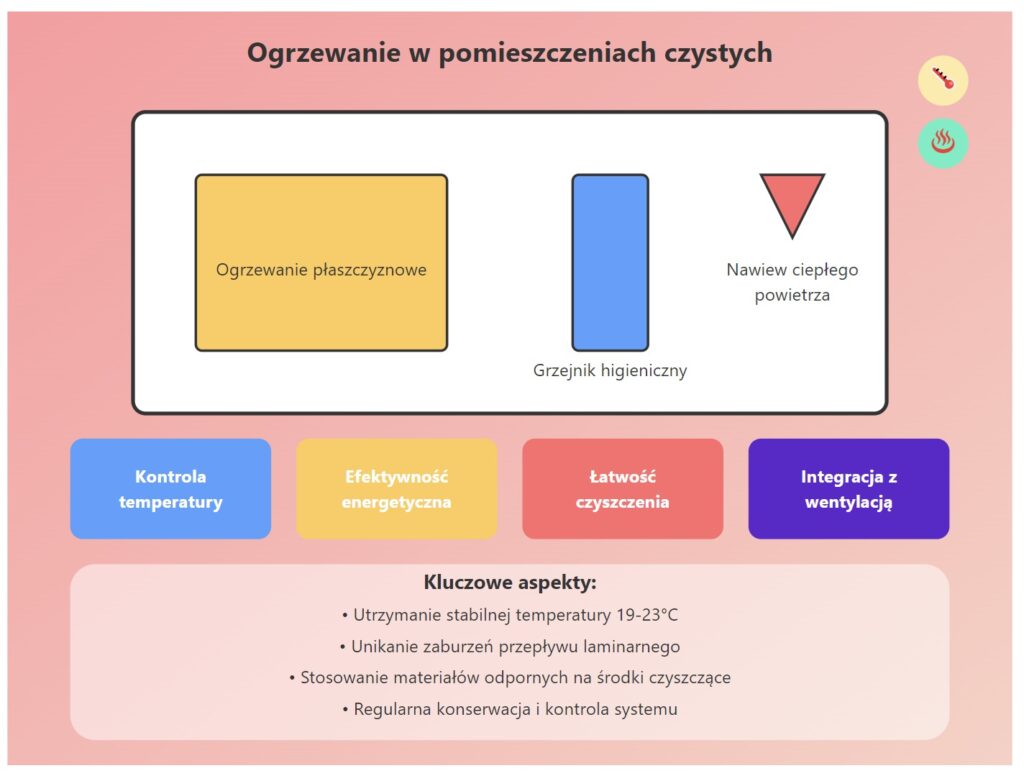
W trakcie mojej 20-letniej kariery w zarządzaniu pomieszczeniami czystymi, kwestia ogrzewania zawsze stanowiła istotne wyzwanie. Odpowiedni system ogrzewania jest kluczowy nie tylko dla komfortu personelu, ale przede wszystkim dla utrzymania stabilnych warunków temperatury, niezbędnych dla wielu procesów produkcyjnych i badawczych.
Wybór systemu ogrzewania
W naszym zakładzie, w zależności od klasy czystości pomieszczenia, stosujemy różne rozwiązania:
- Dla pomieszczeń klasy ISO 5 – ISO 8:
- Preferujemy stosowanie ogrzewania płaszczyznowego. To rozwiązanie sprawdziło się najlepiej, ponieważ nie zaburza przepływu powietrza i nie tworzy dodatkowych powierzchni, które mogłyby gromadzić zanieczyszczenia.
- W szczególnych przypadkach dopuszczamy stosowanie urządzeń o gładkich powierzchniach grzewczych, nieożebrowanych, łatwych do czyszczenia i dezynfekcji (np. grzejników w wykonaniu higienicznym).
- Dla pomieszczeń klasy ISO 5:
- Stosujemy taki system ogrzewania, aby nawiew powietrza poprzez sufit laminarny z zachowaniem odpowiednio niższej temperatury w stosunku do temperatury w pomieszczeniu (o Δt = 1-3 K) nie miał negatywnego wpływu na utrzymanie parametrów komfortu cieplnego.
- Preferujemy ogrzewanie płaszczyznowe ścienne. Ogrzewanie podłogowe, choć efektywne, może mieć negatywny wpływ na utrzymanie stabilności przepływu laminarnego.
Wyzwania i rozwiązania
Jednym z największych wyzwań, z jakimi się spotkałem, było zapewnienie równomiernego rozkładu temperatury w pomieszczeniu czystym bez zaburzania przepływu laminarnego powietrza. Rozwiązaniem okazało się zastosowanie zaawansowanych systemów ogrzewania płaszczyznowego o niskiej bezwładności cieplnej, zintegrowanych z systemem automatyki.
Innym wyzwaniem było zapewnienie łatwości czyszczenia i dezynfekcji elementów grzewczych. W przypadku grzejników higienicznych, wprowadziliśmy specjalne procedury czyszczenia, wykorzystujące środki dezynfekujące dopuszczone do stosowania w pomieszczeniach czystych.
Kontrola i monitoring
W naszej praktyce, kontrola i monitoring systemu ogrzewania są zintegrowane z ogólnym systemem automatyki pomieszczenia czystego. Kluczowe elementy to:
- Ciągły pomiar temperatury w różnych punktach pomieszczenia.
- Automatyczna regulacja mocy grzewczej w zależności od aktualnych potrzeb.
- Monitoring zużycia energii i efektywności systemu ogrzewania.
- Alarmowanie w przypadku odchyleń od zadanych parametrów.
Testy i walidacja
Aby upewnić się, że system ogrzewania nie ma negatywnego wpływu na przepływ powietrza w pomieszczeniu czystym, przeprowadzamy regularne testy wizualizacji przepływu powietrza (testy dymowe) zgodnie z PN-EN ISO 14644-3. Te testy są szczególnie istotne po każdej modyfikacji systemu ogrzewania lub zmianie układu pomieszczenia.
Efektywność energetyczna
W ostatnich latach coraz większą wagę przykładamy do efektywności energetycznej systemów ogrzewania. W naszym zakładzie wprowadziliśmy następujące rozwiązania:
- Zaawansowane systemy odzysku ciepła z powietrza wywiewanego.
- Inteligentne systemy sterowania, które optymalizują pracę systemu ogrzewania w zależności od obecności personelu i aktualnych procesów produkcyjnych.
- Wykorzystanie pomp ciepła do ogrzewania tam, gdzie jest to możliwe i ekonomicznie uzasadnione.
Szkolenia i procedury
Prawidłowa obsługa systemu ogrzewania jest kluczowa dla jego efektywności i trwałości. W naszym zakładzie wprowadziłem program regularnych szkoleń dla personelu technicznego, obejmujący:
- Zasady działania systemów ogrzewania w pomieszczeniach czystych.
- Procedury konserwacji i czyszczenia elementów grzewczych.
- Interpretację danych z systemu monitoringu i automatyki.
- Procedury postępowania w sytuacjach awaryjnych.
Wnioski i rekomendacje
Z mojego doświadczenia wynika, że odpowiedni dobór i utrzymanie systemu ogrzewania jest kluczowe dla efektywnego funkcjonowania pomieszczeń czystych. Rekomendowałbym:
- Preferowanie systemów ogrzewania płaszczyznowego, szczególnie w pomieszczeniach o najwyższych klasach czystości.
- Integrację systemu ogrzewania z ogólnym systemem automatyki pomieszczenia czystego.
- Regularne przeprowadzanie testów wizualizacji przepływu powietrza, aby upewnić się, że system ogrzewania nie zaburza przepływu laminarnego.
- Inwestycję w efektywne energetycznie rozwiązania, które w długiej perspektywie przynoszą oszczędności.
- Regularne szkolenia personelu technicznego w zakresie obsługi i konserwacji systemu ogrzewania.
Podsumowując, prawidłowo zaprojektowany i utrzymany system ogrzewania jest niezbędny dla zapewnienia odpowiednich warunków w pomieszczeniach czystych zgodnie z normą ISO 14644-1. Wymaga to kompleksowego podejścia, uwzględniającego aspekty techniczne, energetyczne i organizacyjne.
Dokumentacja projektowa dla pomieszczeń czystych
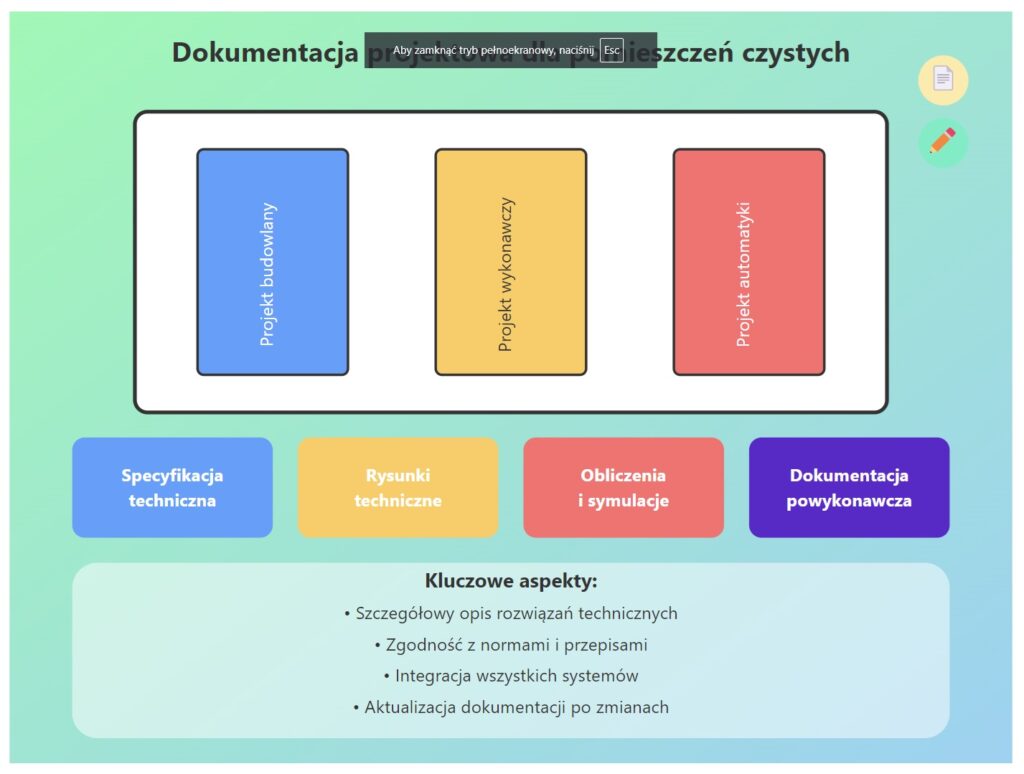
W mojej 20-letniej karierze zarządzania pomieszczeniami czystymi, zrozumiałem, że precyzyjna i kompleksowa dokumentacja projektowa jest fundamentem sukcesu każdego Cleanroom. To nie tylko wymóg prawny, ale przede wszystkim narzędzie zapewniające prawidłowe wykonanie, eksploatację i utrzymanie pomieszczeń czystych zgodnie z normą ISO 14644-1.
Projekt budowlany
Podstawą każdego projektu pomieszczenia czystego jest projekt budowlany. W naszym zakładzie zawsze upewniamy się, że:
- Roboty budowlane są wykonywane na podstawie szczegółowej dokumentacji projektowej.
- Indywidualnie opracowana specyfikacja techniczna wykonania i odbioru robót jest sporządzona zgodnie z wymaganiami Dz.U.2004.202.2072.
To podejście pozwala nam uniknąć wielu problemów na etapie realizacji i późniejszej eksploatacji.
Projekt wykonawczy systemu wentylacji i klimatyzacji
Projekt wykonawczy to kluczowy dokument, który musi zawierać wszystkie niezbędne informacje do realizacji robót. W naszej praktyce, projekt wykonawczy zawsze obejmuje:
- Opis techniczny, zawierający:
- Szczegółowy opis zastosowanych rozwiązań
- Parametry obliczeniowe powietrza zewnętrznego i wewnętrznego
- Klasy czystości powietrza w pomieszczeniu
- Założone nadciśnienie/podciśnienie powietrza
- Założoną prędkość przepływu powietrza
- Parametry obliczeniowe czynników grzewczego i chłodniczego
- Zestawienie zapotrzebowania na energię cieplną i chłodniczą
- Zestawienie strumieni powietrza wentylacyjnego
- Opis układu kaskady ciśnień powietrza
- Zestawienie urządzeń i elementów instalacji wraz z ich specyfikacją
- Zestawienie przewodów wentylacyjnych i kształtek
- Szczegółowe założenia do systemu automatyki instalacji
- Określenie mierników funkcjonalności
- Wytyczne przeciwpożarowe
- Wytyczne dla innych branż
- Część rysunkową, obejmującą:
- Rzuty
- Przekroje
- Schematy rozwiązań (szczególnie schemat działania systemu wentylacji i klimatyzacji dla pomieszczeń klasy ISO 5- ISO 8)
- Obliczenia, w tym:
- Dla pomieszczeń klasy ISO 5: obliczenia doboru wentylatorów nawiewnych i wyciągowych w czterech fazach pracy instalacji (początkowej, nominalnej, końcowej i trybie ograniczonego wydatku)
- Wartości ciśnienia powietrza przed filtrem wysokoskutecznym w odniesieniu do prędkości wypływu powietrza bezpośrednio pod stropem laminarnym
Projekt wykonawczy systemu automatyki
W naszym zakładzie projekt automatyki jest traktowany jako oddzielne, równie ważne opracowanie. Dla pomieszczeń klasy ISO 5 zawiera on:
- Schematy techniczne
- Dane dotyczące zastosowanych komponentów
- Szczegółowy opis realizacji wszystkich funkcji systemu automatyki
- Opis technologii działania systemu z uwzględnieniem wartości zadanych i sposobu ich utrzymania
- Objaśnienie działania algorytmów sterowania poszczególnych urządzeń
- Charakterystykę zastosowanych czujników i urządzeń wykonawczych
Z mojego doświadczenia wynika, że projekt automatyki musi zostać zaakceptowany przez inwestora, projektanta instalacji wentylacji i klimatyzacji, a w szczególnych przypadkach również przez rzeczoznawcę ds. HVAC.
Projekt powykonawczy
Projekt powykonawczy to zaktualizowana wersja projektu wykonawczego, uwzględniająca wszystkie zmiany dokonane podczas realizacji. W naszej praktyce, projekt powykonawczy zawsze zawiera:
- Uaktualnioną część opisową i rysunkową
- Wymagane atesty, aprobaty techniczne, deklaracje zgodności
- Wykaz zastosowanych urządzeń wraz z ich dokumentacją techniczno-ruchową oraz instrukcjami obsługi
- Listę materiałów eksploatacyjnych
Wszystkie istotne zmiany w projekcie powykonawczym muszą być zatwierdzone przez projektanta instalacji.
Wyzwania i rozwiązania
Jednym z największych wyzwań, z jakimi się spotkałem, było zapewnienie spójności dokumentacji między różnymi branżami zaangażowanymi w projekt. Rozwiązaniem okazało się wprowadzenie systemu zarządzania dokumentacją projektową, który umożliwia śledzenie zmian i zapewnia, że wszystkie strony pracują na aktualnych wersjach dokumentów.
Innym wyzwaniem było zapewnienie, że dokumentacja jest zrozumiała nie tylko dla specjalistów, ale także dla personelu operacyjnego. W odpowiedzi na to, wprowadziliśmy praktykę tworzenia uproszczonych instrukcji obsługi i schematów, które są łatwe do zrozumienia dla operatorów.
Wnioski i rekomendacje
Z mojego doświadczenia wynika, że precyzyjna i kompleksowa dokumentacja projektowa jest kluczowa dla sukcesu pomieszczenia czystego. Rekomendowałbym:
- Zaangażowanie doświadczonych projektantów, specjalizujących się w pomieszczeniach czystych.
- Regularne przeglądy dokumentacji na każdym etapie projektu, z udziałem wszystkich zainteresowanych stron.
- Inwestycję w nowoczesne systemy zarządzania dokumentacją projektową.
- Tworzenie uproszczonych instrukcji i schematów dla personelu operacyjnego.
- Regularne aktualizacje dokumentacji powykonawczej, aby odzwierciedlała ona aktualny stan instalacji.
Podsumowując, prawidłowo przygotowana dokumentacja projektowa jest fundamentem dla skutecznego projektowania, realizacji i utrzymania pomieszczeń czystych zgodnie z normą ISO 14644-1. Wymaga to kompleksowego podejścia, uwzględniającego aspekty techniczne, prawne i organizacyjne.
Umowa o roboty budowlane dla pomieszczeń czystych
W trakcie mojej 20-letniej kariery w zarządzaniu pomieszczeniami czystymi, zrozumiałem, że prawidłowo skonstruowana umowa o roboty budowlane jest kluczowym elementem sukcesu projektu Cleanroom. To nie tylko dokument prawny, ale przede wszystkim narzędzie zapewniające jasne oczekiwania i odpowiedzialności wszystkich stron zaangażowanych w projekt.
Kluczowe elementy umowy
W naszym zakładzie, umowa o roboty budowlane dla pomieszczeń czystych zawsze zawiera następujące elementy:
- Odniesienie do oczekiwanej jakości wykonanych robót:
- Odwołanie do specyfikacji technicznej wykonania robót
- Odwołanie do wytycznych dotyczących pomieszczeń czystych
- Odwołanie do warunków technicznych wykonania i odbioru instalacji
- Określenie strony odpowiedzialnej za wykonanie pomiarów i kontroli:
- Wskazanie przedstawiciela Inwestora odpowiedzialnego za nadzór nad prawidłowością przeprowadzenia pomiarów
- Określenie osoby odpowiedzialnej za interpretację wyników pomiarów
- Parametry projektowe instalacji oraz mierniki funkcjonalności:
- Szczegółowe określenie parametrów, które muszą być spełnione, aby instalację uznać za wykonaną prawidłowo i gotową do spełniania przynależnych jej funkcji
- Jasne zdefiniowanie mierników funkcjonalności (umowa o wynik)
- Określenie procedur odbiorowych pomieszczenia czystego
Dodatkowe wymagania dla pomieszczeń o podwyższonych wymaganiach higienicznych
Dla pomieszczeń klasy ISO 5 i wyższej, w umowie zawsze uwzględniamy dodatkowe wymagania:
- Wykonanie przewodów wentylacyjnych z zachowaniem określonej w projekcie klasy szczelności
- Wykonanie komisyjnego testu szczelności instalacji wentylacyjnej:
- Określenie powierzchni przewodów przewidzianej do prób szczelności instalacji
- Wykonanie instalacji z zachowaniem odpowiedniej czystości i/lub wykonanie dodatkowego czyszczenia instalacji wentylacyjnej po montażu
- Wykonanie komisyjnego przeglądu całej struktury budowlanej pomieszczeń klasy ISO 5 przed przystąpieniem do robót wykończeniowych:
- Kontrola szczelności
- Ewentualne doszczelnienie przy użyciu środków dopuszczonych do stosowania w pomieszczeniach o podwyższonych wymaganiach higienicznych
- Montaż filtrów HEPA w nawiewnikach z zachowaniem szczelności ich osadzenia
- Wykonanie komisyjnych pomiarów szczelności zamocowania oraz integralności filtrów HEPA
- Zapewnienie nieprzerwanej pracy instalacji przez 72 godziny przed przystąpieniem do procedur odbiorowych Cleanroom
- Sporządzenie instrukcji eksploatacji instalacji wentylacji, klimatyzacji i chłodniczej
- Wykonanie odbioru technicznego instalacji zawierającego testy i pomiary zgodnie z ISO 14644-3
Wyzwania i rozwiązania
Jednym z największych wyzwań, z jakimi się spotkałem, było precyzyjne zdefiniowanie mierników funkcjonalności, które byłyby jednocześnie ambitne i realistyczne. Rozwiązaniem okazało się przeprowadzenie szczegółowej analizy ryzyka przed sformułowaniem tych mierników, uwzględniającej specyfikę danego projektu i możliwości techniczne.
Innym wyzwaniem było zapewnienie, że wszystkie strony rozumieją techniczne aspekty umowy. W odpowiedzi na to, wprowadziliśmy praktykę organizowania warsztatów technicznych przed podpisaniem umowy, podczas których wszystkie strony mogą omówić i wyjaśnić wszelkie niejasności.
Kwestie prawne
W naszej praktyce, zawsze konsultujemy umowę z doświadczonym prawnikiem specjalizującym się w prawie budowlanym i zagadnieniach związanych z pomieszczeniami czystymi. To pozwala nam uniknąć potencjalnych sporów prawnych w przyszłości.
Zarządzanie zmianami
Z doświadczenia wiem, że podczas realizacji projektu często pojawiają się nieprzewidziane okoliczności wymagające zmian. Dlatego w naszych umowach zawsze uwzględniamy procedury zarządzania zmianami, określające:
- Proces zgłaszania i zatwierdzania zmian
- Osoby upoważnione do zatwierdzania zmian
- Sposób dokumentowania zmian
- Wpływ zmian na harmonogram i budżet projektu
Wnioski i rekomendacje
Z mojego doświadczenia wynika, że precyzyjna i kompleksowa umowa o roboty budowlane jest kluczowa dla sukcesu projektu pomieszczenia czystego. Rekomendowałbym:
- Zaangażowanie doświadczonych prawników i ekspertów technicznych przy formułowaniu umowy
- Przeprowadzenie szczegółowej analizy ryzyka przed określeniem mierników funkcjonalności
- Organizację warsztatów technicznych dla wszystkich stron przed podpisaniem umowy
- Uwzględnienie w umowie szczegółowych procedur zarządzania zmianami
- Regularne przeglądy i aktualizacje umowy w trakcie realizacji projektu
Podsumowując, prawidłowo skonstruowana umowa o roboty budowlane jest fundamentem dla skutecznej realizacji projektu pomieszczenia czystego zgodnie z normą ISO 14644-1. Wymaga to kompleksowego podejścia, uwzględniającego aspekty techniczne, prawne i organizacyjne.
Odbiór instalacji w pomieszczeniach czystych
W mojej 20-letniej karierze zarządzania pomieszczeniami czystymi, proces odbioru instalacji zawsze stanowił krytyczny etap projektu. To moment, w którym teoria spotyka się z praktyką, a wszystkie założenia projektowe poddawane są ostatecznej weryfikacji.
Procedury odbiorowe
W naszym zakładzie, prace odbiorowe dla pomieszczeń czystych zawsze wykonujemy zgodnie z procedurami podanymi w PN-EN 12599 oraz ISO 14644-3. Proces odbioru obejmuje trzy główne etapy:
- Sprawdzenie kompletności wykonanych prac
- Kontrolę działania instalacji
- Pomiary kontrolne
Skład komisji odbiorowej
Z doświadczenia wiem, że skład komisji odbiorowej ma kluczowe znaczenie dla prawidłowego przebiegu odbioru. W przypadku pomieszczeń klasy ISO 5, w komisji zawsze uczestniczą:
- Inwestor i/lub użytkownik
- Projektant
- Wykonawca
- Inspektorzy nadzoru budowlanego wymaganych branż
- Specjalista walidacji
- Specjalista HVAC
Sprawdzenie kompletności wykonanych prac
Ten etap ma na celu wykazanie, że wszystkie roboty związane z montażem instalacji wykonano prawidłowo, zgodnie z projektem oraz obowiązującymi przepisami. Obejmuje on:
- Sprawdzenie zgodności wykonania instalacji z dokumentacją wykonawczą i powykonawczą
- Porównanie sposobu wykonania wszystkich elementów instalacji z zasadami sztuki inżynierskiej
- Sprawdzenie dostępności elementów instalacji dla celów eksploatacji i konserwacji
- Sprawdzenie lokalizacji otworów rewizyjnych
- Sprawdzenie czystości instalacji zgodnie z PN-EN 15780
- Sprawdzenie kompletności dokumentacji powykonawczej
- Sprawdzenie kompletności przekazanych instrukcji eksploatacji systemu
- Sprawdzenie oznakowania wszystkich elementów systemu
Kontrola działania
Kontrolę działania rozpoczynamy od pojedynczych urządzeń i części składowych instalacji, poprzez poszczególne układy, aż do kompletnych instalacji i systemów. Kluczowe elementy to:
- Symulacja stanów awaryjnych dla układu obsługującego pomieszczenia klasy ISO 5
- Kontrola działania systemów redundantnych
- Przeprowadzenie 48-godzinnego testu letniego przy zewnętrznych warunkach temperatury i wilgotności zbliżonych do maksymalnych wartości przyjętych w projekcie
Pomiary odbiorowe
Pomiary kontrolne mają na celu uzyskanie pewności, że instalacja osiąga parametry projektowe. W naszym zakładzie wykonujemy następujące pomiary:
- Pomiar szczelności przewodów wentylacyjnych
- Pomiar parametrów powietrza wewnętrznego: temperatury i wilgotności względnej
- Pomiar strumienia objętości powietrza nawiewanego, wywiewanego i recyrkulacyjnego
- Pomiar poziomu dźwięku A
- Pomiar kaskady ciśnienia powietrza między pomieszczeniami
- Test czystości pyłowej powietrza (walidacja pomieszczenia)
- Badanie szczelności zamocowania i integralności filtrów HEPA
- Pomiar spadku ciśnienia na filtrach HEPA
- Pomiar prędkości opadania strugi pod nawiewem laminarnym
- Wizualizację przepływu powietrza nawiewanego
- Test regeneracji
Wyzwania i rozwiązania
Jednym z największych wyzwań, z jakimi się spotkałem, było zapewnienie stabilnych warunków podczas pomiarów odbiorowych. Rozwiązaniem okazało się wprowadzenie 72-godzinnego okresu ciągłej pracy systemu wentylacji przed przystąpieniem do pomiarów.
Innym wyzwaniem była interpretacja wyników pomiarów w kontekście rzeczywistych warunków pracy pomieszczenia czystego. W odpowiedzi na to, wprowadziliśmy praktykę wykonywania dodatkowych pomiarów podczas symulowanych procesów produkcyjnych.
Dokumentacja odbiorowa
Do protokołu odbioru końcowego robót w pomieszczeniach czystych zawsze załączamy następujące protokoły pomiarowe:
- Protokół z pomiarów badania szczelności przewodów wentylacyjnych
- Protokół z badania czystości instalacji
- Protokoły potwierdzające zapewnienie mierników funkcjonalności na założonym poziomie
- Protokół z wykonania 48-godzinnego testu letniego
- Protokoły badań szczelności instalacji chłodniczych i pomp ciepła
Wnioski i rekomendacje
Z mojego doświadczenia wynika, że precyzyjny i kompleksowy proces odbioru instalacji jest kluczowy dla zapewnienia prawidłowego funkcjonowania pomieszczenia czystego. Rekomendowałbym:
- Szczegółowe planowanie procesu odbioru już na etapie projektowania
- Zaangażowanie wszystkich kluczowych interesariuszy w proces odbiorowy
- Wykonywanie pomiarów w różnych warunkach, w tym podczas symulowanych procesów produkcyjnych
- Dokładną dokumentację wszystkich pomiarów i testów
- Przeprowadzenie szkolenia dla personelu użytkownika bezpośrednio po zakończeniu odbiorów
Podsumowując, prawidłowo przeprowadzony odbiór instalacji jest fundamentem dla skutecznego funkcjonowania pomieszczenia czystego zgodnie z normą ISO 14644-1. Wymaga to kompleksowego podejścia, uwzględniającego aspekty techniczne, organizacyjne i szkoleniowe.
Zalecenia dotyczące eksploatacji instalacji HVAC pomieszczeń czystych
W trakcie mojej 20-letniej kariery w zarządzaniu pomieszczeniami czystymi, zrozumiałem, że prawidłowa eksploatacja instalacji HVAC jest kluczowa dla utrzymania wymaganej klasy czystości i funkcjonalności Cleanroom. Nawet najlepiej zaprojektowany i wykonany system może zawieść, jeśli nie jest odpowiednio eksploatowany i konserwowany.
Zadania zespołu technicznego
W naszym zakładzie, zespół techniczny odpowiedzialny za serwis systemu wentylacji i klimatyzacji ma jasno określone zadania:
- Utrzymanie mierników funkcjonalności systemu na określonym poziomie (zdefiniowanym przez projektanta i/lub inwestora, zawartym w umowie serwisowej).
- Zapewnienie prawidłowej eksploatacji systemu przez zespół posiadający odpowiednie kompetencje.
- Optymalizacja kosztów eksploatacji przy jednoczesnym zachowaniu bezpieczeństwa funkcjonowania.
- Utrzymanie urządzeń i instalacji w należytym stanie technicznym.
- Zapewnienie skutecznego i szybkiego usuwania awarii w przypadku ich wystąpienia.
- Wykonywanie odpowiednich pomiarów i testów określonych w harmonogramie w ustalonych odstępach czasu.
Utrzymanie gwarancji
Aby utrzymać świadczenia gwaranta w okresie gwarancyjnym, zawsze podpisujemy umowę serwisową z serwisem fabrycznym producenta lub jednostką upoważnioną do świadczenia autoryzowanej usługi serwisowej. To kluczowe dla zapewnienia profesjonalnej obsługi i utrzymania gwarancji.
Kompetencje zespołu technicznego
Z mojego doświadczenia wynika, że kompetencje zespołu technicznego są kluczowe dla prawidłowego funkcjonowania pomieszczeń czystych. W naszym zakładzie wymagamy od personelu technicznego:
- Doświadczenia w obsłudze i serwisowaniu urządzeń wentylacji i klimatyzacji w zakresie pomieszczeń czystych.
- Świadectw kwalifikacyjnych z zakresu dozoru i eksploatacji urządzeń elektroenergetycznych.
- Świadectw kwalifikacyjnych uprawniających do obsługi, naprawy oraz demontażu urządzeń i instalacji zawierających substancje kontrolowane.
- Certyfikatów kompetencji w dziedzinie chłodnictwa, pomp ciepła i klimatyzacji.
- Uprawnień budowlanych do kierowania robotami budowlanymi bez ograniczeń w specjalności instalacyjnej.
- Certyfikatów potwierdzających możliwość wykonywania autoryzowanej usługi serwisowej urządzeń danego producenta.
Obsługa bieżąca
Obsługa bieżąca pomieszczeń czystych obejmuje:
- Cykliczną kontrolę trybu i prawidłowości pracy systemu.
- Regularne obchody kontrolne urządzeń, instalacji i systemów.
- Opracowanie i aktualizację harmonogramów bieżących czynności eksploatacyjnych i przeglądów okresowych.
- Opracowanie procedur na wypadek awarii lub przerwania ciągłości pracy urządzeń i instalacji.
- Prowadzenie dokumentacji z regularnych obchodów kontrolnych i przeglądów okresowych.
Konserwacja instalacji
Konserwacja obejmuje wszelkie planowane, regularne działania serwisowe, mające na celu utrzymywanie pracy urządzeń i instalacji na poziomie funkcjonalnym oraz minimalizację ryzyka wystąpienia awarii. Kluczowe elementy to:
- Przeglądy okresowe urządzeń wymagane koniecznością utrzymania ich we właściwym stanie technicznym.
- Przeglądy okresowe urządzeń wymagane z konieczności utrzymania gwarancji producenta.
- Przeglądy urządzeń i instalacji 2 razy w roku (wiosna, jesień) wymagane przez prawo budowlane.
- Przeglądy okresowe urządzeń wymagane przez inne rozporządzenia i ustawy.
Umowa serwisowa
Umowa serwisowa powinna precyzować wszystkie istotne kwestie dotyczące utrzymania urządzeń i instalacji w ruchu. Kluczowe elementy to:
- Określenie strony, która przejmie odpowiedzialność za zapewnienie mierników funkcjonalności na określonym poziomie.
- Określenie warunków dostaw materiałów eksploatacyjnych.
- Określenie trybu przygotowania, terminów i formy procedur awaryjnych.
- Określenie czasu reakcji i czasu naprawy w zależności od wpływu uszkodzonego elementu na utrzymanie mierników funkcjonalności.
Wnioski i rekomendacje
Z mojego doświadczenia wynika, że prawidłowa eksploatacja instalacji HVAC jest kluczowa dla utrzymania wymaganej klasy czystości w pomieszczeniach czystych. Rekomendowałbym:
- Inwestycję w szkolenia i rozwój kompetencji zespołu technicznego.
- Wdrożenie zaawansowanych systemów monitoringu i diagnostyki.
- Regularne przeglądy i aktualizacje procedur eksploatacyjnych.
- Ścisłą współpracę z producentami urządzeń i systemów.
- Prowadzenie szczegółowej dokumentacji wszystkich czynności eksploatacyjnych i serwisowych.
Podsumowując, prawidłowa eksploatacja instalacji HVAC jest fundamentem dla skutecznego funkcjonowania pomieszczenia czystego zgodnie z normą ISO 14644-1. Wymaga to kompleksowego podejścia, uwzględniającego aspekty techniczne, organizacyjne i szkoleniowe.
Podsumowanie i wnioski końcowe
Po 20 latach doświadczenia w zarządzaniu pomieszczeniami czystymi, mogę z pewnością stwierdzić, że utrzymanie odpowiednich warunków w Cleanroomach zgodnie z normą ISO 14644-1 to złożone i wymagające zadanie. Wymaga ono holistycznego podejścia, uwzględniającego wszystkie aspekty od projektowania, przez budowę, aż po codzienną eksploatację.
Kluczowe aspekty zarządzania pomieszczeniami czystymi
- Projektowanie:
- Precyzyjne określenie wymagań dla danej klasy czystości
- Współpraca między projektantami różnych branż
- Uwzględnienie przyszłych potrzeb i możliwości rozbudowy
- Budowa i instalacja:
- Wybór odpowiednich materiałów i urządzeń
- Ścisła kontrola jakości na każdym etapie budowy
- Szczegółowa dokumentacja wszystkich prac
- Systemy HVAC:
- Kluczowa rola w utrzymaniu czystości i parametrów środowiskowych
- Konieczność redundancji kluczowych elementów
- Zaawansowane systemy filtracji i kontroli przepływu powietrza
- Automatyka i kontrola:
- Ciągły monitoring wszystkich kluczowych parametrów
- Szybka reakcja na odchylenia od normy
- Zaawansowane systemy alarmowe i raportowania
- Eksploatacja i konserwacja:
- Regularne przeglądy i konserwacja wszystkich systemów
- Szkolenia personelu technicznego i produkcyjnego
- Szczegółowe procedury dla wszystkich czynności w Cleanroomie
- Dokumentacja:
- Kompletna i aktualna dokumentacja techniczna
- Szczegółowe rejestry wszystkich czynności i zdarzeń
- Regularne audyty i aktualizacje procedur
Wyzwania i rozwiązania
W trakcie mojej kariery napotkałem wiele wyzwań związanych z zarządzaniem pomieszczeniami czystymi. Oto kilka kluczowych problemów i rozwiązań, które okazały się skuteczne:
- Utrzymanie stabilnych parametrów środowiskowych:
- Wyzwanie: Fluktuacje temperatury, wilgotności i ciśnienia.
- Rozwiązanie: Zaawansowane systemy automatyki z algorytmami predykcyjnymi, pozwalające na wyprzedzające reagowanie na zmiany warunków.
- Zapobieganie zanieczyszczeniom:
- Wyzwanie: Wprowadzanie zanieczyszczeń przez personel i materiały.
- Rozwiązanie: Rygorystyczne procedury wejścia i wyjścia, systemy śluz osobowych i materiałowych, regularne szkolenia personelu.
- Efektywność energetyczna:
- Wyzwanie: Wysokie koszty energii związane z utrzymaniem Cleanroomów.
- Rozwiązanie: Systemy odzysku ciepła, optymalizacja pracy systemów HVAC w zależności od aktualnego obciążenia, wykorzystanie energooszczędnych technologii.
- Zgodność z normami i regulacjami:
- Wyzwanie: Ciągłe zmiany w przepisach i normach.
- Rozwiązanie: Ścisła współpraca z organami regulacyjnymi, regularne audyty, elastyczne systemy pozwalające na szybkie dostosowanie do nowych wymagań.
- Ciągłość operacji:
- Wyzwanie: Minimalizacja przestojów związanych z konserwacją i awariami.
- Rozwiązanie: Systemy redundantne, predykcyjne systemy konserwacji, szczegółowe plany awaryjne.
Przyszłe trendy
Patrząc w przyszłość, widzę kilka kluczowych trendów, które będą kształtować zarządzanie pomieszczeniami czystymi:
- Inteligentne systemy zarządzania budynkiem (BMS) wykorzystujące sztuczną inteligencję i uczenie maszynowe.
- Zwiększone wykorzystanie robotyki i automatyzacji w celu minimalizacji obecności ludzi w krytycznych obszarach.
- Rozwój nowych materiałów o właściwościach antybakteryjnych i łatwych do czyszczenia.
- Większy nacisk na zrównoważony rozwój i efektywność energetyczną.
- Wykorzystanie technologii rzeczywistości rozszerzonej (AR) do szkoleń i wsparcia technicznego.
Końcowe refleksje
Zarządzanie pomieszczeniami czystymi to nieustanne wyzwanie, ale także niezwykle satysfakcjonujące zadanie. Kluczem do sukcesu jest ciągłe doskonalenie, otwartość na nowe technologie i rozwiązania, oraz ścisła współpraca między wszystkimi zaangażowanymi stronami – od projektantów, przez personel techniczny, aż po użytkowników końcowych.
Pomieszczenia czyste odgrywają kluczową rolę w wielu gałęziach przemysłu i nauki, od produkcji farmaceutycznej, przez elektronikę, aż po badania kosmiczne. Dlatego tak ważne jest, abyśmy jako specjaliści w tej dziedzinie nieustannie podnosili nasze kwalifikacje i dzielili się wiedzą.
Jestem przekonany, że przestrzegając rygorystycznych standardów, takich jak ISO 14644-1, i jednocześnie pozostając otwartym na innowacje, możemy zapewnić, że pomieszczenia czyste będą nadal odgrywać kluczową rolę w rozwoju technologii i nauki, przyczyniając się do postępu ludzkości.
Q: Co to jest pomieszczenie typu clean room?
A: Pomieszczenie typu clean room, zwane też pomieszczeniem czystym, to specjalnie zaprojektowana przestrzeń, w której kontroluje się stężenie cząstek unoszących się w powietrzu. Pomieszczenia te są wykorzystywane w różnych branżach, gdzie konieczne jest utrzymanie wysokiego poziomu czystości, np. w przemyśle farmaceutycznym, elektronicznym czy kosmicznym. Clean roomy są projektowane i zarządzane zgodnie z normą ISO 14644, która określa klasyfikację czystości pomieszczeń.
Q: Jakie są klasy czystości pomieszczeń według normy ISO 14644-1?
A: Norma ISO 14644-1, opracowana przez Międzynarodową Organizację Normalizacyjną, definiuje 9 klas czystości pomieszczeń, od ISO 1 (najczystsza) do ISO 9 (najmniej czysta). Klasyfikacja ta opiera się na maksymalnej dopuszczalnej liczbie cząstek o określonych rozmiarach na jednostkę objętości powietrza. Im niższa klasa ISO, tym mniej cząstek stałych jest dozwolonych w powietrzu pomieszczenia czystego.
Q: Jakie są kluczowe wymagania dotyczące projektowania pomieszczeń typu clean room?
A: Projektowanie pomieszczeń typu clean room musi uwzględniać wiele czynników, zgodnie z normą ISO 14644-4. Kluczowe wymagania obejmują: odpowiedni system filtracji powietrza, kontrolę ciśnienia, temperaturę i wilgotność, materiały konstrukcyjne łatwe do czyszczenia i nie generujące cząstek, śluzy powietrzne przed wejściem do pomieszczenia czystego, specjalne systemy oświetlenia i odpowiednie rozwiązania dla personelu (np. odzież ochronna). Należy także zaprojektować systemy monitorowania i alarmowania, aby stale kontrolować parametry czystości.
Q: Jak należy przygotować się przed wejściem do pomieszczenia czystego?
A: Przed wejściem do pomieszczenia czystego należy przejść przez śluzę powietrzną i zastosować odpowiednie procedury. Typowe kroki obejmują: założenie specjalnej odzieży ochronnej (kombinezon, rękawiczki, ochraniacze na buty, czepek), oczyszczenie rąk i przedmiotów wnoszonych do pomieszczenia, przejście przez maty klejące usuwające zanieczyszczenia z obuwia. W niektórych przypadkach może być wymagane dodatkowe czyszczenie przy użyciu strumienia powietrza (air shower). Celem tych działań jest zminimalizowanie liczby cząstek wnoszonych do pomieszczenia czystego.
Q: Jakie są główne różnice między normami ISO 14644 a GMP w kontekście pomieszczeń czystych?
A: Normy ISO 14644 i GMP (Good Manufacturing Practice) mają różne zastosowania w kontekście pomieszczeń czystych. ISO 14644 to międzynarodowy standard opracowany przez Międzynarodową Organizację Normalizacyjną, który skupia się na klasyfikacji czystości powietrza i procedurach kontroli w pomieszczeniach czystych. Z kolei GMP to zestaw wytycznych stosowanych głównie w przemyśle farmaceutycznym i spożywczym, koncentrujących się na zapewnieniu jakości i bezpieczeństwa produktów. GMP uwzględnia nie tylko czystość powietrza, ale także inne aspekty produkcji, takie jak dokumentacja, kontrola jakości czy szkolenia personelu.
Q: Jak często należy monitorować i weryfikować czystość pomieszczenia typu clean room?
A: Częstotliwość monitorowania i weryfikacji czystości pomieszczenia typu clean room zależy od jego klasy czystości i wymagań branżowych. Zgodnie z normą ISO 14644-2, należy przeprowadzać regularne testy i monitorowanie. Dla większości klas czystości zaleca się przeprowadzanie pełnej reklasyfikacji co najmniej raz w roku. Jednak ciągłe monitorowanie parametrów, takich jak liczba cząstek w powietrzu, ciśnienie, temperatura i wilgotność, powinno odbywać się znacznie częściej, nawet w czasie rzeczywistym, aby zapewnić stałe utrzymanie wymaganych warunków.
Q: Jakie są najważniejsze procedury czyszczenia i konserwacji w pomieszczeniach typu clean room?
A: Procedury czyszczenia i konserwacji w pomieszczeniach typu clean room są kluczowe dla utrzymania wymaganej klasy czystości. Obejmują one: regularne czyszczenie wszystkich powierzchni przy użyciu specjalistycznych środków czyszczących i technik, które nie generują dodatkowych cząstek; stosowanie dedykowanych narzędzi i materiałów czyszczących; regularną wymianę filtrów powietrza; konserwację systemów wentylacji i klimatyzacji; okresowe czyszczenie lub wymianę odzieży ochronnej. Wszystkie te działania muszą być wykonywane zgodnie z ustalonymi protokołami i dokumentowane, aby zapewnić zgodność z normami ISO 14644 i innymi stosownymi regulacjami.
Q: Jak zapewnić sterylność w pomieszczeniach czystych najwyższej klasy?
A: Zapewnienie sterylności w pomieszczeniach czystych najwyższej klasy wymaga rygorystycznych procedur. Kluczowe aspekty to: zastosowanie zaawansowanych systemów filtracji powietrza HEPA lub ULPA, utrzymanie nadciśnienia w pomieszczeniu, użycie materiałów odpornych na środki dezynfekujące, regularna sterylizacja powierzchni i sprzętu (np. przy użyciu promieniowania UV lub środków chemicznych), ścisła kontrola dostępu personelu, stosowanie sterylnej odzieży ochronnej. Dodatkowo, wszystkie materiały wprowadzane do pomieszczenia muszą być odpowiednio sterylizowane. Należy również regularnie przeprowadzać testy mikrobiologiczne, aby potwierdzić skuteczność procedur sterylizacji.
Here’s the FAQ in Polish language, formatted as requested:
Q: Jak definiuje się pomieszczenia czyste zgodnie z normą ISO?
A: Zgodnie z normą ISO 14644-4, pomieszczenia czyste i związane z nimi środowiska kontrolowane to przestrzenie, w których kontrolowana jest koncentracja cząstek znajdujących się w powietrzu. Norma ta dzieli pomieszczenia na dziewięć kategorii czystości, od ISO klasy 1 (najczystsze) do ISO klasy 9.
Q: Jakie są kluczowe czynniki przy projektowaniu pomieszczenia czystego lub strefy czystej?
A: Projektując clean room należy wziąć pod uwagę kilka kluczowych czynników: system filtracji powietrza, kontrolę ciśnienia, materiały wykończeniowe, system śluz powietrznych, oraz procedury czyszczenia i konserwacji. Istotne jest również zapewnienie odpowiedniego rozkładu przestrzeni i przepływu personelu.
Q: Jak kontroluje się liczbę cząstek stałych w pomieszczeniu czystym?
A: Kontrola cząstek stałych w pomieszczeniu czystym odbywa się poprzez zastosowanie zaawansowanych systemów filtracji powietrza, utrzymanie nadciśnienia w pomieszczeniu, stosowanie odpowiednich materiałów i odzieży ochronnej, oraz regularne monitorowanie i czyszczenie. Kluczowe jest również ograniczenie ruchu personelu i materiałów.
Q: Jakie branże najczęściej korzystają z pomieszczeń czystych?
A: Pomieszczenia czyste są szeroko wykorzystywane w branżach takich jak: przemysł farmaceutyczny, biotechnologia, produkcja mikroelektroniki, nanotechnologia, przemysł kosmiczny, oraz w zaawansowanych laboratoriach badawczych. Wszędzie tam, gdzie konieczne jest wytwarzanie produktów w środowisku o kontrolowanej czystości.
Q: Jak zapewnić sterylność w pomieszczeniu czystym?
A: Aby zapewnić sterylność w pomieszczeniu czystym, należy stosować rygorystyczne procedury czyszczenia i dezynfekcji, używać odpowiednich środków chemicznych, regularnie monitorować poziom czystości, kontrolować przepływ powietrza i ciśnienie, oraz szkolić personel w zakresie właściwych praktyk higieny. Ważne jest również stosowanie sterylnych materiałów i narzędzi.
Q: Jakie są podstawowe zasady zachowania higieny powietrza w pomieszczeniach czystych?
A: Podstawowe zasady higieny powietrza w pomieszczeniach czystych obejmują: utrzymanie odpowiedniego przepływu powietrza, regularna wymiana filtrów HEPA, kontrola wilgotności i temperatury, minimalizacja ruchu personelu, stosowanie odpowiedniej odzieży ochronnej, oraz regularne czyszczenie i dezynfekcja wszystkich powierzchni.
Q: Jak należy przygotować się przed wejściem do pomieszczenia czystego?
A: Przed wejściem do pomieszczenia czystego należy dokładnie oczyścić ciało, założyć odpowiednią odzież ochronną (kombinezon, rękawiczki, ochraniacze na buty, czepek), przejść przez śluzę powietrzną, a w niektórych przypadkach również przez komorę z nadmuchem powietrza. Ważne jest też przestrzeganie procedur dekontaminacji i minimalizacja wnoszonych przedmiotów.
Q: Jak kontroluje się przepływ powietrza i ciśnienia podczas dostępu do pomieszczenia czystego?
A: Kontrola przepływu powietrza i ciśnienia w pomieszczeniu czystym odbywa się poprzez zastosowanie systemów wentylacji z filtrami HEPA, utrzymanie gradientu ciśnień między pomieszczeniami (wyższe ciśnienie w czystszych obszarach), oraz wykorzystanie śluz powietrznych. Systemy te są stale monitorowane i regulowane, aby zapewnić właściwe warunki.
Q: Co to są klasy czystości powietrza i jak są klasyfikowane?
A: Klasy czystości powietrza definiują poziom zanieczyszczeń w pomieszczeniach czystych, a klasyfikacja opiera się na stężeniu cząsteczek w powietrzu. Klasyfikacja czystości powietrza na podstawie norm ISO określa, jakie wymagania muszą być spełnione dla danej klasy czystości powietrza.
Q: Jakie są różnice między pomieszczeniami czystymi w przemyśle farmaceutycznym a produkcyjnym?
A: Pomieszczenia czyste w przemyśle farmaceutycznym muszą spełniać surowsze normy dotyczące czystości powietrza i kontroli zanieczyszczeń niż te w przemyśle produkcyjnym. Dobrej praktyki wytwarzania (GMP) są kluczowe w farmacji, aby zapewnić bezpieczeństwo i skuteczność produktów.
Q: Jakie są zalety stosowania filtrów HEPA w pomieszczeniach czystych?
A: Filtry HEPA są skuteczne w usuwaniu cząsteczek o wielkości 0,3 mikrona i większych, co pozwala na utrzymanie wysokiej czystości powietrza w pomieszczeniach czystych. Dzięki filtracji powietrza z pomieszczenia, są one kluczowym elementem w budowie pomieszczeń czystych.
Q: Jakie działania są podejmowane, aby kontrolować zanieczyszczenia w pomieszczeniach czystych?
A: Kontrola zanieczyszczeń w pomieszczeniach czystych obejmuje regularne monitorowanie jakości powietrza, stosowanie filtrów HEPA oraz ścisłe przestrzeganie procedur dotyczących czystości pomieszczeń. Ważne są również procedury dotyczące wprowadzania materiałów do pomieszczeń.
Q: Jakie są wymagania dotyczące budowy pomieszczeń czystych?
A: Budowa pomieszczeń czystych wymaga zastosowania odpowiednich materiałów, które są łatwe do czyszczenia oraz nie emitują zanieczyszczeń. Powierzchnie pomieszczenia powinny być gładkie i odporne na działanie środków czyszczących, a także odpowiednio zaprojektowane, aby umożliwić efektywną filtrację.
Q: Jakie są kluczowe elementy dobrej praktyki wytwarzania w kontekście czystych pomieszczeń?
A: Kluczowe elementy dobrej praktyki wytwarzania obejmują ścisłe przestrzeganie procedur czyszczenia, monitorowanie jakości powietrza oraz szkolenie personelu w zakresie obsługi pomieszczeń czystych. Ważne jest także regularne audytowanie procesów, aby zapewnić zgodność z wymaganiami dotyczącymi czystości powietrza.
Q: Jakie czynniki wpływają na klasyfikację pomieszczeń czystych?
A: Klasyfikacja pomieszczeń czystych zależy od wielu czynników, w tym od stężenia cząsteczek w powietrzu, rodzaju zastosowanych filtrów, a także od procedur czyszczenia i kontroli zanieczyszczeń. Klasyfikacja czystości powietrza na podstawie norm ISO dostarcza wytycznych dotyczących tych aspektów.
Q: Jakie są najczęstsze źródła zanieczyszczeń w pomieszczeniach czystych?
A: Najczęstsze źródła zanieczyszczeń w pomieszczeniach czystych to personel, materiały wprowadzane do pomieszczeń, a także urządzenia i maszyny. Dlatego kontrola zanieczyszczeń oraz stosowanie odpowiednich procedur i filtrów HEPA są kluczowe dla utrzymania czystego powietrza.